Exploring the Advantages of Using Coordinate Measuring Machines in Global Manufacturing
In today's rapidly evolving manufacturing landscape, precision and quality control have become paramount. As businesses strive to enhance their operational efficiency and product reliability, the significance of advanced measuring technologies cannot be overstated. According to a recent report by MarketsandMarkets, the global coordinate measuring machine (CMM) market is projected to grow from USD 2.17 billion in 2021 to USD 3.49 billion by 2026, at a CAGR of 10.1%. This growth is driven by a rising demand for quality assurance in manufacturing processes, particularly in sectors such as aerospace, automotive, and consumer electronics.
The adoption of Coordinate Measuring Machines is transforming the way manufacturers approach quality control, providing them with unparalleled accuracy and speed in measurement processes. By incorporating CMM technology, manufacturers can reduce inspection times, minimize errors, and enhance overall productivity. A study conducted by the National Institute of Standards and Technology (NIST) highlights that the implementation of advanced measurement technologies, including CMMs, can lead to an average reduction of 30% in rework costs and an increase of up to 25% in general production efficiency. As the manufacturing industry continues to globalize, the integration of Coordinate Measuring Machines will be pivotal in maintaining competitive advantage and achieving sustainable growth.
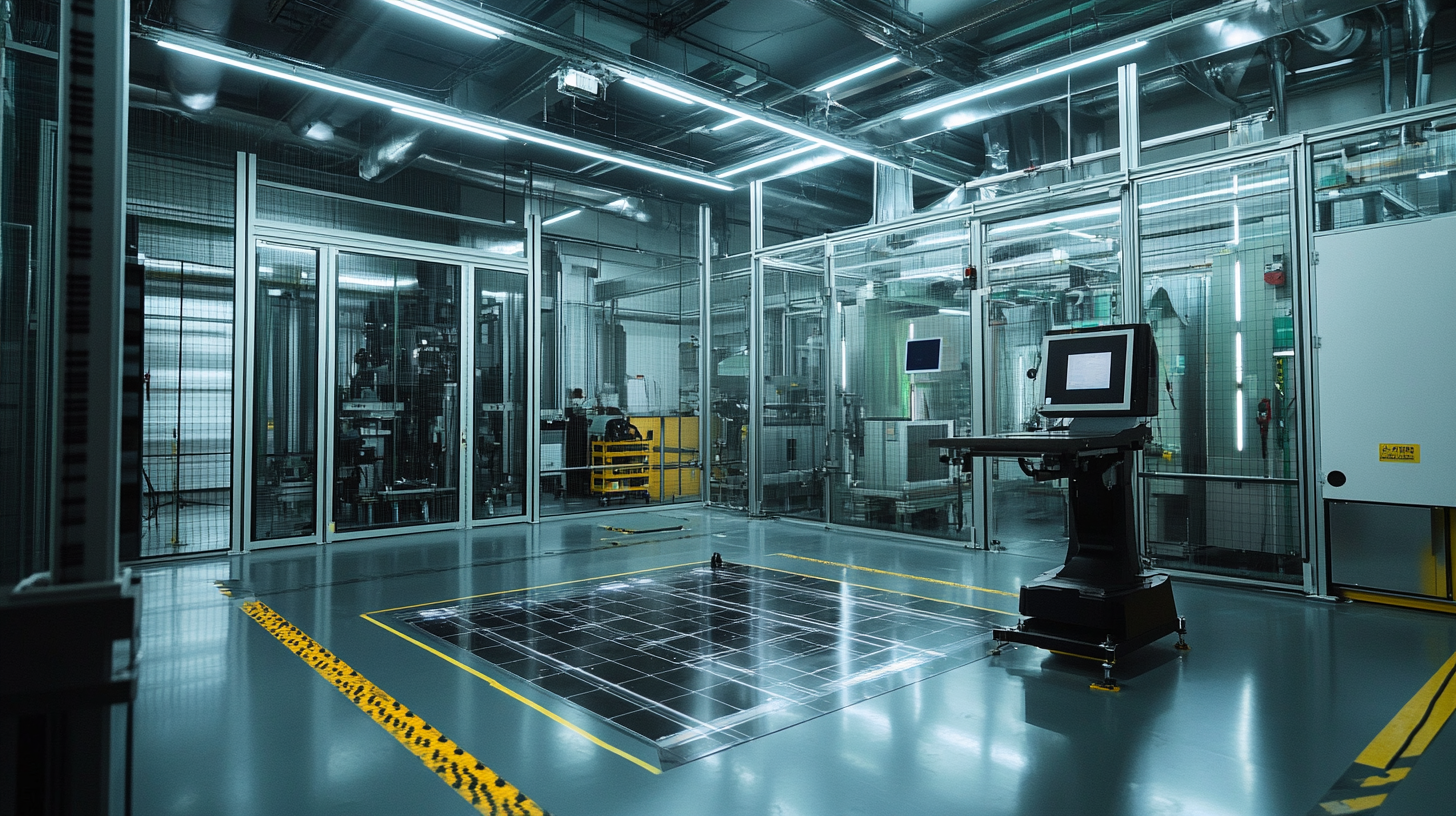
Benefits of Precision: How CMMs Enhance Quality Control in Manufacturing
In today's competitive manufacturing landscape, precision and quality control are paramount. Coordinate Measuring Machines (CMMs) are revolutionizing how manufacturers approach quality assurance. According to a report by MarketsandMarkets, the global CMM market is projected to reach $2.78 billion by 2025, driven by increasing demand for quality measurement across various industries. These advanced measurement systems significantly reduce the uncertainties associated with product dimensions and tolerances, ensuring that manufactured parts meet stringent specifications.
The enhanced accuracy provided by CMMs leads to a higher level of quality control. A study from NIST indicates that manufacturers employing CMM technology experience up to a 60% reduction in measurement errors compared to traditional methods. This not only minimizes scrap and rework costs but also boosts customer satisfaction by delivering high-quality products consistently. Moreover, CMMs can rapidly inspect complex geometries, allowing for a more comprehensive analysis of manufacturing processes and improved decision-making.
Integrating CMMs into the manufacturing workflow enables real-time data collection and analysis, which is imperative for continuous improvement. As per a survey by the American Society for Quality, organizations utilizing advanced measurement technology report a 25-30% increase in process efficiency. By harnessing the benefits of CMMs, manufacturers can ensure that quality is not just an aim but a standard, paving the way for innovation and competitiveness in the global market.
Boosting Productivity: The Role of CMMs in Streamlining Production Processes
In the evolving landscape of global manufacturing, the integration of Coordinate Measuring Machines (CMMs) is proving to be a game-changer, particularly in streamlining production processes. With advancements in automation and robotics, the efficiency and accuracy of CMMs have seen significant improvements. According to a recent market report, the global CMM market size is projected to reach USD 3.5 billion by 2027, highlighting the growing recognition of these machines as essential tools for manufacturers aiming to boost productivity.
CMMs equipped with state-of-the-art software can now process measurements in real time, enabling quicker decision-making and minimizing errors. The implementation of IoT technology allows for seamless data integration, enhancing the ability to monitor production processes continuously. This technological synergy not only reduces downtime but also optimizes resource allocation, ensuring that companies can maintain high output levels while managing costs effectively.
Moreover, the rise in automation within CMMs has redefined quality control in manufacturing. Automated systems can perform high-speed measurements with unparalleled precision, directly impacting the overall product quality and consistency. As manufacturers increasingly turn to these advanced solutions, the role of CMMs in fostering innovation and operational excellence continues to expand, marking a pivotal shift in how industries approach production efficiencies.
Cost Efficiency: Reducing Waste and Increasing Profit Margins with CMM Technology
The implementation of Coordinate Measuring Machines (CMM) in global manufacturing is reshaping cost efficiency by minimizing waste and enhancing profit margins. According to a report by the Aberdeen Group, organizations utilizing CMM technology have achieved a reduction in manufacturing costs by up to 30%. This significant cost saving is primarily attributed to the precise measurements that CMMs provide, enabling manufacturers to identify defects early in the production process. By catching errors at the initial stage, companies avoid expensive rework or scrap costs, further streamlining their operations.
Moreover, a white paper from the National Institute of Standards and Technology (NIST) emphasizes that CMMs can reduce inspection time by 50% compared to traditional manual measurement methods. This not only accelerates the production process but also frees up valuable resources that can be allocated to other critical areas, thus increasing overall productivity. The integration of CMM technology not only promotes accuracy but also fosters a culture of continuous improvement within manufacturing processes.
The financial impact is evident: a study by PricewaterhouseCoopers shows that companies employing advanced measurement techniques, including CMM, reported a 20% increase in profit margins over three years. By investing in CMM technology, manufacturers are not only improving their operational efficiency but also positioning themselves to compete more effectively in the global market. With the growing trend of digital transformation in manufacturing, the adoption of CMM is proving essential for companies looking to thrive and expand their market share.
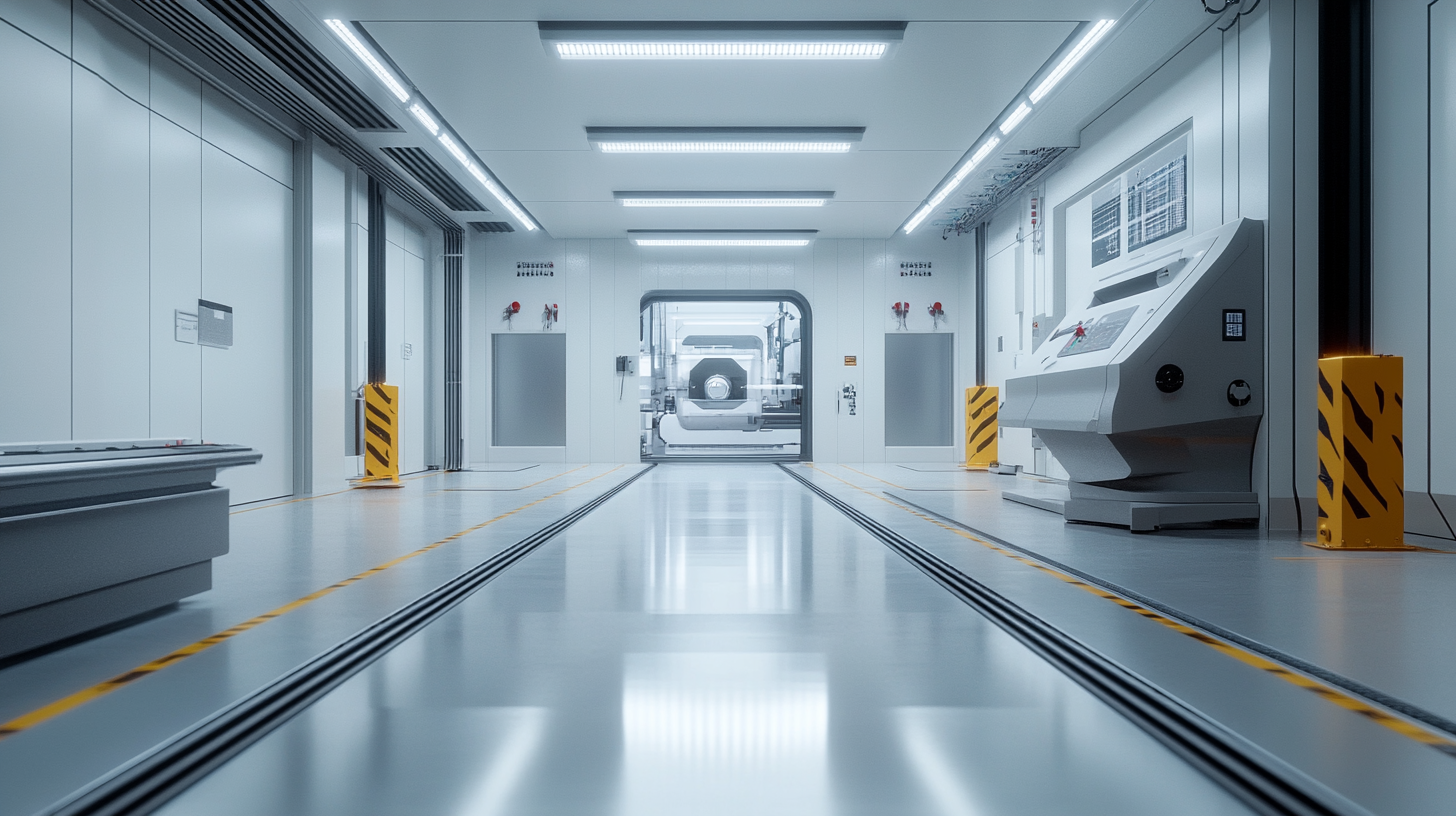
Global Standards: Ensuring Compliance and Consistency through Coordinate Measuring
In the realm of global manufacturing, adherence to international standards is paramount for ensuring product quality and operational efficiency. Coordinate Measuring Machines (CMMs) play a crucial role in this regard, enabling manufacturers to achieve compliance with various industry standards such as ISO 9001 and AS9100. According to a report by MarketsandMarkets, the global CMM market is expected to grow from USD 2.3 billion in 2020 to USD 3.5 billion by 2025, reflecting a heightened focus on quality assurance and precision measurement across various sectors.
CMMs facilitate the accurate measurement of complex geometries and components, which is essential for manufacturers aiming to meet rigorous global standards. By employing either contact or non-contact measurement techniques, these machines provide precise data that helps in the validation of dimensions and tolerances. The ability to attain high repeatability—often within 0.001mm—ensures that manufacturers can consistently produce items that meet specified requirements. Furthermore, utilizing CMMs can streamline production processes, reduce waste, and lead to better compliance with environmental standards, bolstering a company's reputation in the marketplace.
Moreover, the integration of CMMs with advanced software solutions allows for real-time data analysis and reporting, enabling manufacturers to monitor compliance continuously. This aligns with findings from the International Organization for Standardization (ISO), which notes that companies adhering to structured quality management systems are 20% more likely to report high levels of operational efficiency. Thus, the implementation of CMM technology is not merely an investment in measurement capabilities; it is a strategic move towards achieving and maintaining compliance in an increasingly competitive global market.
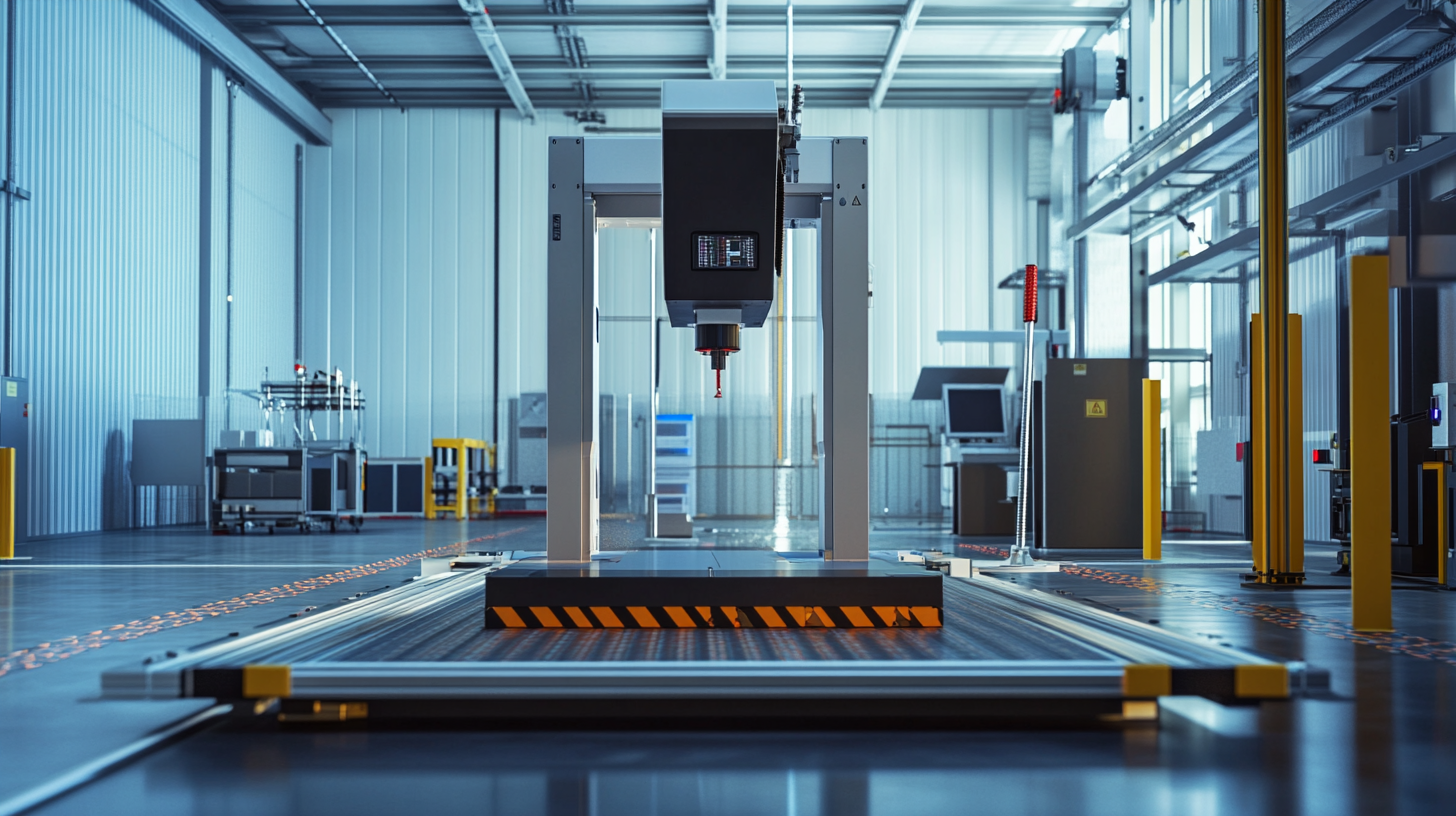
Future Trends: Innovations in CMM Technology and Their Impact on the Manufacturing Industry
The coordinate measuring machine (CMM) market is poised for significant growth, anticipated to reach substantial figures by 2030. As manufacturers increasingly rely on precise measurements for quality assurance, innovations in CMM technology are crucial in meeting industry demands. Recent analyses reveal that the integration of advanced technologies such as automation and the Internet of Things (IoT) is enhancing the efficiency and accuracy of CMMs, making them indispensable tools in modern manufacturing processes.
Future trends indicate that the CMM market will benefit greatly from advancements in artificial intelligence and digital twin technology. These innovations, highlighted in recent industry showcases, suggest that data-driven automation will allow manufacturers to achieve unprecedented levels of flexibility and optimization. As the CMM evolves within the framework of smart manufacturing, its role in quality control and productivity improvements becomes increasingly prominent, with expert reports indicating a substantial rise in adoption across various sectors.
Moreover, the segmentation of the CMM market, which includes fixed and portable types, is expected to cater to diverse industry verticals like automotive and aerospace. This segmentation aligns with the growing demand for customizable solutions, directly influenced by the rapid evolution of automation and robotics technologies. As CMMs become more efficient and accurate, they are not only streamlining quality control processes but also reinforcing their essential role in the global manufacturing landscape.