Exploring Options: What to Consider When Choosing Your Next CNC Tool Room Lathe
Choosing the right CNC tool room lathe is a critical decision that can significantly impact the efficiency and quality of your machining projects. With a myriad of options available in the market, it's essential to understand the key features and specifications that differentiate one model from another. Whether you are a seasoned machinist or a newcomer to the industry, knowing what to consider when selecting your next CNC tool room lathe can help you make an informed choice that aligns with your specific needs and budget.
As you embark on this journey to explore various CNC tool room lathes, it's important to evaluate factors such as precision, durability, ease of operation, and the range of capabilities offered by each model. In this blog, we will delve into the crucial aspects that should influence your decision-making process, ensuring that you will find a CNC tool room lathe that not only meets your current requirements but also has the potential to support your future projects as technology and demands evolve.
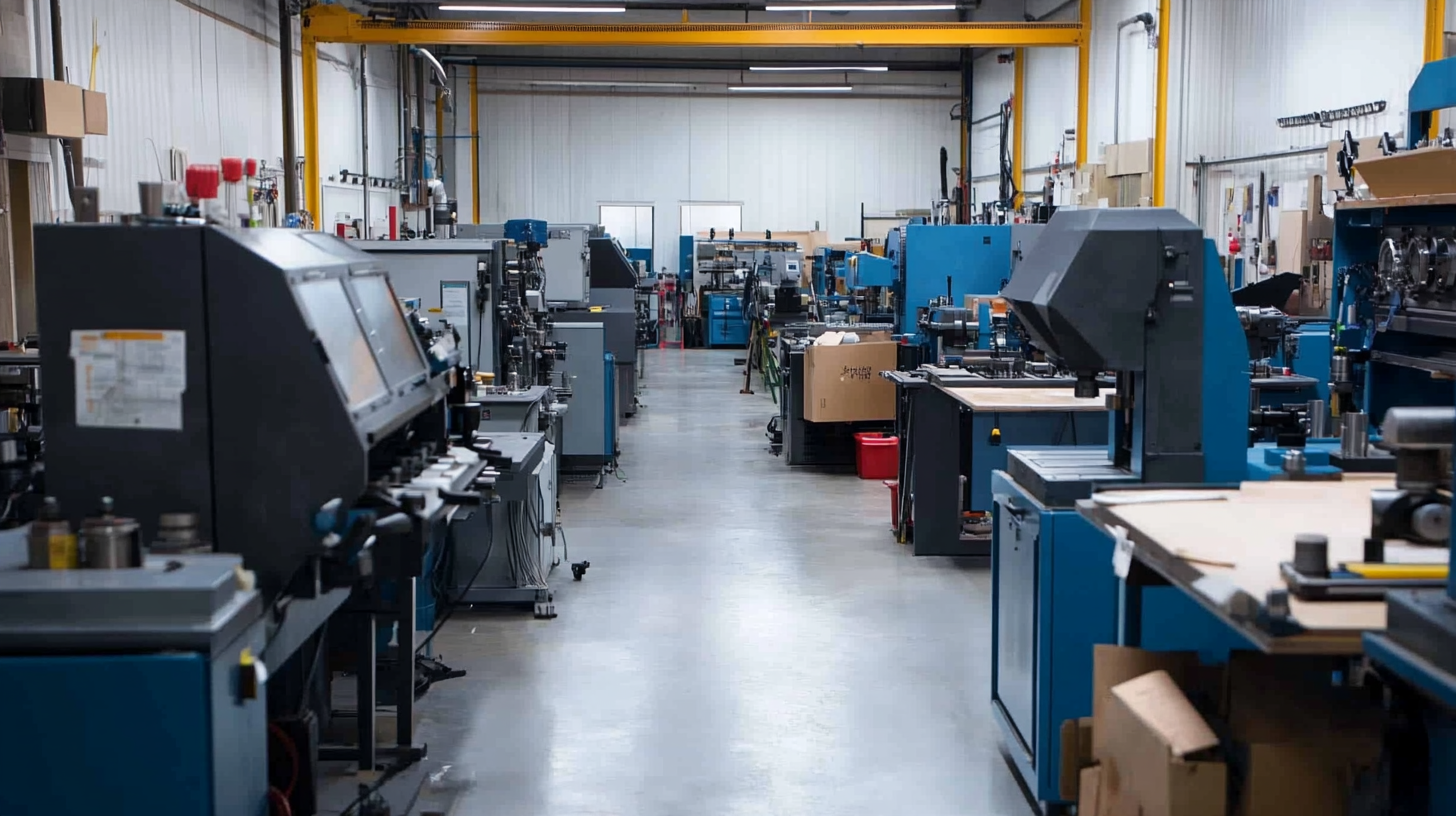
Understanding the Basics: What is a CNC Tool Room Lathe?
A CNC tool room lathe is a sophisticated piece of machinery pivotal in modern manufacturing and precision engineering. Unlike traditional lathes, which require manual operation, CNC (Computer Numerical Control) lathes automate the cutting process through programmed commands. This allows for greater accuracy, repeatability, and efficiency, making them a popular choice in tool rooms where precision is paramount. Understanding the basics of a CNC tool room lathe involves grasping its key components, including the spindle, cutting tools, and the computer control system. The spindle is the heart of the lathe, spinning the workpiece at high speeds while the cutting tools, positioned with precision, remove material to shape the piece. The computer control system interprets design files and translates them into commands that dictate the movements of the lathe, ensuring that complex designs can be produced with minimal human intervention. Another critical aspect to consider is the programming involved in operating a CNC lathe. Users need to be familiar with coding languages such as G-code, which directs the machine on how to perform specific tasks. This programming capability not only enhances the functionality of tool room lathes but also expands the range of projects that can be accomplished, from intricate parts for aerospace applications to custom components for various industries.
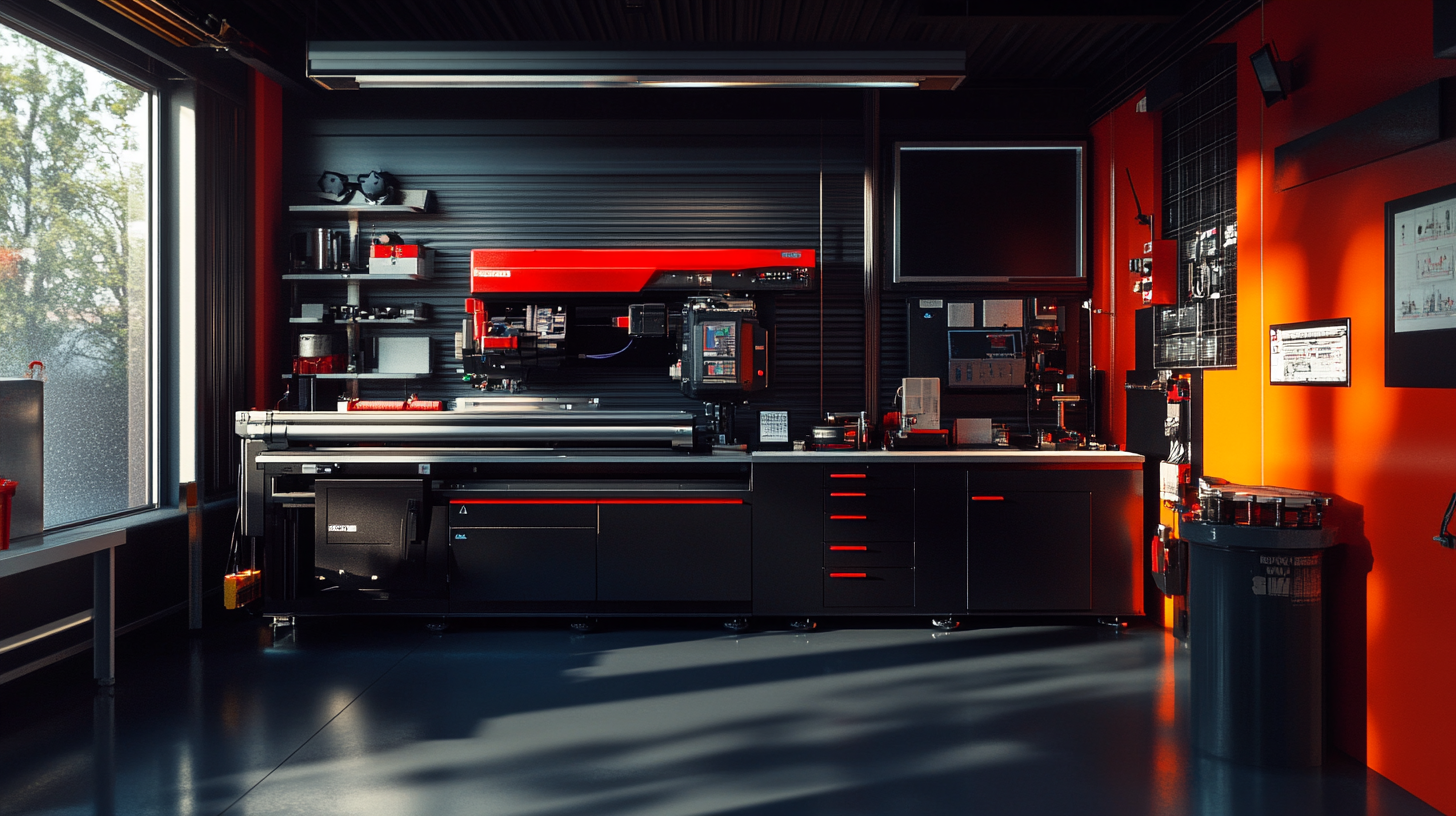
Key Features to Evaluate When Choosing a CNC Lathe
When selecting your next CNC tool room lathe, it's essential to focus on several key features to ensure optimal performance and suitability for your specific applications. First and foremost, consider the lathe's precision and accuracy. CNC lathes are often employed for tasks requiring intricate designs and tight tolerances, so a machine that guarantees high precision in its operations can significantly impact the quality of your finished products.
Another crucial aspect is the control system. A user-friendly interface can streamline operations and enhance productivity. Look for a lathe that offers advanced programming capabilities, allowing for complex machining processes while still being accessible to operators of varying skill levels. Additionally, contemplate the machine's versatility; a lathe that can handle multiple materials and offers dynamic tooling options will provide greater value and adaptability to your workshop.
Lastly, evaluate the support and durability of the lathe. Investing in equipment known for its reliability and backed by strong manufacturer support can reduce downtime and maintenance costs. Consider user reviews and testimonials, as these can provide insights into the machine’s long-term performance and serviceability. By carefully assessing these features, you can make an informed decision that meets your machining demands and enhances your operational capabilities.
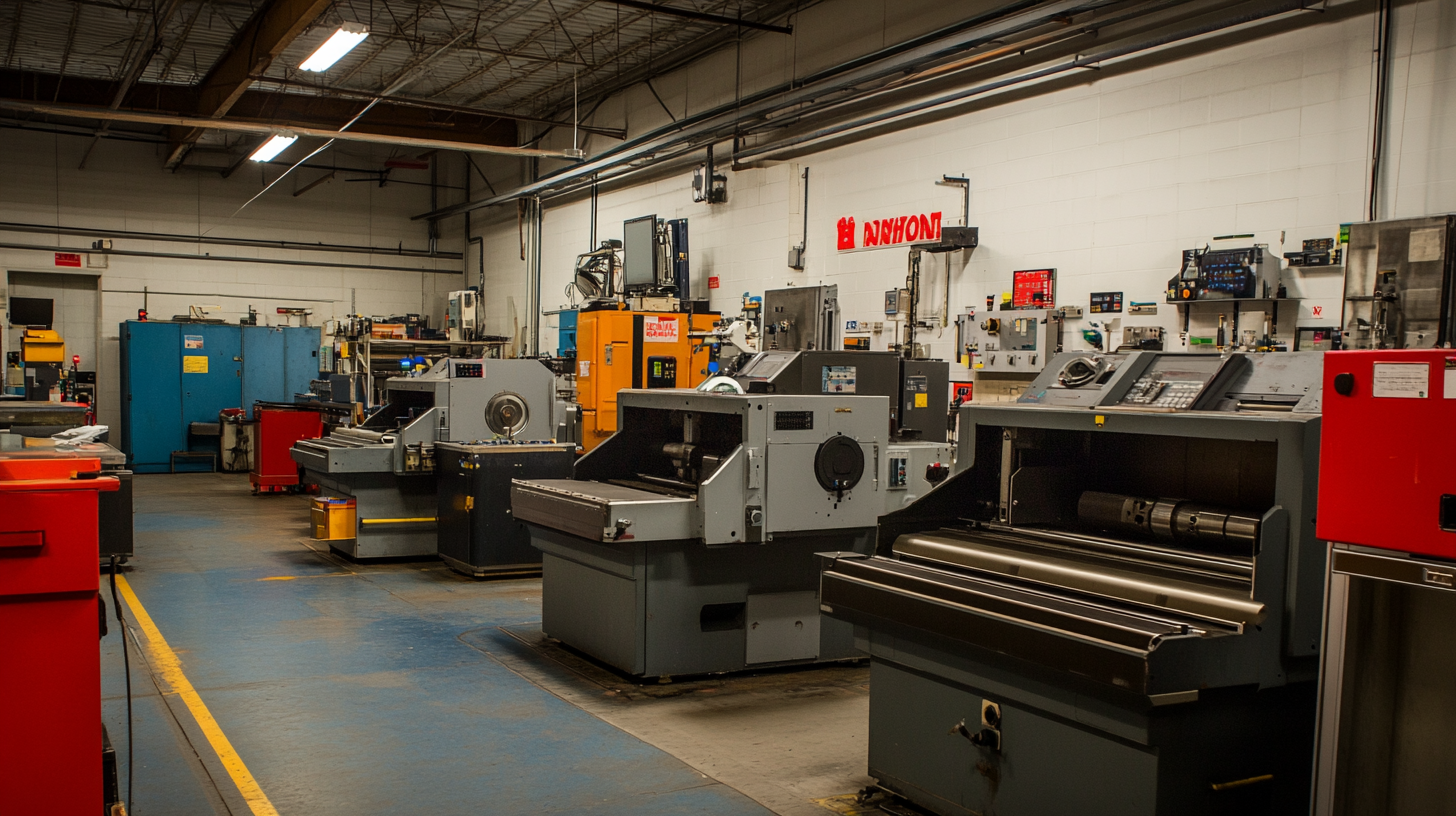
Comparing Different CNC Lathe Models: Pros and Cons
When choosing your next CNC tool room lathe, understanding the various models available on the market is crucial. Each CNC lathe comes with its pros and cons, which directly affect productivity and the quality of outputs. For example, traditional CNC lathes often provide high precision and reliability, making them ideal for standard machining tasks. Their drawback, however, lies in the longer setup times and the need for skilled operators to program and manage them effectively.
In contrast, newer models like multi-tasking CNC lathes often come equipped with advanced features such as live tooling and automatic tool changers. These enhancements allow for more complex machining operations in a single setup, often leading to significant time savings and reduced labor costs. However, the initial investment can be considerably higher, and there can be a steeper learning curve for operators unfamiliar with the latest technology.
Additionally, considering the size and capacity of the CNC lathe is essential. Smaller, more compact lathes are great for limited workspaces and can efficiently handle smaller parts, yet they may struggle with larger components. On the other hand, larger lathes can machine bigger pieces but often require more floor space and higher operational costs. By carefully weighing the pros and cons of different CNC lathe models, you can make an informed decision that aligns with your machining needs and business goals.
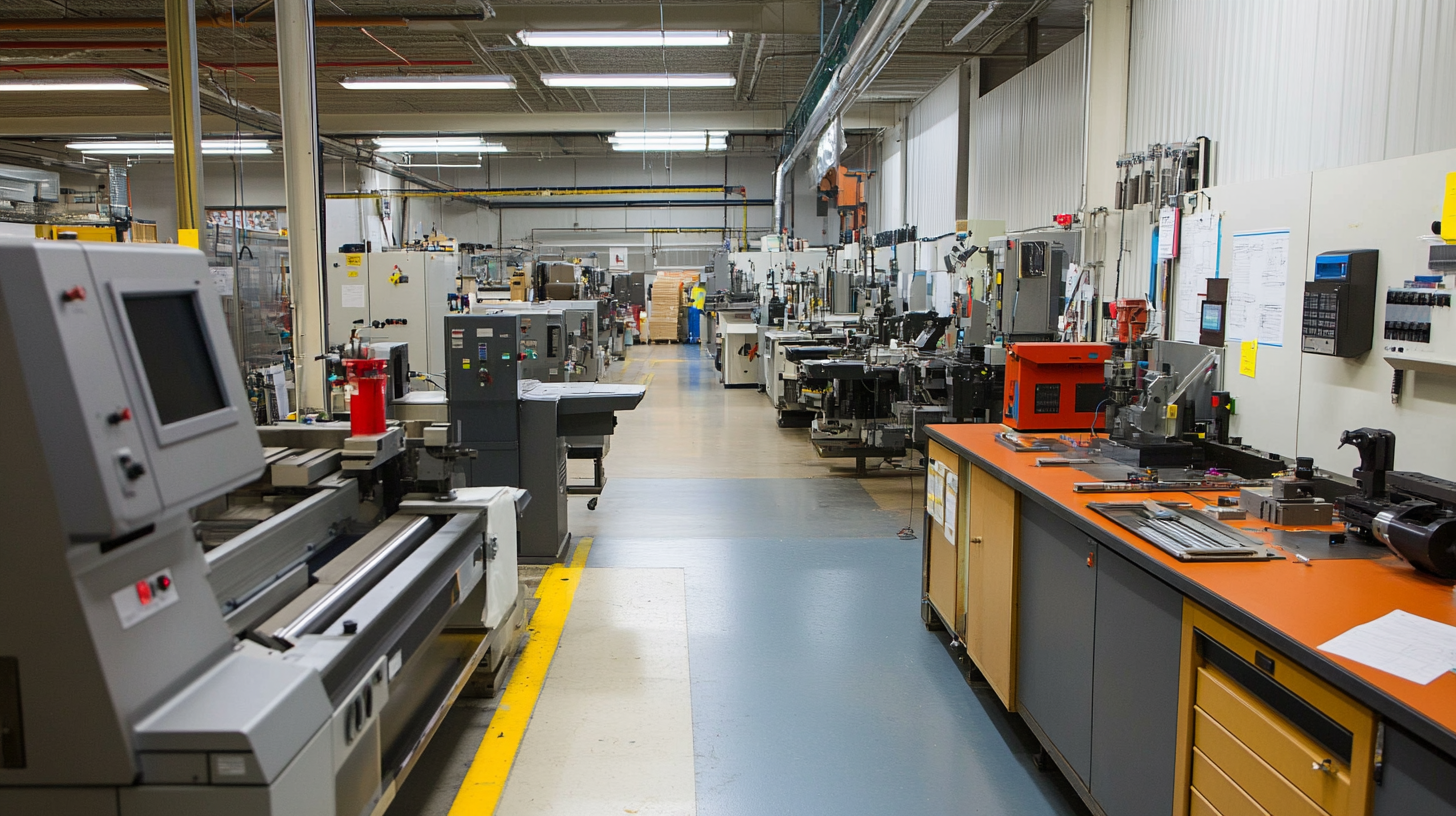
Cost Considerations: Budgeting for Your CNC Lathe Purchase
When considering the purchase of a CNC lathe tool room, cost is undoubtedly a critical factor. Budgeting for a CNC lathe involves more than just the initial purchase price; potential buyers must account for ongoing expenses such as maintenance, repairs, tooling, and software upgrades. As the CNC machine market continues to grow, with projections estimating a significant expansion in the coming years, it’s imperative for operators to conduct thorough financial planning. This enables them to optimize their operations and avoid any unforeseen costs that could impact their bottom line.
Before making a purchase, assessing the features and capabilities of various CNC lathes is equally crucial. Features such as automation and data integration can enhance efficiency and productivity while potentially minimizing long-term costs. For instance, modern CNC lathes often come equipped with real-time data solutions to help identify issues before they escalate, such as tool breakages or operational downtimes. This level of foresight can save significant amounts over time, proving that investing in higher-quality equipment may lead to lower overall costs.
Additionally, small CNC machines are gaining popularity, particularly among hobbyists and startups that prioritize budget-friendliness without compromising quality. By carefully evaluating options within their price range and focusing on machines that balance affordability with capabilities, buyers can ensure they make informed decisions that align with their financial goals and operational needs.
Maintenance and Support: Ensuring Longevity of Your CNC Lathe
When investing in a CNC tool room lathe, one critical aspect to consider is the maintenance and support offered by the manufacturer. Regular maintenance is essential for the longevity of any CNC machine. A well-maintained lathe not only ensures precision and efficiency but also minimizes unexpected downtime, which can significantly impact overall productivity. It's important to evaluate the manufacturer's maintenance recommendations and support services, assessing whether they provide comprehensive guides, troubleshooting resources, and access to skilled technicians.
Having a solid support system in place is equally important. Manufacturers that offer training sessions or workshops can help operators become adept at utilizing the CNC lathe effectively. This not only enhances the machine's performance but also extends its lifespan. Additionally, consider the availability of spare parts and the manufacturer's commitment to customer service. Quick access to replacement components can make a significant difference when repairs are needed, preventing prolonged disruptions to your workflow.
Ultimately, prioritizing maintenance and support will help ensure that your CNC lathe operates smoothly and efficiently for years to come, making your investment more worthwhile in the long run.