Setting the Benchmark: Understanding CNC Tool Manufacturing Standards and Their Global Impact
In today's fast-paced manufacturing landscape, the importance of precise and high-quality CNC tools cannot be overstated. As industries across the globe increasingly rely on CNC (Computer Numerical Control) technology to enhance productivity and ensure accuracy, understanding the manufacturing standards that govern these tools becomes critical. Setting the benchmark for CNC tool manufacturing not only influences operational efficiency but also defines the competitive edge of businesses in various sectors. This blog will explore the intricate manufacturing standards associated with CNC tools and their global implications, shedding light on how these standards affect product quality, safety, and performance.
The global impact of CNC tool manufacturing standards extends far beyond mere compliance; it shapes the industry landscape, drives innovation, and influences market dynamics. By adhering to established benchmarks, manufacturers can ensure their CNC tools meet the highest quality and reliability criteria, fostering trust among customers and stakeholders. As we delve deeper into the intricacies of these standards, we will reveal how they function as a vital framework that enhances collaboration between manufacturers and users, ultimately propelling advancements in technology and manufacturing processes. Join us as we set the stage for a comprehensive discussion on the pivotal role of CNC tool manufacturing standards in shaping the future of the industry.
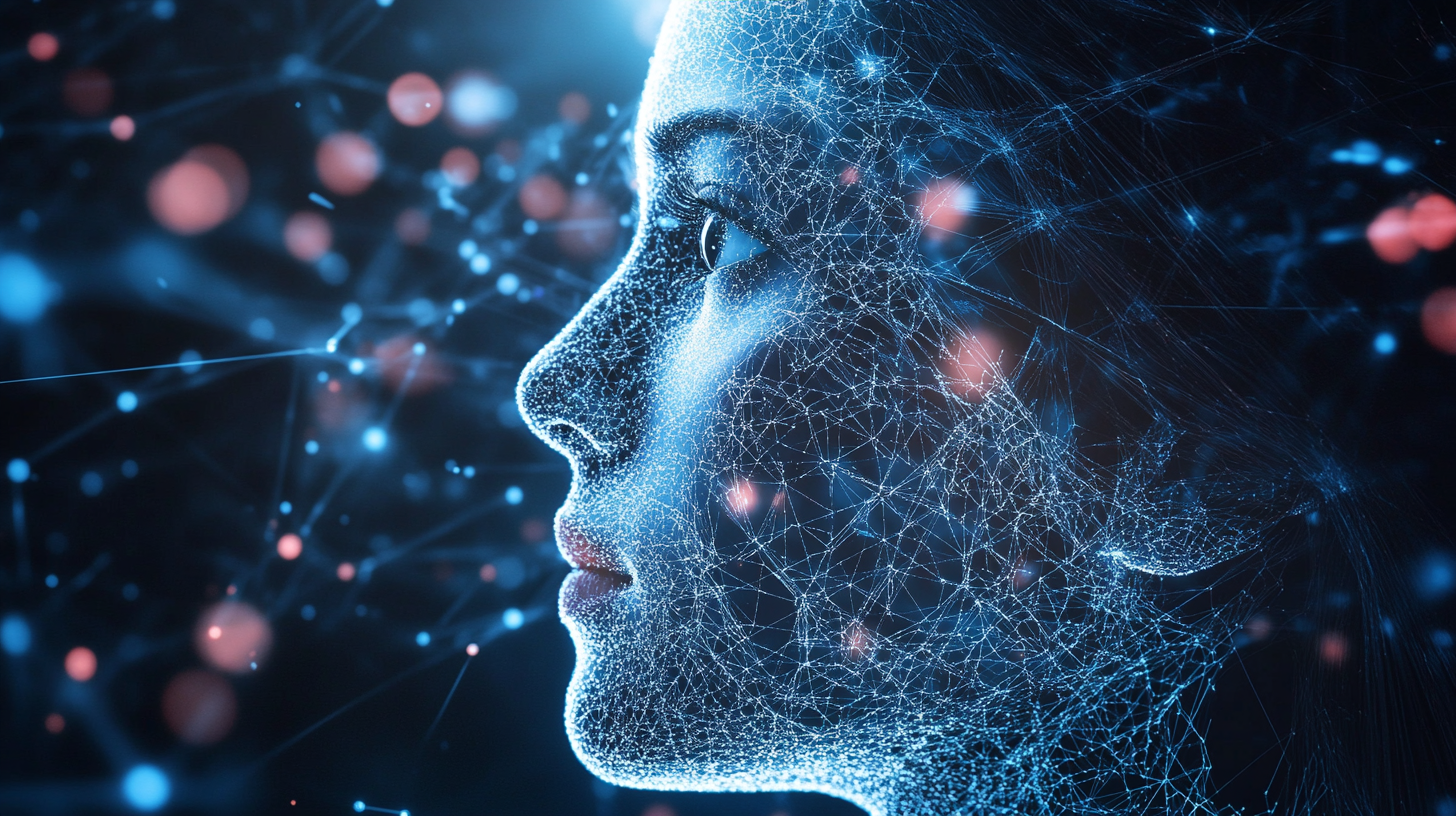
The Evolution of CNC Tool Manufacturing Standards Through the Years
The evolution of CNC (Computer Numerical Control) tool manufacturing standards has been pivotal in shaping the industry, promoting efficiency, precision, and safety. In the early years, the standards were rudimentary and focused primarily on ensuring that machines could operate without excessive wear and tear. According to a report by the International Organization for Standardization (ISO), the first CNC standards were established in the 1970s, setting the groundwork for precision engineering that would come in later decades. Throughout the 1980s and 1990s, the advent of more sophisticated materials and technologies saw a significant boost in the precision and capabilities of CNC tools. The introduction of standardized testing procedures helped manufacturers validate the performance of their products. By 1998, the ISO 9001 quality management system was adopted widely, emphasizing continuous improvement and customer satisfaction. This shift toward standardized practices not only improved product reliability but also facilitated international trade, allowing manufacturers to export tools with confidence. In recent years, the emphasis has leaned towards the integration of digital technologies and automation. According to a report by MarketsandMarkets, the global CNC machine market is projected to reach USD 117.31 billion by 2026, underscoring the industry's move towards smarter, more connected tools. The introduction of Industry 4.0 has brought new standards focused on interoperability and data exchange between machines, which further enhances productivity and resource management. As the standards continue to evolve, they will play a crucial role in addressing challenges such as sustainability and the need for rapid innovation in CNC tool manufacturing.
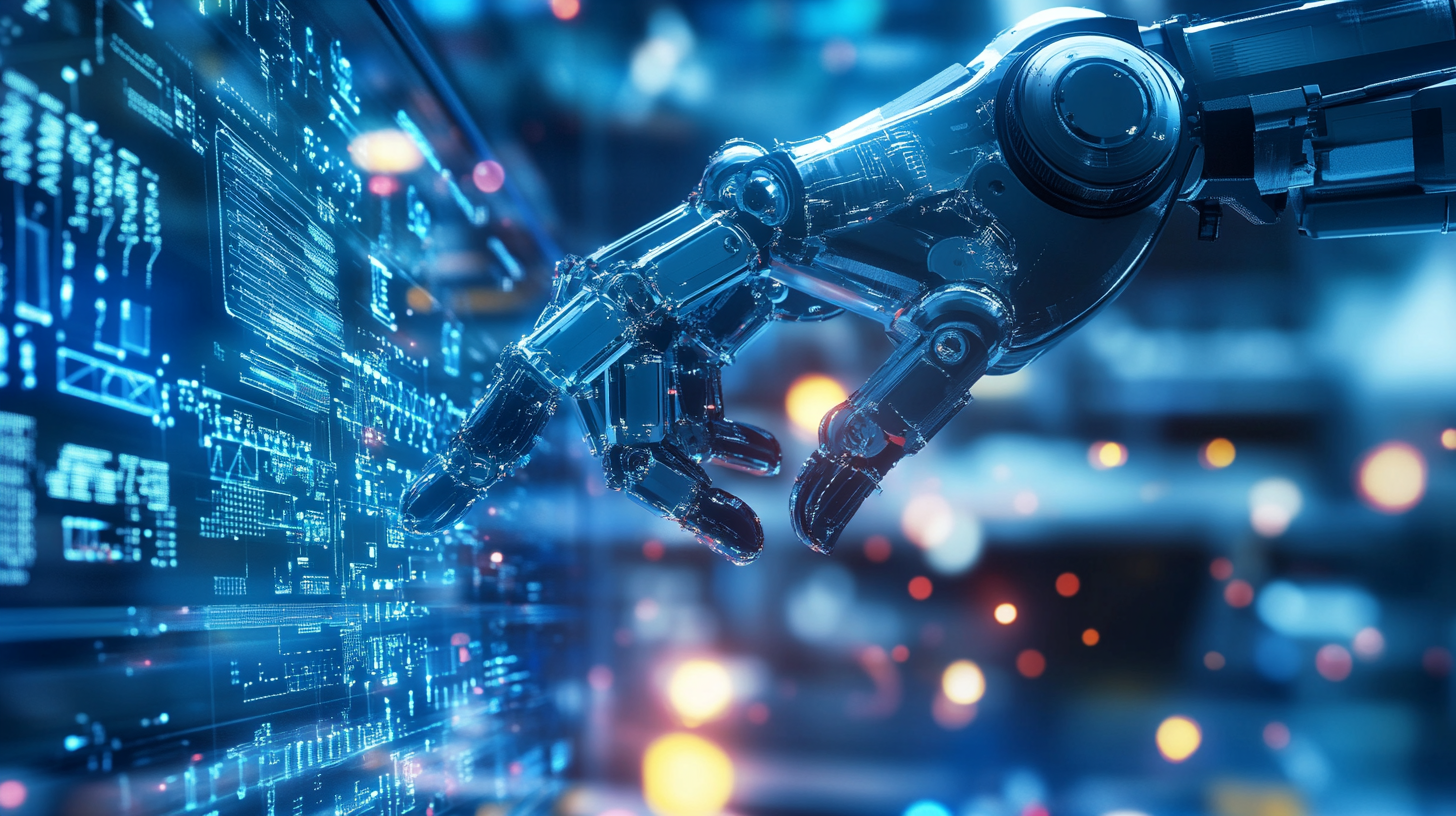
Key International Organizations Influencing CNC Tool Standards
The landscape of CNC tool manufacturing is significantly influenced by key international organizations that establish and uphold standards across the globe. Among the most prominent are the International Organization for Standardization (ISO) and the Association for Manufacturing Technology (AMT). These organizations play a critical role in setting benchmarks that ensure quality, safety, and efficiency in CNC tool production, which is essential given the industry's projected growth. According to a report by MarketsandMarkets, the CNC machine market is expected to grow from $70.23 billion in 2020 to $100.96 billion by 2026, primarily driven by the need for precision engineering and high production rates.
ISO, with its vast repository of standards, covering everything from design specifications to manufacturing processes, provides a foundation that manufacturers can rely on. For instance, ISO 9001:2015 outlines quality management systems that are crucial for maintaining product integrity and customer satisfaction. The ISO standards are not just regulatory measures; they help facilitate international trade by ensuring that products meet universal quality benchmarks, thereby minimizing trade barriers and fostering global competitiveness.
Meanwhile, AMT plays a pivotal role in advocating for technology advancements and innovations within the machining sector. Through their standards, they influence the adoption of cutting-edge technologies in CNC tool manufacturing. Their research shows that companies adhering to these standards report a 25% improvement in operational efficiency and a significant reduction in production costs. This data underscores the importance of aligning with recognized international standards to remain competitive in a rapidly evolving marketplace. As the CNC industry continues to expand, the role of these organizations in shaping standards cannot be overstated.
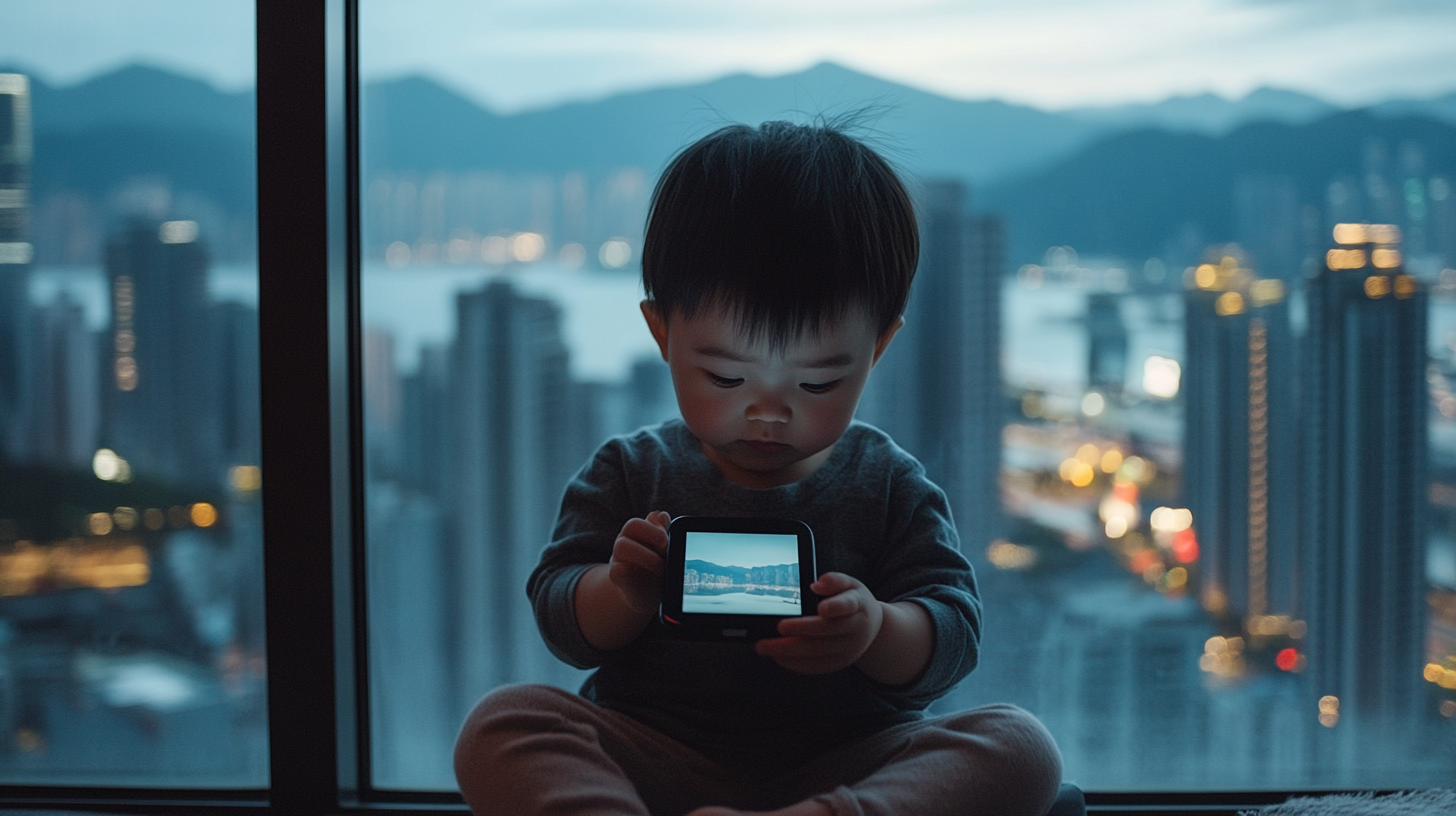
The Importance of Compliance in CNC Tool Production Quality
Ensuring compliance in CNC tool production is paramount for maintaining high-quality standards, especially in the rapidly evolving landscape of manufacturing. As the global market shifts towards Industry 4.0 and smart manufacturing, adherence to established manufacturing standards is crucial. Recent projections indicate that the index for the turning tool market is expected to exceed $4.63 billion in 2023, driven by a compound annual growth rate of 6.3% from 2024 to 2032. This growth underscores the increasing reliance on sophisticated CNC technologies that must adhere to strict compliance measures, ensuring that they meet both customer expectations and regulatory requirements.
Furthermore, the CNC machine tool market is poised for significant expansion, with analyst reports suggesting a strong correlation between the adoption of advanced technologies and market growth. The demand for precision tools in critical industries such as automotive, general machinery, and aerospace is rising, necessitating adherence to compliance protocols. Companies seeking to capture market share must prioritize compliance not only to enhance their reputation but also to ensure the safety and reliability of their products.
As the industry moves further into an era of digital integration and smart applications, understanding and meeting CNC manufacturing standards is not just beneficial—it is essential for survival in a competitive, technology-driven market. The integration of artificial intelligence into CNC machining processes is set to open new avenues and drive further compliance adaptation in tool manufacturing, enhancing both productivity and precision while ensuring safety and quality are maintained at all levels.
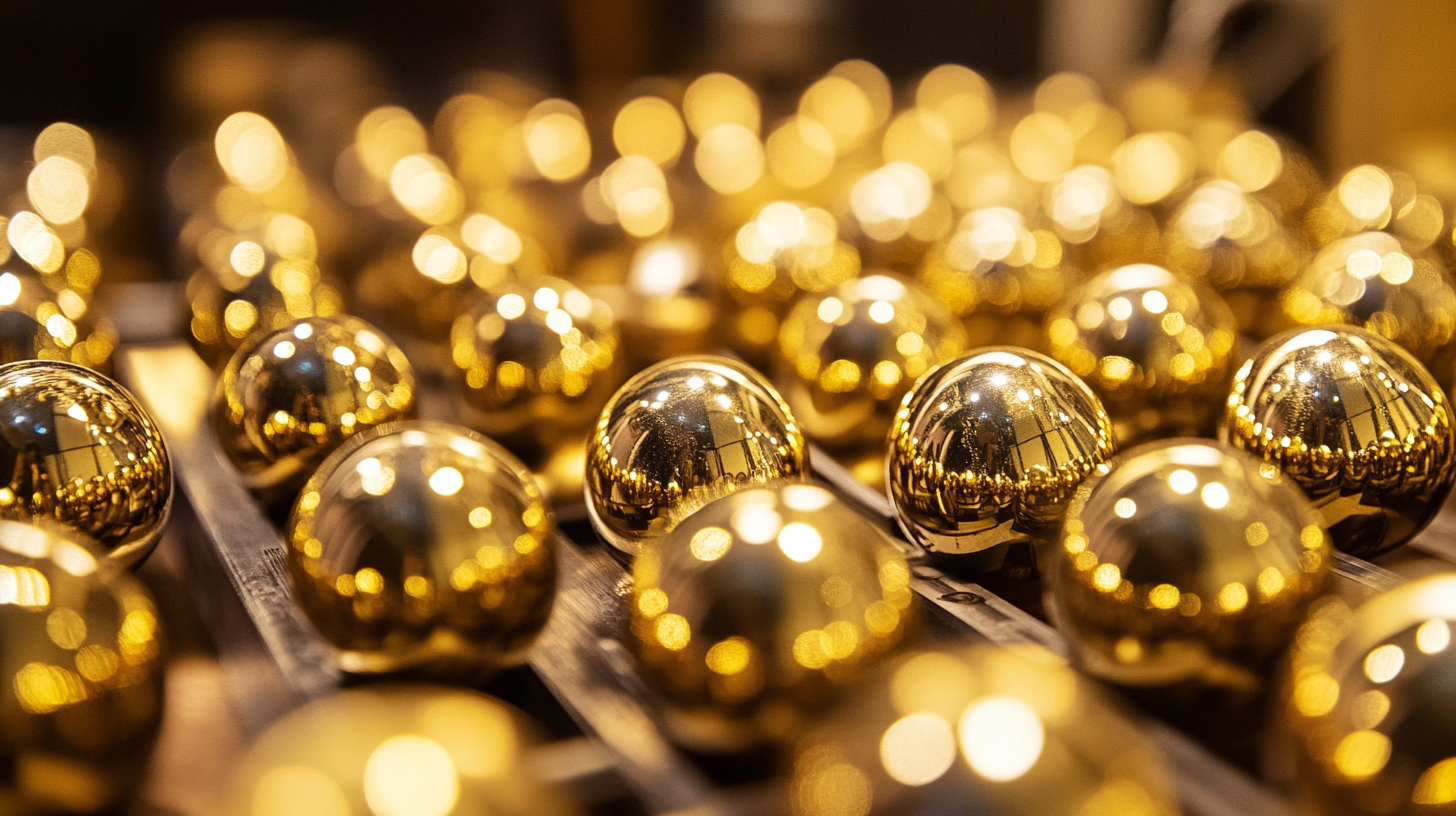
Global Variations in CNC Tool Manufacturing Practices and Standards
You know, when you look at how CNC tools are made around the world, it’s pretty fascinating. There’s this whole mix of cultural vibes, tech advancements, and regulations that shape manufacturing practices. And as we all get more connected globally, it’s super important for manufacturers to grasp these differences—especially if they want to keep up with worldwide demands while staying efficient and eco-friendly in their production.
Take Japan and Germany, for instance. Precision engineering isn’t just a buzzword there; it’s part of their manufacturing DNA! They have these really strict standards that emphasize quality and innovation, which means they're all about using advanced materials and the latest tech to make their tools last longer and perform better. On the flip side, you’ve got emerging markets that tend to be a bit more laid-back, focusing on cutting costs and cranking out products quickly. This whole variation really drives home the point that businesses must grasp these differing standards, especially when they’re thinking about expanding into new areas.
And let’s not forget the recent buzz about sustainability and being environmentally responsible—it’s really changing the game in manufacturing everywhere. More and more, we’re hearing about goals like ‘zero waste’ and practices from places like Shaoxing in China, where they've got some cool ideas in their yellow wine industry. These aren’t just good for the planet; they also resonate with consumers who are getting increasingly picky about how their products are sourced. Global organizations, like those awarded by the World Health Organization for tackling industrial trans fats, are raising the bar. So, CNC tool manufacturers really have to think on their feet, adapting and innovating to meet both local standards and the higher expectations on a global scale.
The Future of CNC Tool Manufacturing: Trends and Innovations to Watch
You know, the world of CNC tool manufacturing is changing super fast! It’s really exciting to see all these new trends and innovations coming up that are set to reshape the industry. One big thing we’re seeing is the rise of Industry 4.0 and the Internet of Things (IoT) in the CNC space. Basically, by bringing digital tech and computerization into the manufacturing processes, companies are really ramping up their precision and efficiency. This means they can produce more while wasting less—pretty awesome, right? Plus, with these smart CNC technologies, manufacturers can tap into real-time data to fine-tune their operations and really nail those quality standards.
But that’s not all—don’t forget about artificial intelligence (AI). It’s kind of a game-changer! AI helps machines learn from data patterns, which is great for things like predictive maintenance and next-level automation. It’s not just about making things work better; it’s also opening the door to some cool new applications, like personalized tooling solutions that fit specific production needs. As AI keeps getting better, it’s going to be super important for businesses looking to cut costs and speed up their lead times—definitely a must if they want to stay competitive in this global market.
And let's chat about sustainability for a second. It’s really becoming a big deal in CNC tool manufacturing. A lot of manufacturers are on the hunt for green technologies and energy-efficient solutions, which is a huge step towards cutting down our environmental footprint. By going for sustainable practices, companies aren’t just checking off boxes for regulations; they’re also appealing to those consumers who care about eco-friendliness. With all these trends coming together, the future of CNC tool manufacturing looks really bright—think smarter, greener, and way more efficient production methods!