Maximizing Cnc Lathes Longevity with Cost Effective Maintenance Strategies
In the world of precision manufacturing, CNC lathes play a pivotal role in enhancing productivity and ensuring the accuracy of machined components. According to a report by the National Association of Manufacturers, nearly 65% of manufacturers consider CNC machining indispensable for modern production processes. However, the longevity of CNC lathes is often compromised by inadequate maintenance practices. Research indicates that predictive maintenance can reduce machine downtime by over 30%, translating to significant cost savings and improved operational efficiency.
Implementing cost-effective maintenance strategies is crucial for maximizing the lifespan of CNC lathes and optimizing their performance. A study by the Machine Tool Engineering Journal found that companies that adopt proactive maintenance frameworks see a 25% decrease in repair costs and an extension of machine life by an average of five years. By understanding the importance of regular maintenance and proactive strategies, manufacturers can better position themselves in the competitive landscape, ensuring their CNC lathes continue to deliver exceptional results over time.
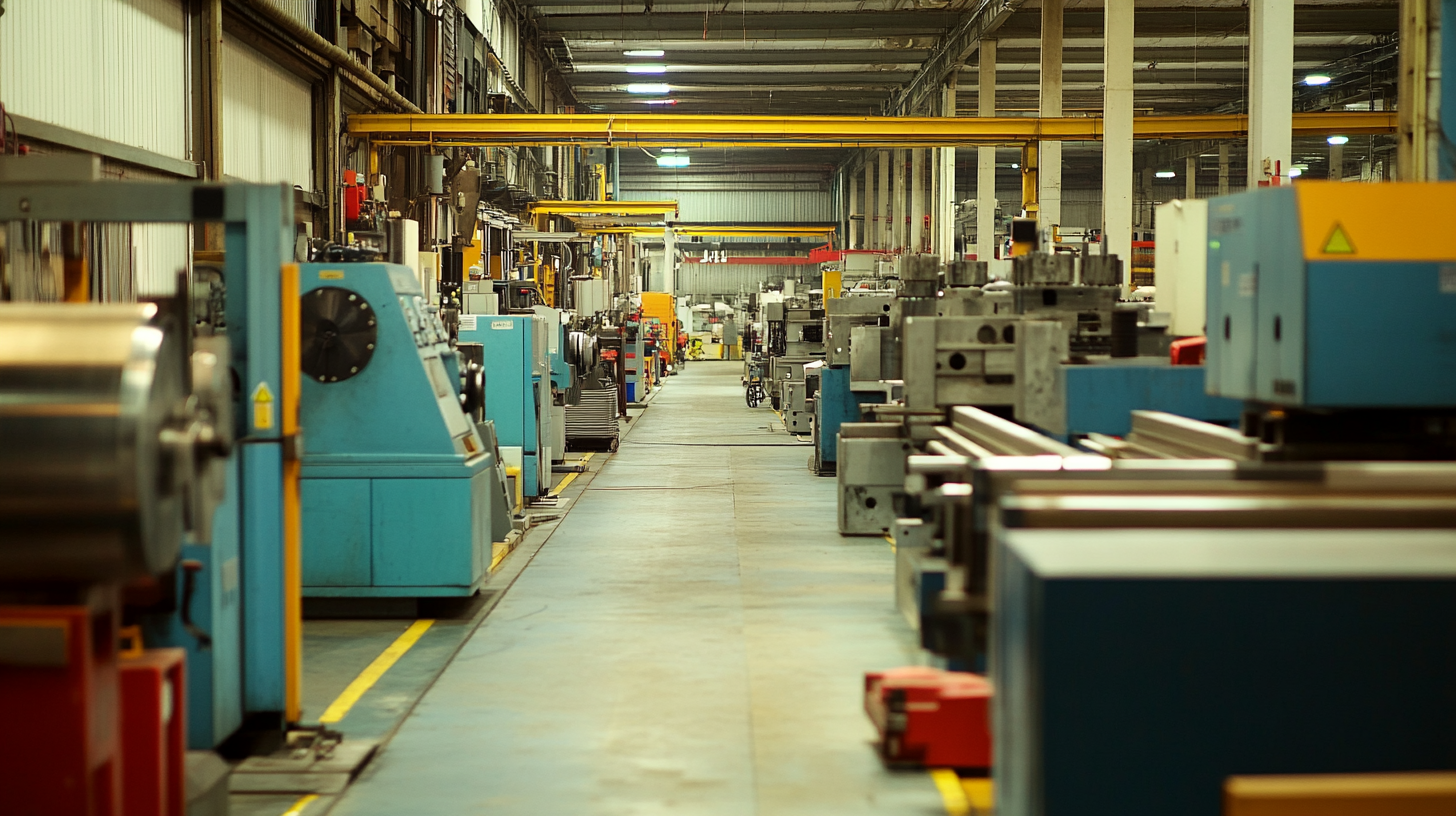
Identifying Key Maintenance Practices for CNC Lathes to Extend Equipment Lifespan
CNC lathes are essential for precision machining in various industries. To extend their lifespan and maximize productivity, it’s crucial to implement effective maintenance strategies that focus on key practices. One of the primary maintenance practices is establishing a regular inspection schedule. This allows for early detection of wear and tear, ensuring that potential issues are identified before they escalate into costly repairs or downtime. Another vital aspect is to utilize advanced monitoring technologies, such as ultrasonic sensors. These sensors correlate sound with machining quality, providing real-time data that can help operators adjust settings and prevent defects. Integrating such technologies not only enhances the quality of output but also leads to more informed decision-making about maintenance needs, ultimately prolonging the lathe's operational life. Moreover, proper lubrication and cleaning protocols are essential for maintaining CNC lathes. Ensuring that the moving parts are well-lubricated minimizes friction and wear, while regular cleaning prevents the buildup of debris that can impede performance. Implementing these key maintenance practices effectively contributes to the longevity of CNC lathes, enhancing both their efficiency and reliability in production processes.
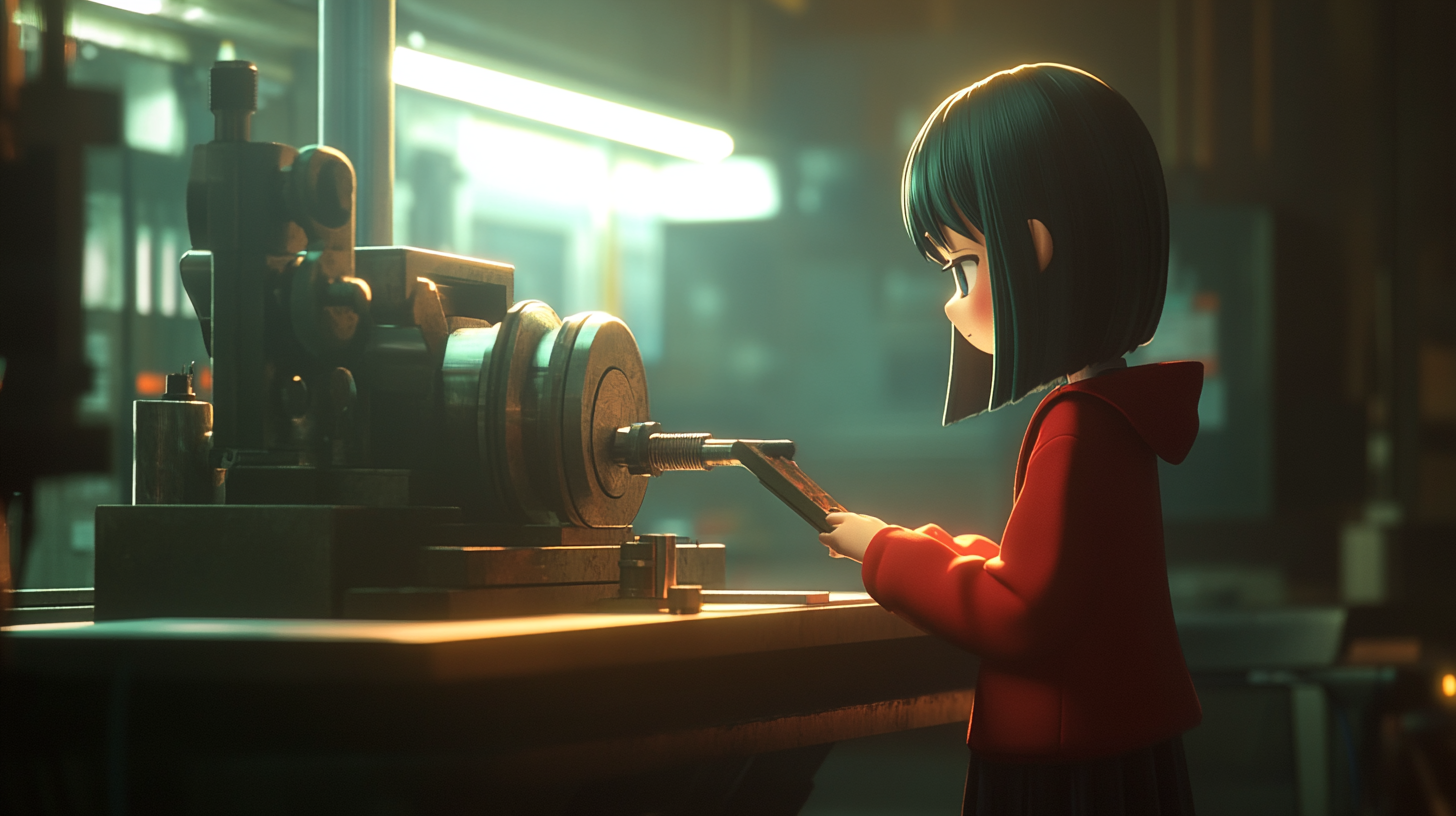
Analyzing the Impact of Regular Calibration on Precision and Longevity of CNC Lathes
Regular calibration plays a pivotal role in maintaining the precision and longevity of CNC lathes, as these machines are keystones in modern manufacturing. Over time, even the most meticulously maintained CNC lathes can drift from their optimal settings due to factors such as wear and tear, thermal expansion, and mechanical shifts. By performing regular calibration checks, operators can ensure that the machinery remains aligned with its design specifications, minimizing errors in production and maintaining high standards of quality.
The impact of regular calibration extends beyond mere accuracy. When CNC lathes are calibrated on a consistent basis, they experience less wear, ultimately leading to prolonged machine lifespan. Calibration helps in identifying potential issues before they escalate into costly repairs or downtime. For instance, small deviations that may go unnoticed can lead to increased tool wear or damage to the workpiece, resulting in scrap and inefficiencies. Incorporating a routine calibration schedule can thus save companies both time and resources while enhancing overall production reliability.
Moreover, well-calibrated CNC lathes operate more efficiently, consuming less energy and reducing cycle times. This not only contributes to a more sustainable manufacturing process but also enhances the financial bottom line. As industries evolve and demands for precision continue to rise, investing in regular calibration is no longer optional—it’s a fundamental strategy for businesses aiming to maximize their CNC lathes' longevity while ensuring flawless production output.
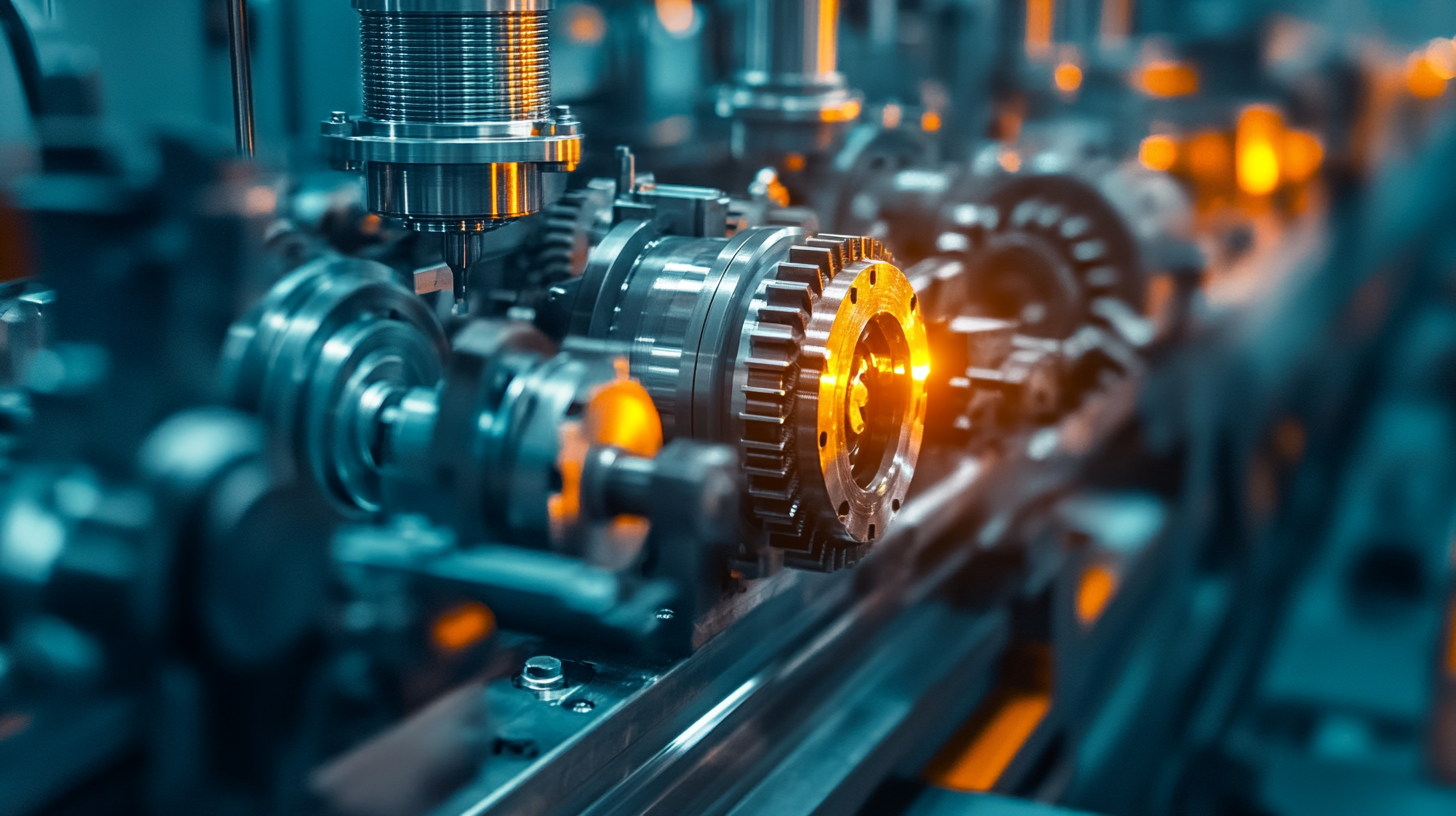
Utilizing Predictive Maintenance Technologies to Reduce Downtime and Repair Costs
In the modern manufacturing landscape, the implementation of predictive maintenance technologies is increasingly seen as a key strategy to enhance operational efficiency and extend the lifespan of machinery, especially CNC lathes. By leveraging real-time data analysis and machine learning algorithms, manufacturers can anticipate maintenance needs before they escalate into costly failures. Such proactive approaches are crucial as industries globally emphasize reducing downtime and repair costs, aligning with the broader trends in smart manufacturing.
The projected growth of the global magnetic pump market, anticipated to reach $960 million by 2033 from $700 million in 2024, underscores the rising emphasis on reliability and efficiency in manufacturing processes. This growth, driven by a compound annual growth rate (CAGR) of approximately 3.6%, reflects an increasing demand for advanced technologies that can optimize performance while minimizing waste.
Similarly, the mining equipment market is on track for substantial growth, with an increase to over $83.7 billion in market size by 2024, projected to grow at a CAGR exceeding 5.2% through 2034. This growth is propelled by a surging demand for minerals and metals, necessitating smarter, data-driven operational strategies.
As the industrial sector evolves, embracing the industrial metaverse and integrating IoT, artificial intelligence, and augmented realities, the focus on predictive maintenance is set to redefine manufacturing practices. Companies are not only seeking to enhance productivity but also aiming to create sustainable, resilient operations that can withstand the challenges of an ever-changing economic landscape.
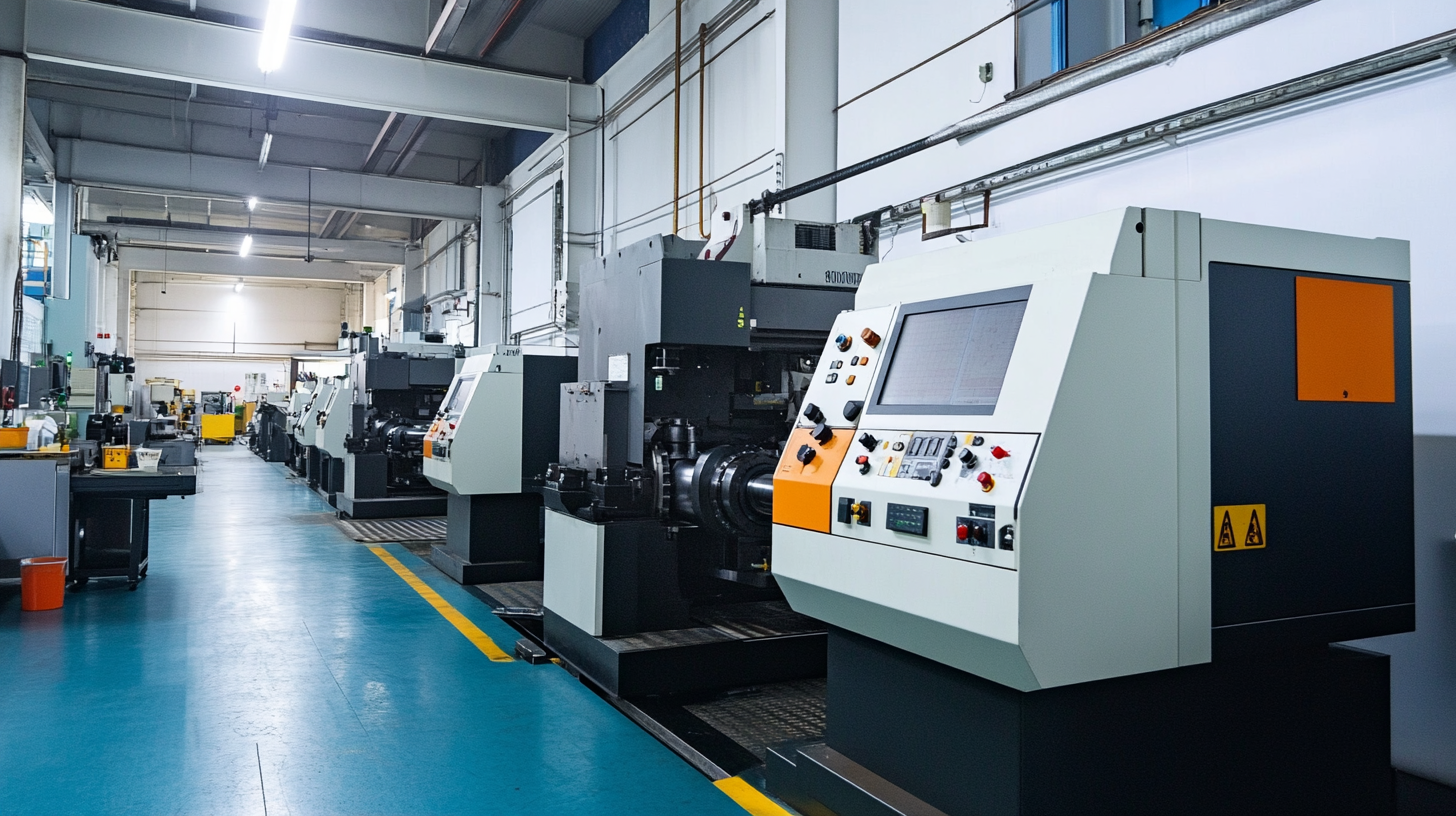
Cost-Benefit Analysis of Routine Maintenance Schedules for CNC Lathe Operations
When it comes to CNC lathe operations, understanding the cost-benefit analysis of routine maintenance schedules is crucial for maximizing equipment longevity and minimizing downtime. A well-structured maintenance plan not only enhances the performance of CNC lathes but also significantly reduces long-term operational costs. Regular inspections and timely servicing can prevent minor issues from escalating into major repairs, which can be a financial burden for manufacturing businesses. Moreover, maintaining optimal operational conditions through routine checks increases the efficiency and accuracy of the machining process.
The demand for CNC lathes is expected to grow, with the global machine tool market projected to reach approximately $230.4 billion by 2033. As industries like automotive and precision engineering expand, the role of CNC lathes becomes even more pronounced. Employers must recognize that investing in regular maintenance schedules not only yields immediate operational benefits but also contributes to sustained financial growth, reinforcing the need for strategic resource allocation in maintenance practices. By focusing on cost-effective maintenance strategies, businesses can enhance the longevity of their CNC equipment and ensure their competitive edge in the evolving market landscape.
Implementing Operator Training Programs to Enhance CNC Lathe Maintenance Efficiency
Implementing operator training programs is essential for enhancing the maintenance efficiency of CNC lathes. Operators are the first line of defense when it comes to ensuring the longevity of these intricate machines. A well-structured training program equips them with the knowledge and skills to perform routine maintenance checks, identify potential issues early, and execute corrective measures before minor problems escalate into major repairs. By emphasizing hands-on training and real-world scenarios, operators can better understand the specific requirements of the CNC lathes they work with, leading to a more proactive maintenance approach.
Furthermore, fostering a culture of continuous improvement and learning within the organization can significantly boost maintenance efficiency. Regular workshops and advanced training sessions keep operators updated on new technologies, tools, and techniques related to CNC lathe maintenance. This not only enhances their individual skill sets but also builds a collaborative environment where knowledge-sharing becomes the norm. As a result, operators are empowered to take ownership of their roles, leading to better care of the equipment and a noticeable increase in machine uptime.
Sustained operator training not only contributes to the immediate performance of CNC lathes but also creates a long-term impact on overall productivity. By investing in the development of the workforce, companies can ensure that their teams are prepared to tackle maintenance challenges effectively. This strategic approach ultimately translates into lower operational costs and increased profitability, reinforcing the importance of prioritizing operator education in the maintenance strategy of CNC lathes.