7 Reasons Why CNC Machining Centers Are Essential for Modern Manufacturing Success
In today’s competitive manufacturing landscape, the integration of advanced technologies is no longer optional but essential for achieving operational excellence. CNC Machining Centers have emerged as pivotal components in modern manufacturing processes, offering unmatched precision, efficiency, and flexibility. According to a recent report by MarketsandMarkets, the CNC machining market is projected to reach USD 117.84 billion by 2026, growing at a CAGR of 6.0% from 2021. This growth highlights the critical role that CNC Machining Centers play in enhancing productivity and meeting the diverse needs of industries ranging from aerospace to automotive.
As manufacturers strive to keep pace with rapidly evolving consumer demands and the complexities of global supply chains, investing in CNC Machining Centers has become a strategic imperative. These advanced machines not only streamline production but also reduce reliance on manual labor, significantly minimizing the risk of human error. With 69% of manufacturers reportedly facing ongoing challenges to improve operational efficiency (as noted in a 2023 survey by Deloitte), the functionality and reliability of CNC Machining Centers are paramount. The following sections will delve into the seven key reasons why these machines are essential for achieving manufacturing success in today's dynamic market.
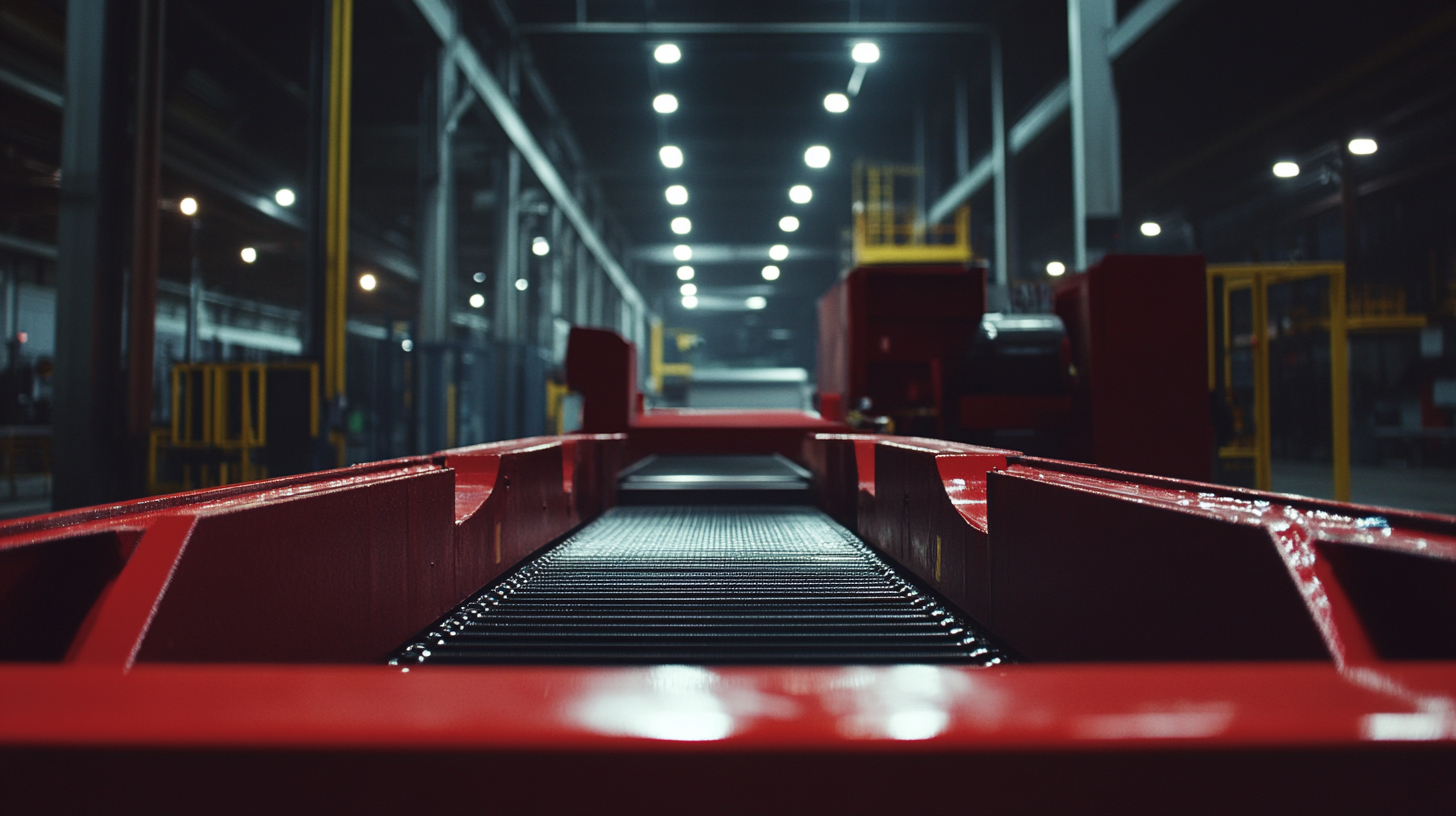
The Precision Advantage: How CNC Machining Centers Ensure Accuracy in Production
CNC machining centers have revolutionized the manufacturing landscape, emphasizing the importance of precision in production processes. The capability of these machines to execute complex designs with accuracy ensures that every component fits seamlessly in its intended application. With the global CNC machine market projected to grow significantly, the demand for meticulously crafted parts across various industries such as aerospace and medical is only expected to rise. At the heart of this evolution is the relentless pursuit of precision. Manufacturers are increasingly recognizing that the accuracy delivered by CNC machining centers enhances not only product quality but also operational efficiency. The integration of advanced technologies, such as probing and inspection within manufacturing software, further elevates this precision by minimizing errors during production and reducing setup times. The result is a streamlined workflow that allows manufacturers to meet stringent quality standards while also adapting swiftly to market demands. As industries continue to seek competitive advantages, the role of CNC machining centers becomes increasingly vital. Their ability to provide custom solutions tailored to specific specifications makes them essential for any organization aspiring to achieve manufacturing excellence. This shift towards precision-focused production methods underscores a broader trend within the machine tools market, where high-quality output is synonymous with operational success.
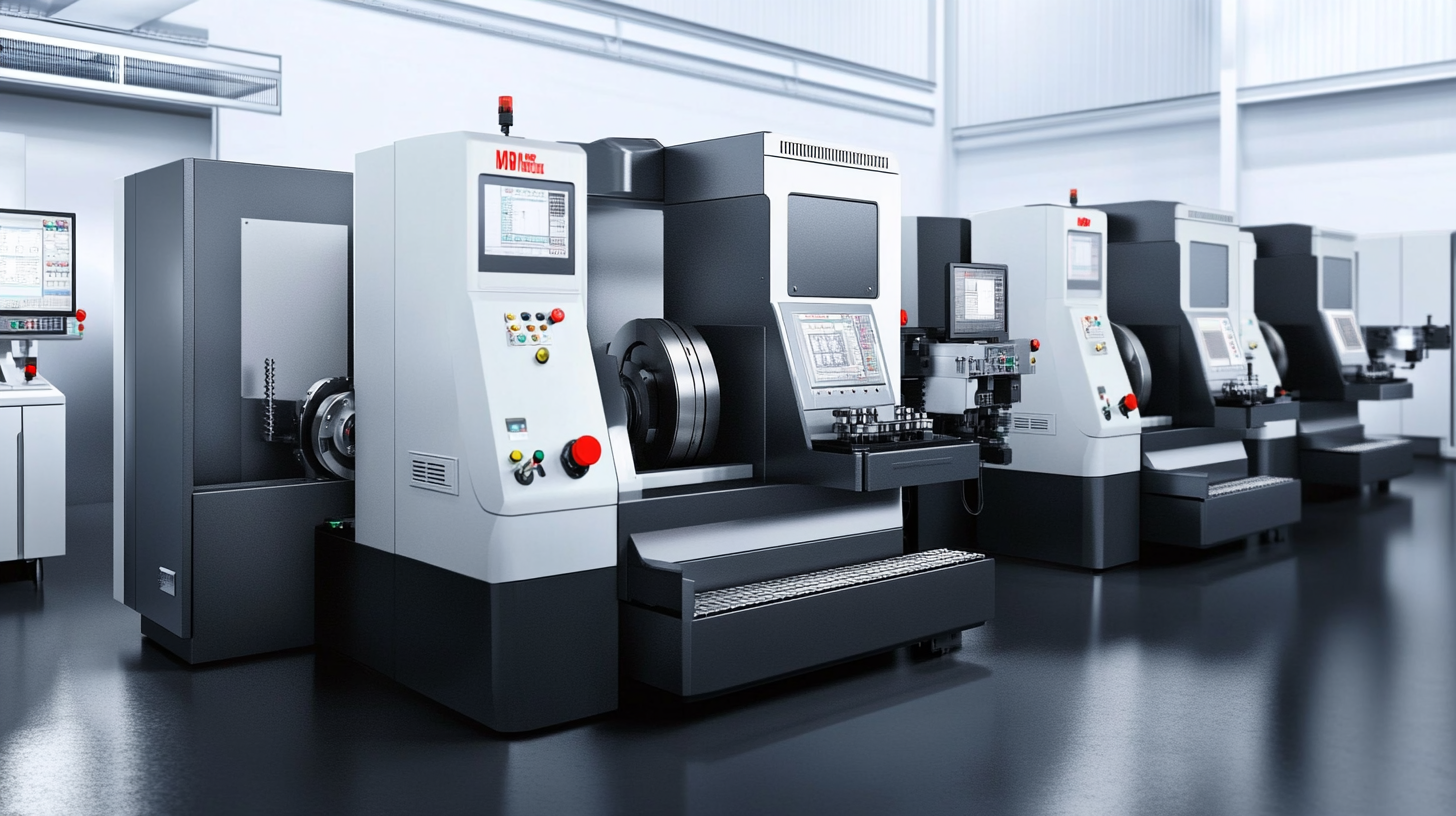
Efficiency Unleashed: Streamlining Operations with CNC Technologies
The efficiency of modern manufacturing is increasingly tied to the adoption of CNC (Computer Numerical Control) technologies. As the global CNC machine market is projected to expand from $101.22 billion in 2025 to $195.59 billion by 2032, representing a compound annual growth rate (CAGR) of 9.9%, it is evident that industries are recognizing the value of automation in enhancing production capabilities. This growth reflects a broader trend toward precision and efficiency, particularly in sectors like metal and material fabrication, where the CNC cutting machines market is anticipated to reach USD 11,671.4 billion by 2032.
Integrating cloud computing technologies into CNC operations further streamlines workflows, enabling real-time optimization, data analysis, and remote monitoring. This level of connectivity allows manufacturers to enhance productivity while reducing downtime and minimizing waste, crucial factors in today's competitive landscape. As companies seek to remain agile and responsive to market demands, the utilization of CNC machining centers becomes not just beneficial but essential for ensuring sustained manufacturing success.
In this context, innovative solutions are emerging, with companies poised to revolutionize CNC technology at upcoming industry events. Advancements are not just limited to traditional machining but extend to the integration of sophisticated technologies that cater to the evolving needs of the manufacturing sector. Embracing these innovations is vital for organizations aiming to thrive in an era marked by rapid technological advancements and shifting consumer expectations.
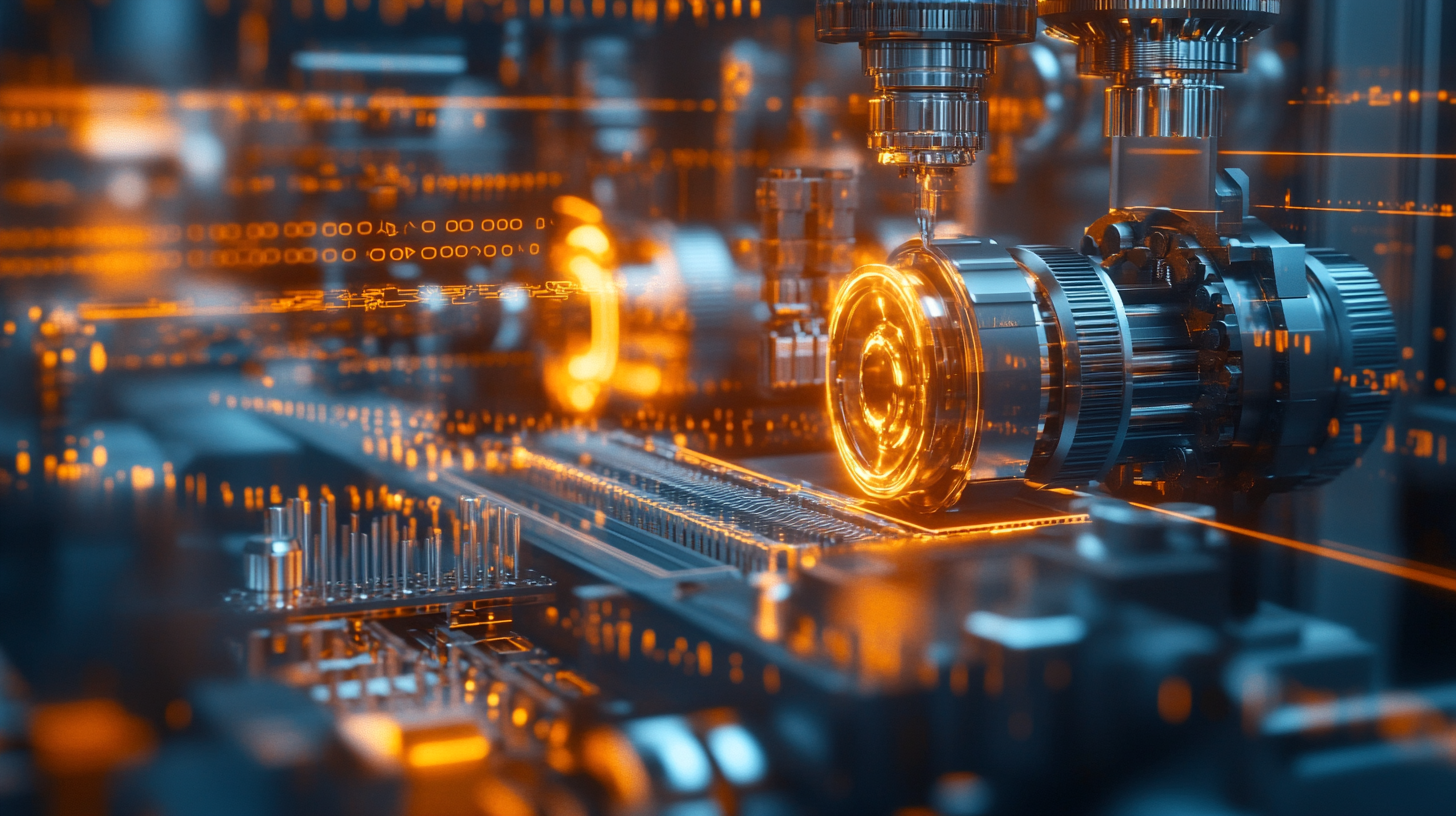
Versatility in Design: The Role of CNC Machining in Custom Manufacturing
In the ever-evolving landscape of modern manufacturing, CNC machining has established itself as an indispensable tool that enhances versatility in design. With the ability to create intricate and custom components, CNC machining allows manufacturers to adapt quickly to changing market demands and consumer preferences. This adaptability is not just a feature; it's a necessity in today’s competitive environment. Manufacturers can produce a wide variety of products, ranging from aerospace parts to medical devices, all tailored to specific requirements with precision and efficiency.
Recent advancements in laser cutting technology and rapid prototyping further highlight the transformative role CNC machining plays in custom manufacturing. These technologies enhance creativity, enabling designers to push the boundaries of traditional manufacturing. By integrating CNC machining with laser cutting and 3D printing technologies, companies can realize complex shapes and functionalities that were previously unimaginable. This synergy between different manufacturing techniques fosters innovation and streamlines production processes, ensuring that businesses remain agile and responsive.
Moreover, CNC machining equipment is continuously evolving to improve production capabilities. New tools designed for optimum performance reduce setup times and enhance precision, allowing manufacturers to focus on their core mission—delivering quality products without compromising efficiency. As industries continue to embrace automation and advanced technological solutions, the importance of CNC machining centers becomes ever more evident, solidifying their essential role in achieving modern manufacturing success.

Reducing Waste: How CNC Machining Centers Minimize Material Usage
CNC machining centers have revolutionized the manufacturing landscape by significantly reducing material waste, thereby enhancing operational efficiency. According to the 2021 report from the Global Manufacturing Alliance, nearly 30% of raw materials are wasted in traditional machining processes. CNC machines, with their precise control and automation capabilities, can help reduce this waste by up to 70%. This reduction translates into significant cost savings and a decreased environmental impact, making CNC technology indispensable for modern manufacturers.
One of the core principles behind the efficiency of CNC machining centers is their ability to utilize advanced software systems that optimize cutting paths and material layouts. A study by the National Institute of Standards and Technology highlighted that manufacturers utilizing CNC technology can achieve a reduction in scrap rates from about 20% to below 5%. This shift not only preserves valuable resources but also supports sustainability efforts by lowering the carbon footprint associated with excessive waste production.
Furthermore, CNC machining centers often incorporate real-time monitoring and adaptive control systems that allow for continuous adjustments during the manufacturing process. This capability minimizes the risk of errors that can lead to material waste. Research from the Institute of Mechanical Engineers indicates that implementing CNC machining can result in more than 25% higher material yield compared to traditional methods. As businesses continue to embrace these technologies, the evidence clearly supports the critical role CNC machining centers play in optimizing material usage and driving success in today’s competitive manufacturing environment.
Enhancing Competitiveness: The Strategic Importance of CNC in Modern Factories
CNC machining centers are revolutionizing modern manufacturing, offering unparalleled precision and adaptability that are essential for maintaining competitiveness in today’s fast-paced industrial landscape. According to a recent report, companies leveraging CNC technology can increase productivity by up to 30% while significantly reducing production times. This heightened efficiency not only lowers operational costs but also allows manufacturers to quickly respond to market demands—a crucial factor in an era characterized by rapid changes in consumer preferences.
Moreover, the strategic importance of CNC in reconfigurable manufacturing systems cannot be overstated. With the rise of Industry 4.0, manufacturers are increasingly integrating CNC machines with advanced automation and IoT technologies. This integration facilitates real-time data collection and analysis, enabling companies to optimize their production processes. A study indicates that manufacturers who adopt such smart systems can achieve up to 15% improvement in overall equipment effectiveness (OEE).
As competition intensifies, the adoption of CNC machining not only enhances operational efficiency but also supports innovation in product design and development. Industry experts suggest that firms investing in CNC technology are better positioned to adapt to new product life cycles and evolving market needs. By embracing these advanced manufacturing techniques, companies can ensure that they remain at the forefront of their industries, paving the way for future growth and success.