Exploring Future Innovations in CNC Lathes for Global Manufacturers in 2025
As we venture into 2025, the manufacturing landscape is poised for transformative changes driven by technological advancements. CNC lathes, pivotal in precision machining, play a critical role in enhancing production efficiency and accuracy. According to the Industry Research Report by Grand View Research, the global CNC lathe market is projected to reach USD 10.95 billion by 2025, growing at a compound annual growth rate (CAGR) of 7.4%. This surge underscores the increasing reliance of global manufacturers on advanced CNC technologies to meet rising consumer demands and maintain competitive advantages.
The innovations in CNC lathes are not just limited to hardware enhancements; they encompass smart manufacturing principles such as IoT integration and machine learning algorithms. A report from Markets and Markets indicates that smart manufacturing is expected to grow from USD 216.8 billion in 2021 to USD 384.8 billion by 2025, further illustrating the trend's impact across the industry. These advancements promise to optimize machining processes, reduce downtime, and improve data analytics for manufacturers worldwide. As we explore future innovations in CNC lathes, it’s essential to understand how these technological strides will shape the manufacturing sector on a global scale.
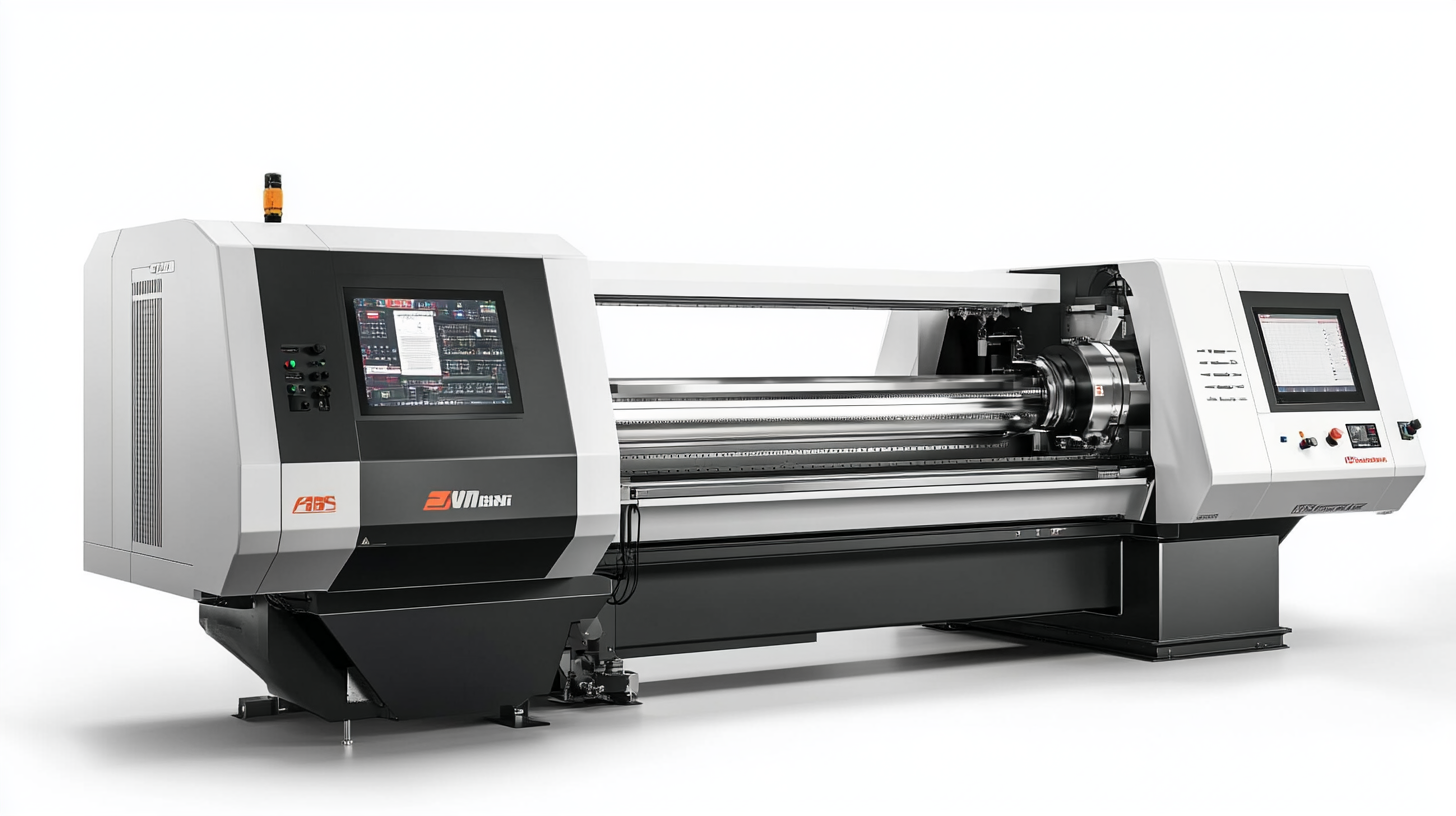
Emerging Technologies Shaping CNC Lathes: A 2025 Perspective
As we venture into 2025, the evolution of CNC lathes stands at the forefront of innovation, shaped by emerging technologies that promise to redefine manufacturing processes. Recent studies emphasize the growing integration of advanced automation and IoT-enabled machinery, predicting that these elements will become standard in leading manufacturing facilities. According to industry analyses, the global CNC machining service market is expected to experience exponential growth, with a projected increase in demand driven by advancements in precision and efficiency across various sectors, especially in the medical field. One notable trend is the development of hybrid CNC machines that combine additive and subtractive manufacturing capabilities. This innovation not only streamlines production processes but also enhances material utilization, significantly reducing waste. Collaborative efforts among key players in the market are paving the way for these advanced solutions, which are anticipated to enter the market soon. Experts note that by leveraging such technologies, manufacturers can achieve unparalleled flexibility and customization in their operations. Moreover, the incorporation of artificial intelligence in CNC machining is set to revolutionize how data is processed and utilized. With AI-driven insights, manufacturers can expect to enhance predictive maintenance and optimize production schedules, ultimately leading to reduced downtimes and increased profitability. As the industry progresses, staying informed about these trends and innovations will be crucial for manufacturers aiming to maintain a competitive edge in a rapidly evolving landscape.
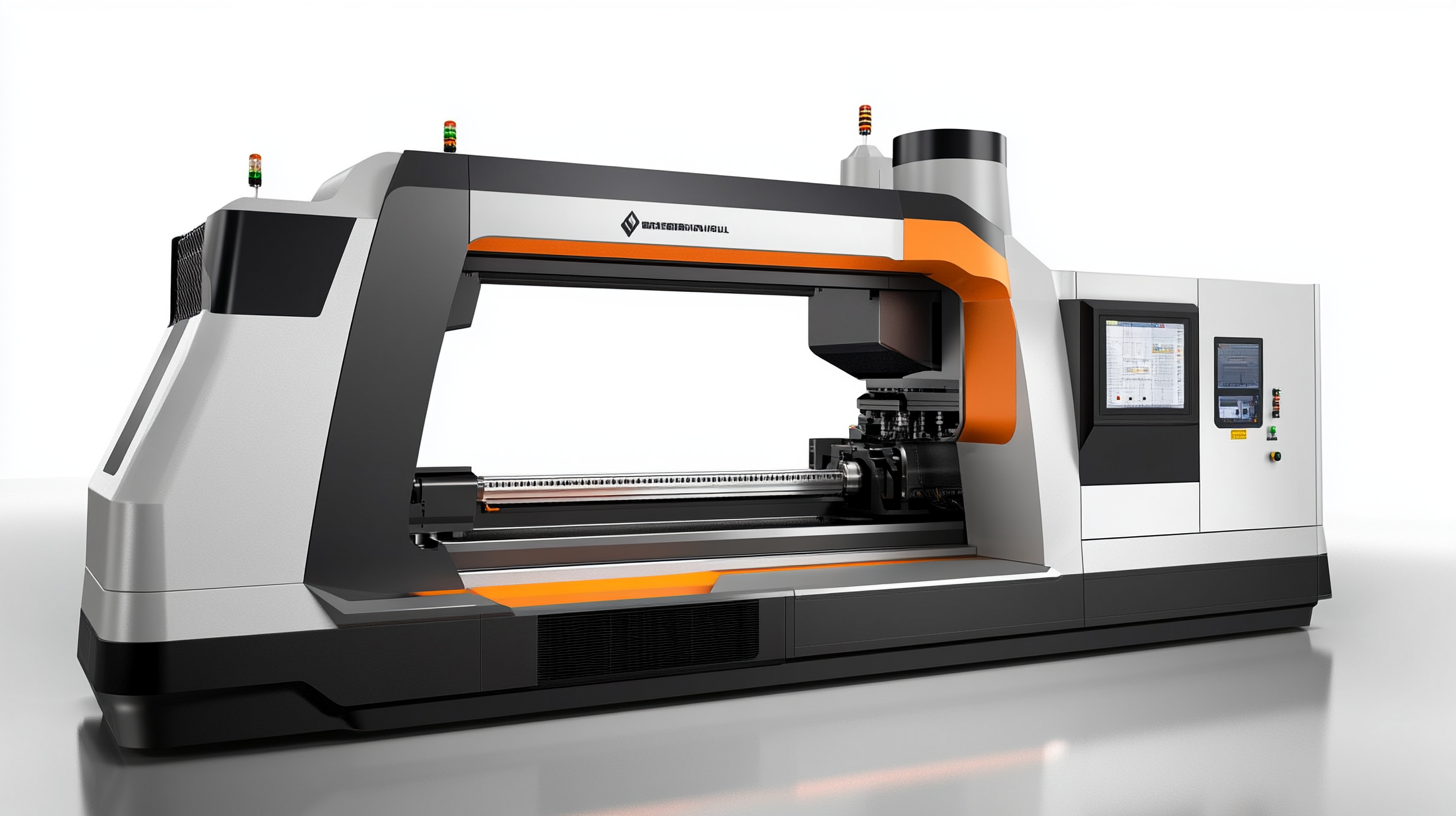
Sustainability Trends in CNC Machining: Innovations for Eco-Friendly Production
The landscape of CNC machining is rapidly transforming as global manufacturers increasingly prioritize sustainability in their production strategies. As we look ahead to 2025, the integration of eco-friendly innovations is set to redefine the operational frameworks within which these machines operate. Key trends include the adoption of energy-efficient technologies that minimize waste and optimize energy consumption, ensuring that the environmental footprint of CNC operations is significantly reduced.
On the forefront of this eco-tech revolution are advancements in renewable energy technology and the circular economy framework. Manufacturers are now deploying advanced CNC lathes that not only improve precision and productivity but also utilize energy sourced from renewables. This shift not only supports sustainability goals but also aligns with regulatory changes aimed at promoting greener practices in industrial operations. Additionally, the circular economy principles encourage manufacturers to rethink materials and processes, leading to the recovery and reuse of resources, ultimately transforming waste into valuable inputs.
Moreover, the incorporation of cutting-edge technologies such as IoT and AI in CNC machining promises to enhance sustainable practices through greater data visibility and real-time decision-making. These technological advancements enable manufacturers to monitor their processes more efficiently, thereby identifying inefficiencies and implementing corrective actions swiftly. As the drive towards sustainability intensifies, the machine tool industry will continue to evolve, reflecting a commitment to innovation that prioritizes both production effectiveness and ecological responsibility.
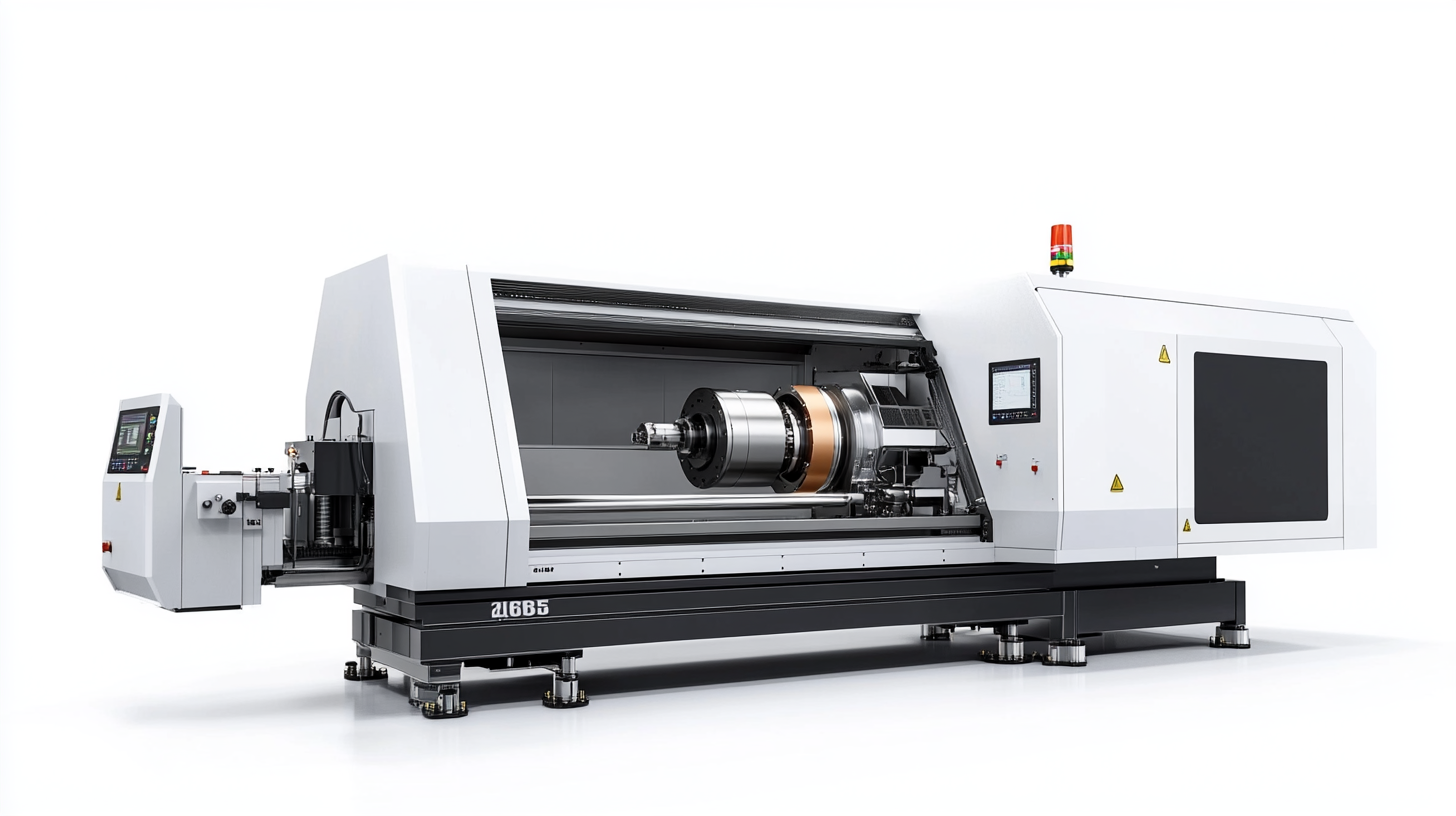
Integrating AI and Machine Learning in CNC Lathe Operations for Enhanced Precision
As we approach 2025, the integration of artificial intelligence (AI) and machine learning into CNC lathe operations is set to redefine manufacturing precision and efficiency. The National Institute of Standards and Technology (NIST) has been exploring AI-enhanced monitoring systems that promise to elevate the standard of manufacturing processes. By leveraging AI, manufacturers can achieve real-time insights into operational efficiencies and defect detection, ultimately enhancing the reliability of complex precision machined parts.
Amidst this technological evolution, the CNC machine market is projected to grow at a CAGR of 5.5%, driven by the increasing demand for smart manufacturing solutions. Innovations such as Romi's custom CNC lathes and advanced 12-axis turning centers are testament to the industry’s shift towards enhanced precision. These advanced machine tools not only improve wear resistance but also streamline the machining processes for turning, milling, and drilling operations, offering unprecedented accuracy and reliability.
Furthermore, the future of metrology and precision engineering is undergoing a significant transformation, with AI playing a pivotal role. Advanced measurement techniques are being developed, allowing manufacturers to monitor and control their processes with greater accuracy than ever before. This symbiotic relationship between AI and metrology ensures that quality standards in manufacturing are not just met but exceeded, positioning companies for success in an increasingly competitive global market.
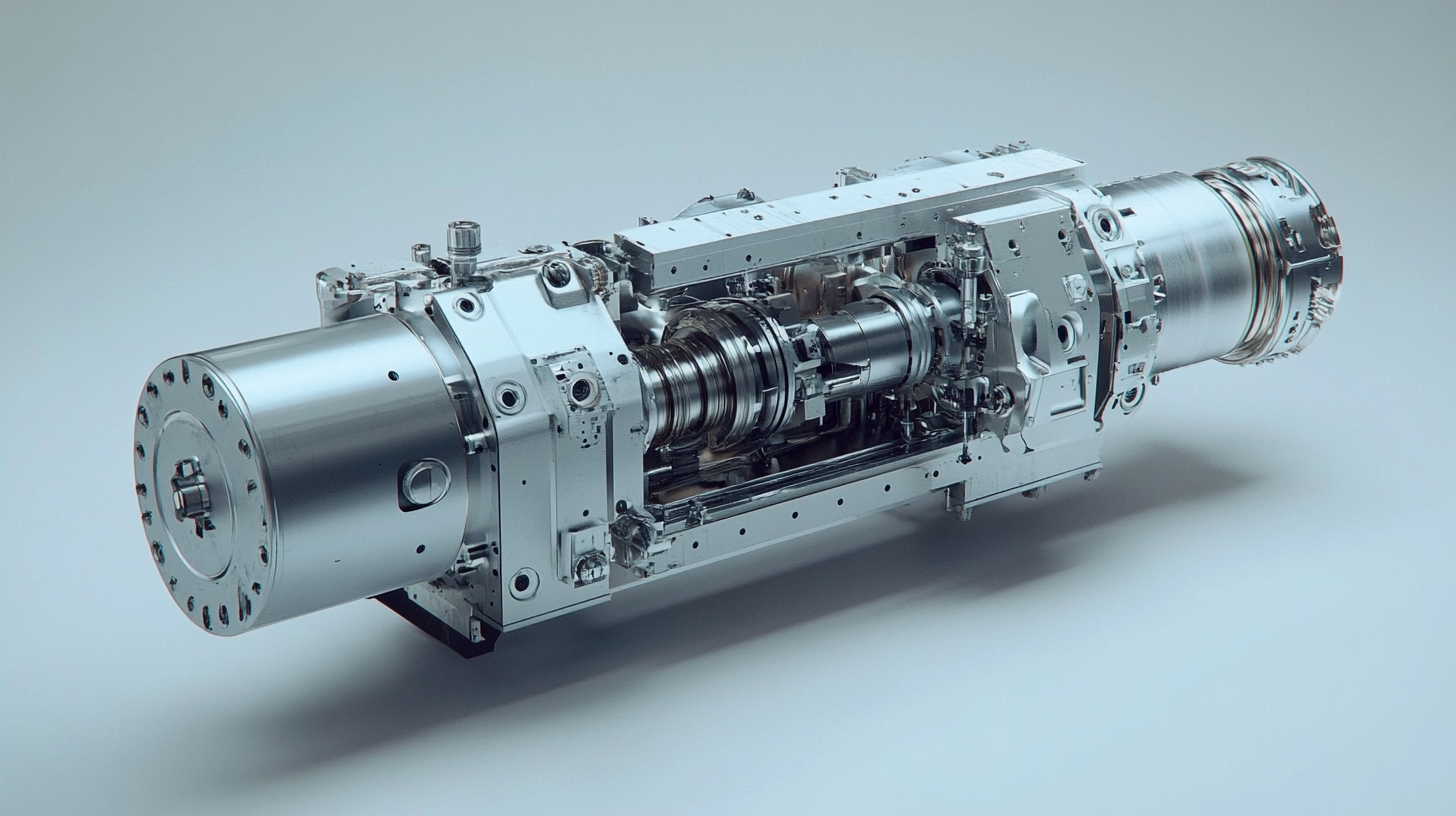
Exploring Advanced Materials: The Future of CNC Lathe Manufacturing
As we look toward the future of CNC lathe manufacturing, advanced materials are set to revolutionize the industry. The integration of innovative materials, such as composites and lightweight alloys, is increasingly becoming a priority for manufacturers aiming to enhance performance and efficiency. Recent reports indicate that the global market for advanced materials is expected to reach $3 trillion by 2025, reflecting the growing emphasis on material science in manufacturing processes.
The 2023 International Manufacturing Technology Show showcased the latest advancements in additive manufacturing and rapid prototyping. These technologies allow manufacturers to test and produce components with high precision at remarkable speeds, which is critical for the CNC lathe sector. For instance, AI-driven systems can analyze and optimize production parameters in real-time, enabling the use of bespoke materials that meet specific engineering demands. The adoption of digital twin technology further enhances this process, allowing manufacturers to simulate performance before investing in physical production.
Moreover, the incorporation of IoT in CNC lathe operations facilitates predictive maintenance and data-driven decision-making. This means that manufacturers can utilize advanced materials more effectively, ensuring that parts remain durable and aligned with the requirements of modern industrial applications. As we advance toward 2025, it’s evident that the synergy between advanced materials and CNC lathe technology will define new benchmarks for quality and productivity in manufacturing.
Global Market Trends: How CNC Lathes are Adapting to Industry 4.0 Requirements
As we move towards 2025, the integration of Industry 4.0 into manufacturing processes is reshaping the landscape of CNC lathes. These advanced machines are evolving in response to global market trends that demand higher precision and smarter operations. The CNC machine tools market is projected to grow by USD 21.9 billion from 2025 to 2029, reflecting an increasing need for high-precision, multi-axis machining centers. This growth is significantly driven by the incorporation of artificial intelligence, which is transforming how manufacturers operate their lathes.
AI technology is at the forefront of this transformation, enabling CNC lathes to become more adaptive and efficient. By leveraging machine learning algorithms, these tools can optimize production processes, predict maintenance issues, and enhance overall operational efficiency. The demand for lathe machines is further fueled by rising infrastructure investments, which are expected to contribute USD 16.6 billion to the metal machining market over the same period. This trend showcases how CNC lathes are not only meeting the needs of today’s manufacturing environment but are also being designed to accommodate future requirements in precision engineering.
In this era of digitalization, manufacturers must stay ahead of technological advancements to remain competitive. The shift towards smart manufacturing with CNC lathes equipped with AI capabilities will redefine production standards, offering new levels of customization and efficiency. As we look to the future, it is clear that CNC lathes will play a critical role in revolutionizing manufacturing processes and meeting the evolving needs of global industries.