Unlocking Precision: The Future of CNC Machining Centers for Global Buyers
In the rapidly evolving landscape of manufacturing technology, CNC machining centers have emerged as a pivotal tool for precision engineering. According to a recent report by MarketsandMarkets, the global CNC machining centers market is projected to reach $100 billion by 2025, growing at a compound annual growth rate (CAGR) of 5.1%. This growth is driven by increased demand for high-efficiency manufacturing processes and the rising need for automation across various industries. As businesses strive for enhanced productivity and quality, investing in advanced CNC machining centers becomes essential for staying competitive in a global market.
Furthermore, the integration of smart manufacturing technologies, such as IoT and AI, is transforming the capabilities of CNC machining centers. A study by McKinsey highlights that companies adopting these innovations could boost their productivity by up to 30%. Global buyers are now looking for machining centers that not only provide precision but also adaptability to changing manufacturing needs. This shift underscores the significance of understanding the future trajectory of CNC machining centers, where technology and precision intersect to redefine manufacturing standards and drive efficiency.
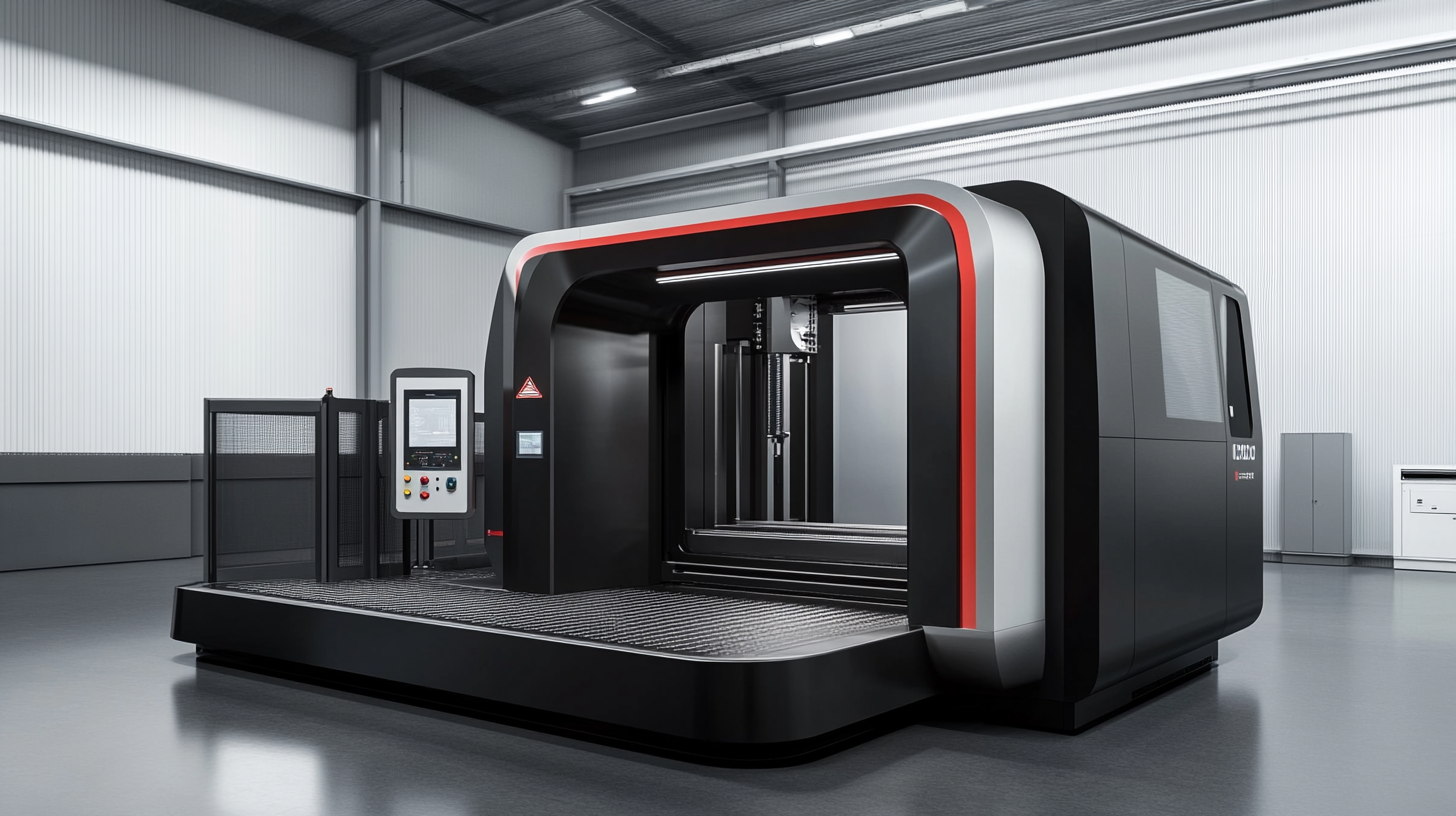
The Evolution of CNC Machining Centers: A Look at Technological Advancements
The evolution of CNC machining centers has been significantly influenced by technological advancements, marking a pivotal moment in the manufacturing industry. With the global CNC machine market projected to grow from $101.22 billion in 2025 to $195.59 billion by 2032, it is clear that innovations such as Industry 4.0 technologies are driving this transformation. This new era emphasizes intelligent manufacturing, where interconnected systems and data analytics streamline processes, enhance efficiency, and foster precision. As manufacturers increasingly adopt advanced CNC machining and turning centers, the market is set to expand at a compound annual growth rate (CAGR) of 6.6% from 2024 onwards. These state-of-the-art machines are equipped with smart technologies that allow for predictive maintenance and real-time performance monitoring, enabling more responsive and adaptive production strategies. The integration of such technologies not only improves operational efficiency but also allows manufacturers to meet the growing demands for customization and shorter production cycles. Moreover, technology convergence plays a crucial role in refining the capabilities of CNC machining centers. Innovations that combine different technological streams, such as artificial intelligence, IoT, and robotics, create a synergistic effect, leading to unparalleled advancements in manufacturing processes. As we observe these trends, it is evident that the future of CNC machining is not just about the machines themselves, but about how they interconnect and operate within a broader, increasingly intelligent manufacturing ecosystem.
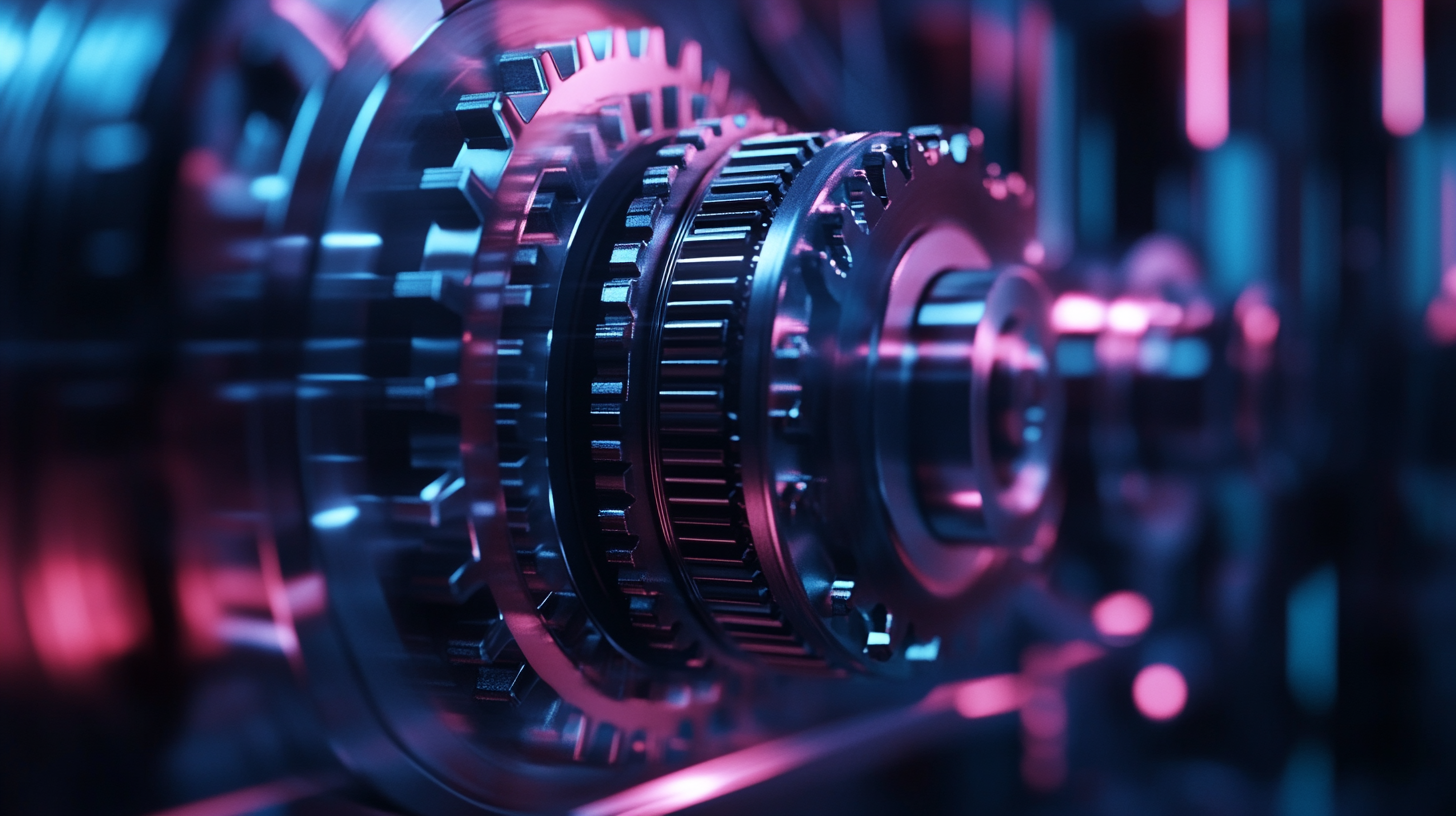
Key Features to Consider When Choosing CNC Machining Centers for Your Business
When selecting CNC machining centers for your business, several key features must be prioritized to ensure precision, efficiency, and long-term profitability. A report by MarketsandMarkets indicates that the global CNC machining market is projected to reach $100 billion by 2026, highlighting the significance of making informed choices in this advancing sector.
One crucial feature to consider is the type of control system. Modern CNC machines utilize advanced numerical control systems that provide greater flexibility and precision. According to a study by Technavio, technologies such as integrated CAD/CAM systems can enhance productivity by up to 30%. This integration allows for seamless transitions from design to manufacturing, reducing errors and lead times.
Another essential aspect is the machine's rigidity and stability. According to a recent survey conducted by the American Society of Mechanical Engineers (ASME), about 45% of machining defects arise from vibrations during manufacturing. Therefore, investing in a CNC machining center with robust structural integrity is imperative to minimizing these vibrations and enhancing overall machining accuracy.
Moreover, businesses should also assess the machine’s automation capabilities. A report from Deloitte emphasizes that companies adopting automated CNC solutions can achieve up to 20% reductions in operational costs. This increased automation package leads to improved production rates and ensures that high-quality standards are consistently met, making it a vital consideration for buyers in today’s competitive landscape.
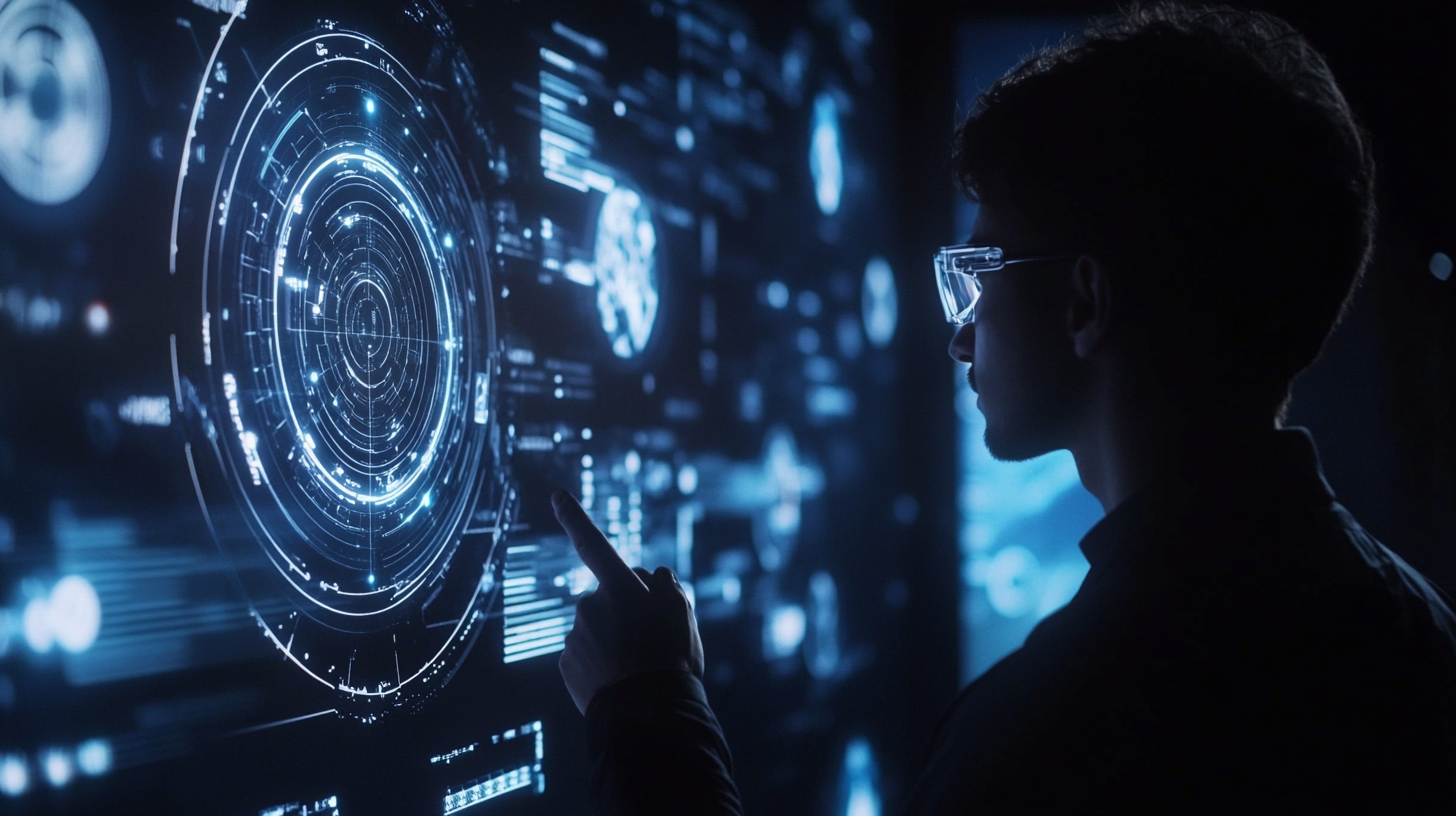
How Automation and AI are Shaping the Future of CNC Machining
The advent of automation and artificial intelligence (AI) is poised to revolutionize the CNC machining industry, offering unprecedented precision and efficiency. According to a report by Markets and Markets, the global CNC machine market is projected to reach $118.4 billion by 2026, growing at a CAGR of 6.8% from 2021. This growth is largely fueled by advancements in automation technologies that enhance the capabilities of CNC machining centers.
AI integration allows for real-time data analytics and predictive maintenance, reducing downtime and optimizing production processes. A study by McKinsey highlights that manufacturers that implement AI-driven automation can reduce production costs by up to 20%. By leveraging machine learning algorithms, CNC machines can now self-diagnose issues and adapt to changing manufacturing environments, further elevating productivity levels.
Moreover, the utilization of robotics in CNC machining is becoming increasingly common. The International Federation of Robotics reports that robotic installations in manufacturing reached a record high in 2020, with a 30% increase compared to the previous year. This surge demonstrates an industry shift towards more automated solutions, with CNC machining centers incorporating robotic arms to handle complex tasks seamlessly, thus ensuring accuracy and efficiency.
As global buyers seek higher quality and faster turnaround times, the synergy between CNC machining and advanced technologies like automation and AI is not just enhancing operational capabilities but is also setting new standards for the industry as a whole. With these innovative solutions, the future of CNC machining centers looks promising, promising to deliver unmatched precision and a competitive edge in the global market.
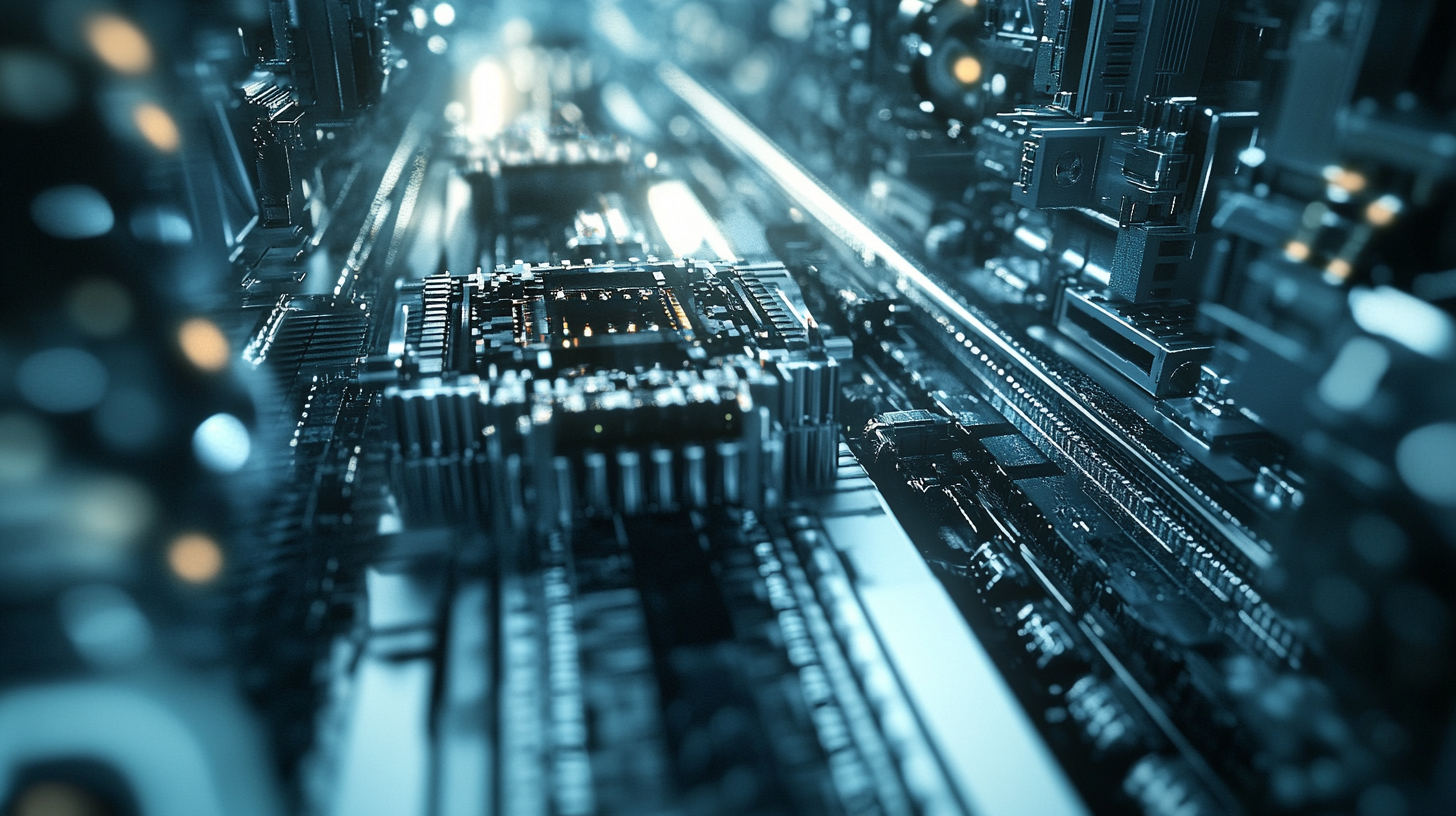
Global Market Trends: What Buyers Need to Know About CNC Technology
As the manufacturing landscape evolves, CNC (Computer Numerical Control) machining technology emerges as a paramount tool for precision and efficiency. Understanding the global market trends in CNC technology is essential for buyers looking to invest in new machinery or upgrade existing equipment. With the industry rapidly advancing, features such as automation, advanced software integration, and smart manufacturing capabilities are becoming vital considerations in the purchasing process.
One of the key trends transforming the CNC machining industry is the integration of Industry 4.0 technologies. This shift allows machines to communicate with each other and with the cloud, leading to improved production efficiency and reduced downtime. Buyers must be aware of how these advancements can optimize their operations and provide real-time analytics to enhance decision-making. Moreover, eco-friendliness and energy efficiency are now more critical than ever, as manufacturers seek to reduce their carbon footprint in response to global sustainability initiatives.
Additionally, the global demand for customized solutions continues to rise, prompting CNC manufacturers to offer more flexible and adaptive machines. Buyers should consider the versatility of CNC machining centers to accommodate small batch production and complex geometries, enabling them to meet industry-specific needs. Staying informed about these trends will empower buyers to make knowledgeable decisions, ensuring their investments align with both current capabilities and future demands in the rapidly changing global market.
Sustainability in CNC Machining: Addressing Environmental Concerns and Innovations
As the world increasingly prioritizes sustainability, the CNC machining industry is stepping up to meet environmental challenges with innovative solutions. Traditional machining processes often generate significant waste and energy consumption, raising concerns about their long-term viability. However, advances in technology and a growing awareness of eco-friendly practices are paving the way for a greener future in CNC machining.
One notable innovation is the development of energy-efficient machinery that consumes less power without compromising performance. These machines utilize advanced power management systems and regenerative braking, significantly reducing their environmental footprint. Furthermore, improvements in tooling and cutting techniques have led to a decrease in material wastage, ensuring that resources are used more effectively while maintaining high precision in production.
In addition to machine advancements, sustainable practices are being integrated into the entire manufacturing process. Companies are increasingly adopting closed-loop systems that recycle materials and manage waste better. The use of biodegradable lubricants and coolants is also gaining traction, minimizing harmful chemical releases into the environment. By embracing these sustainable innovations, CNC machining centers are not only enhancing their operational efficiency but also playing a crucial role in the global movement towards environmental responsibility.