Exploring the Advantages of Integrating Lathe and Milling Machine in Modern Manufacturing
In the ever-evolving landscape of modern manufacturing, the integration of advanced machinery plays a pivotal role in enhancing productivity and precision. Among the most influential tools in this field are the lathe and milling machine, both of which have traditionally served distinct functions. However, as technology continues to advance, the synergy created by merging these two powerful machines is garnering attention for its numerous advantages. This blog delves into how integrating a lathe and milling machine can revolutionize manufacturing processes, offering unparalleled capabilities and efficiencies.
By combining the strengths of both machines, manufacturers can achieve a higher level of versatility, allowing for complex shapes and intricate designs to be produced with greater accuracy and consistency. The collaboration of the lathe and milling machine not only streamlines operations but also minimizes the need for multiple setups, thereby reducing production time and costs. In the following sections, we will explore the various benefits of this integration, providing insights into how modern manufacturers can harness the full potential of lathe and milling machines to stay competitive in today’s market.
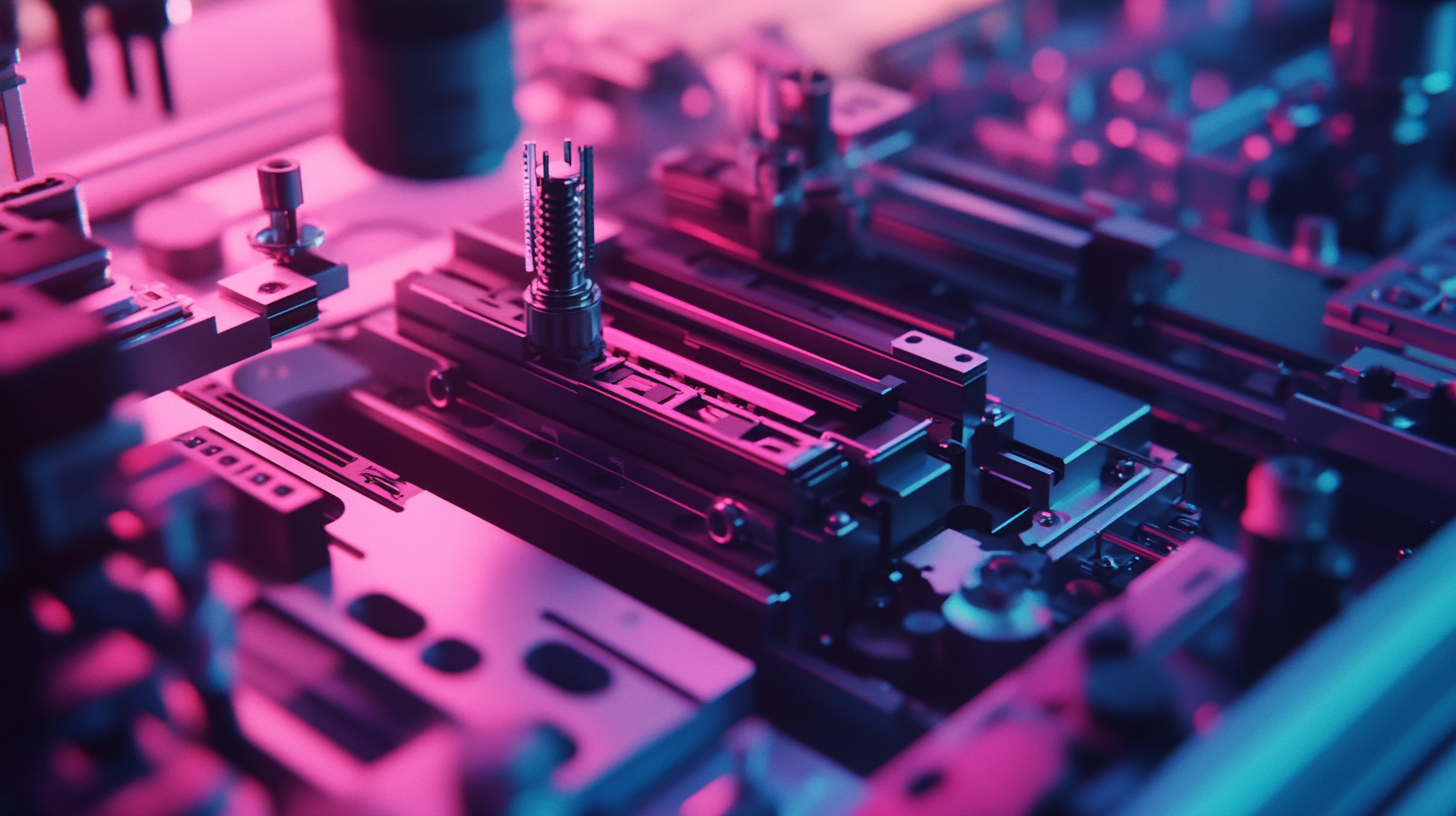
Innovative Approaches: The Role of Lathe and Milling Machine Integration in Manufacturing
The integration of lathe and milling machines in modern manufacturing represents a significant leap towards maximizing efficiency and precision in production lines. By blending these two versatile machining processes, manufacturers can achieve streamlined operations that minimize downtime while enhancing output quality. This integration not only reduces the space needed for multiple machines but also allows for a more cohesive approach to machining tasks, ultimately leading to increased productivity. As Industry 4.0 continues to reshape manufacturing landscapes, the roles of predictive maintenance and real-time data analytics become crucial. Leveraging IoT technologies and big data helps facilitate proactive strategies that can preemptively address potential issues in lathe and milling machines. This data-driven approach fosters a cyber-physical system where machine tools operate with greater intelligence, adapting to changing production demands and ensuring the longevity of the equipment. By integrating integrated force sensors and advanced monitoring systems, manufacturers can closely observe tool wear and performance, leading to more effective maintenance schedules. Moreover, sustainability in manufacturing is increasingly incorporated within the operational framework of lathe and milling integration. Innovative methods and materials are being developed to reduce waste, energy consumption, and overall environmental impact. As producers invest in sustainable practices, the engagement of advanced machining techniques not only supports ecological goals but also aligns with market demands for environmentally-conscious production. The symbiosis of efficiency, intelligence, and sustainability heralds a new era for manufacturing industries, where the integration of lathe and milling machines plays a pivotal role in shaping their future.
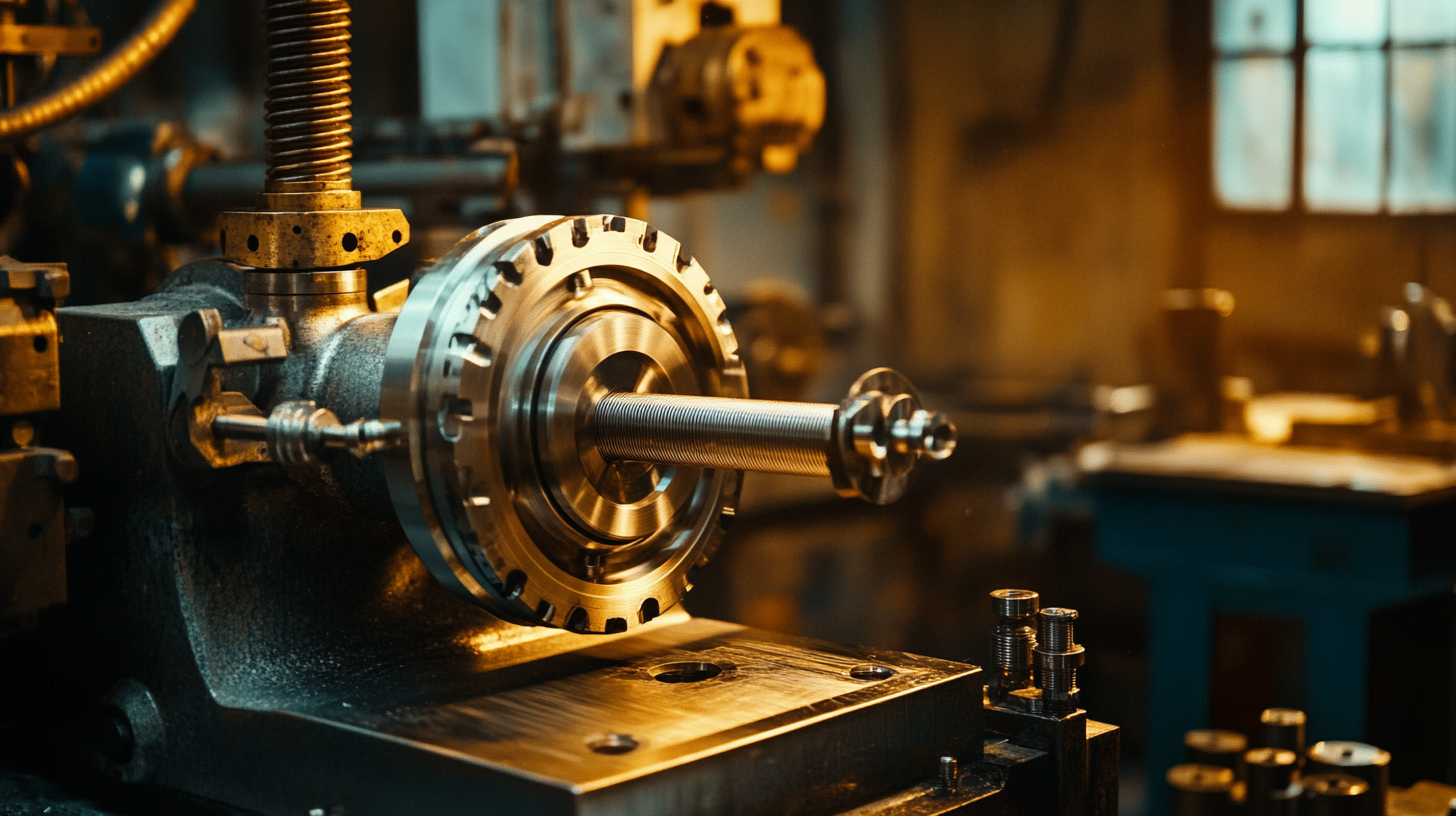
Enhancing Precision: Benefits of Using Combined Machining Processes
The integration of lathe and milling machine processes in modern manufacturing has revolutionized the landscape of precision engineering. By combining these two machining processes, manufacturers can achieve significantly enhanced accuracy in the production of complex parts. The synergy between lathes and mills allows for intricate profiles and detailed features to be machined in a single setup, which minimizes the risk of alignment errors that often occur when parts are transferred between machines.
One of the primary advantages of using combined machining processes is the substantial reduction in cycle times. When both turning and milling operations are performed in one equipment, the need for multiple setups and positions is eliminated. This not only accelerates production speed but also optimizes workflow efficiency, enabling manufacturers to meet tight deadlines without sacrificing quality. Moreover, the integration leads to cost savings in terms of labor and machine maintenance, as fewer machines mean reduced operational overhead.
In addition to efficiency and cost-effectiveness, the combined approach also enhances the overall quality of the finished products. Precision is paramount in industries such as aerospace and automotive, where tolerances are incredibly tight. By utilizing a lathe-mill combination, manufacturers can ensure that each component meets stringent specifications. The ability to conduct both operations in one machine facilitates superior surface finishes and higher accuracy, ultimately resulting in products that demonstrate improved performance and reliability in their applications.
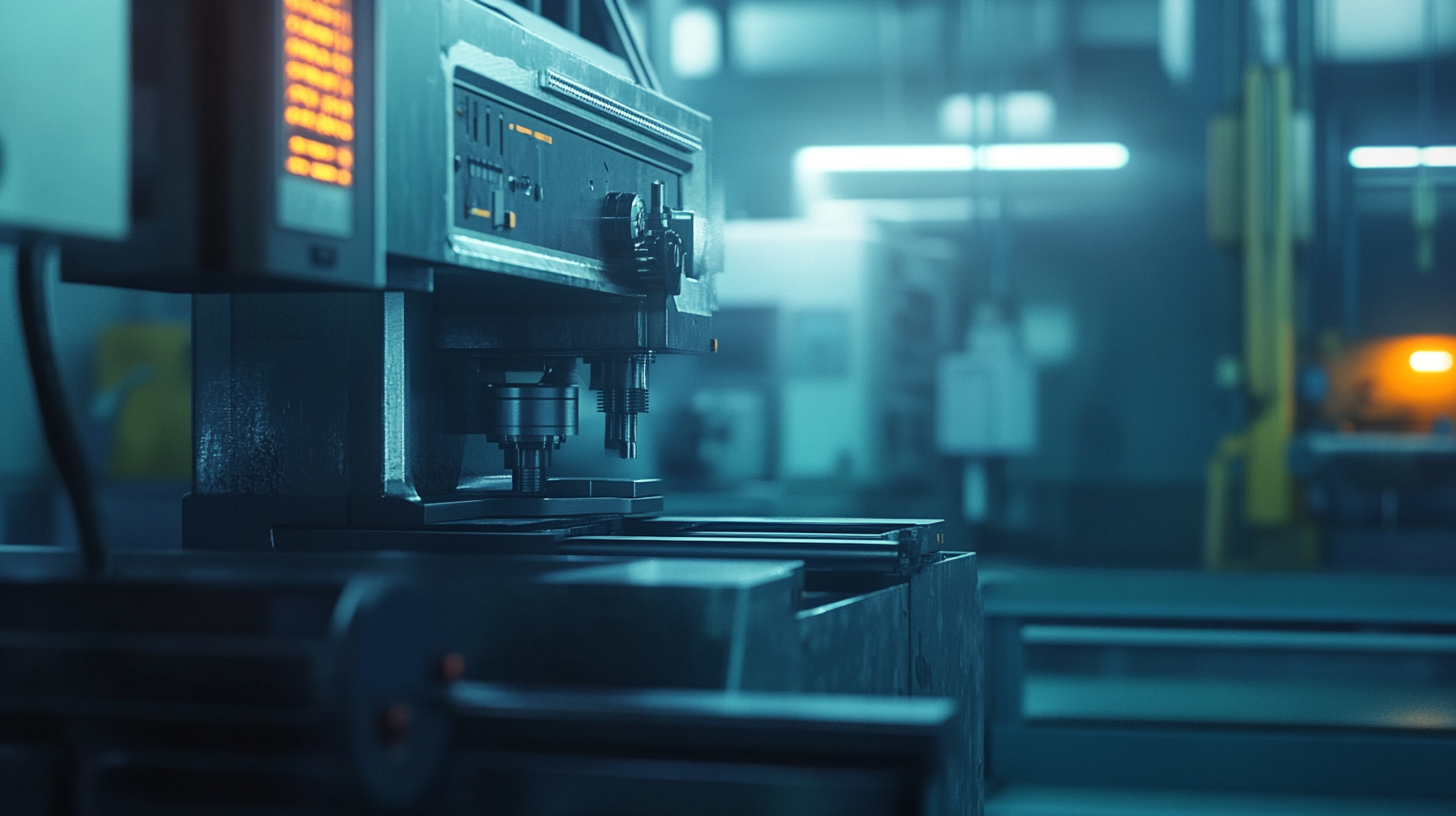
Cost Efficiency: How Lathe and Milling Machine Integration Reduces Production Expenses
The integration of lathe and milling machines in modern manufacturing brings a paradigm shift in terms of cost efficiency. Traditional manufacturing processes often require separate operations for turning and milling, which can lead to increased labor and time expenses. However, by combining these two critical functionalities into a single setup, manufacturers can streamline their workflow, significantly reducing operational costs. The reduced setup time and minimized transportation of components between machines translate into a more efficient production process.
Moreover, integrating lathe and milling machines enables better resource utilization. High-precision workpieces are produced in fewer steps, which not only saves time but also lowers the need for excessive material handling. This synergy allows companies to maximize their equipment's capabilities, ultimately leading to less wasted material and lower overall manufacturing costs. Additionally, with reduced energy consumption associated with fewer machines in operation, businesses can also benefit from lower utility bills.
The advantages extend beyond just cost savings. In an era where efficiency and productivity are paramount, manufacturers who embrace this integration are well-positioned to remain competitive. The ability to offer higher quality products with shortened lead times becomes a significant differentiator in the marketplace. As the industry continues to evolve, integrating lathe and milling machines proves to be not just a practical choice, but a strategic one for modern manufacturing success.
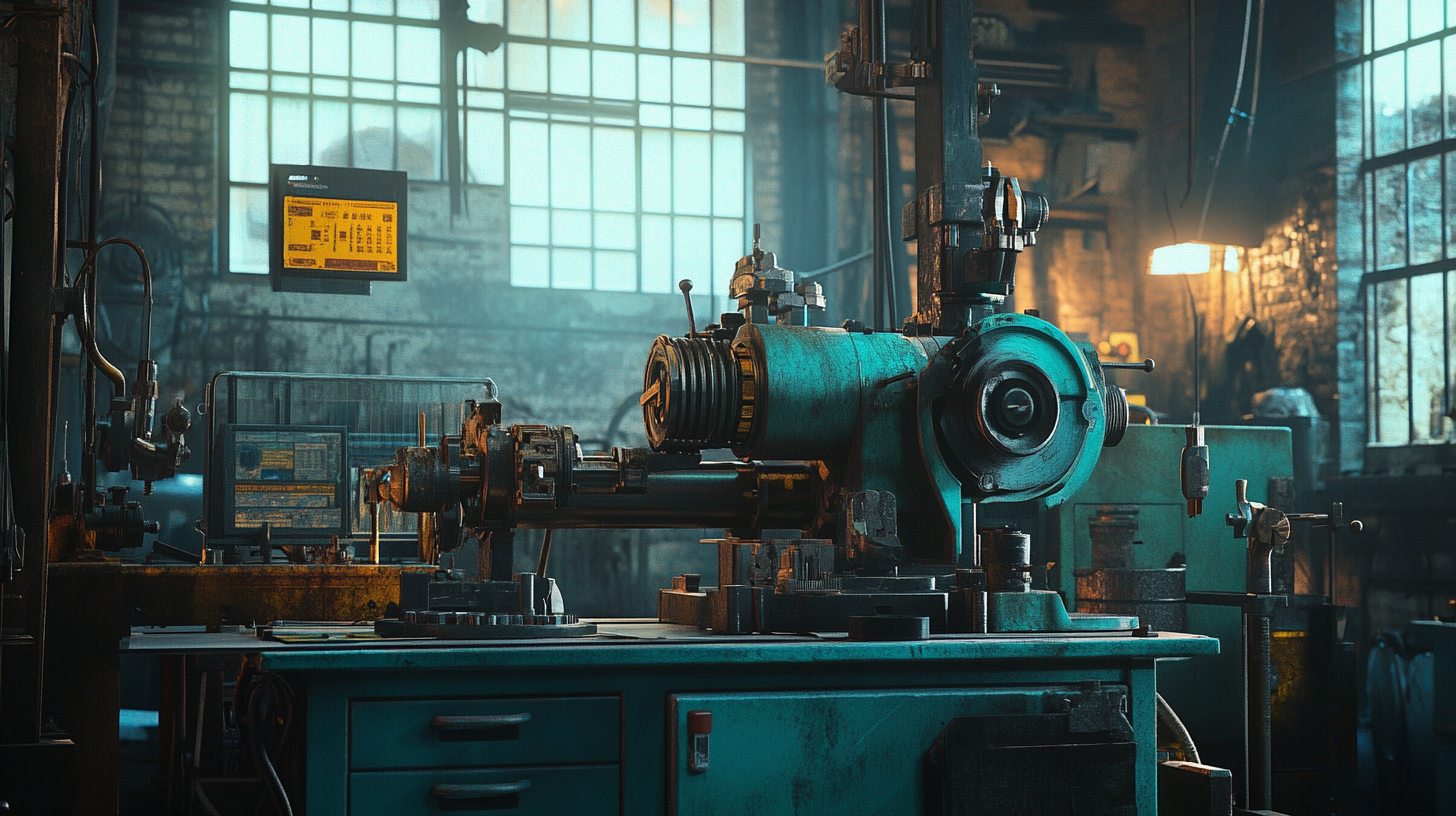
Versatility in Design: Expanding Capabilities through Machine Integration
In the rapidly evolving landscape of modern manufacturing, integrating lathe and milling machines has become a game-changer, particularly in enhancing design versatility. According to a report by the International Society for Automation, manufacturers that have adopted integrated machining centers can increase productivity by up to 30%. This seamless combination allows for more complex geometries and intricate designs that traditional machining processes can't achieve alone, thereby expanding the range of possible applications.
The advantages of machine integration extend beyond just efficiency; they significantly reduce setup times. A study by the Manufacturing Institute highlighted that integrated systems can cut setup time by nearly 50%, allowing companies to respond more swiftly to market demands. This agility is crucial in industries where time-to-market is a competitive advantage, enabling manufacturers to craft custom products tailored to specific customer needs without the traditional delays associated with switching between separate machines.
Moreover, integrating lathe and milling capabilities fosters innovation. Engineers can combine turning and milling operations to create sophisticated components in a single setup, encouraging creativity in design. As reported in the Journal of Manufacturing Processes, manufacturers utilizing integrated machining reported a 20% increase in the variety of products they could offer. This flexibility not only boosts competitiveness but also positions companies to better explore new markets and technologies, ultimately driving growth in an increasingly complex manufacturing environment.
Streamlining Production: The Impact of Integrated Machining on Manufacturing Workflow
In the rapidly evolving landscape of modern manufacturing, the integration of lathe and milling machines is becoming increasingly vital for streamlining production processes. This seamless collaboration is not just about improving efficiency; it encompasses a fundamental shift towards digital manufacturing paradigms. By utilizing synchronized machining techniques, manufacturers can achieve a significant reduction in lead times and enhance the overall quality of their products.
One of the standout benefits of integrated machining is its ability to simplify the workflow. The conventional linear manufacturing process is being replaced with a more dynamic approach, allowing for real-time adjustments and optimizations. When lathe and milling operations are combined, there is less need for part handling and setup changes, which minimizes downtime and creates a more fluid production cycle. This is further augmented by the rise of additive manufacturing technologies, which complement traditional methods by enabling rapid prototyping and customization.
Furthermore, as industries embrace lean manufacturing principles, the integration of various machining processes proves to be a strategic advantage. By improving the synergy between lathe and milling machines, manufacturers not only enhance operational efficiency but also boost product quality. The shift towards digital solutions, including the adoption of additive manufacturing, supports this transformation by offering innovative ways to produce complex geometries that were previously challenging to achieve. As manufacturing continues its digital evolution, the combination of integrated machining and advanced technologies will be crucial for staying competitive in the market.