Maximizing Value with Quality Used Machine Tools Through Cost Effective Maintenance Solutions
In the competitive landscape of manufacturing, leveraging the benefits of used machine tools can significantly enhance operational efficiency and overall productivity. As businesses strive to optimize their resources, understanding how to maximize the value of these assets becomes critical. Quality used machine tools present a unique opportunity for manufacturers, allowing them to reduce upfront costs while still maintaining high standards of performance and reliability. However, to truly harness the potential of these machines, a strategic approach to maintenance is essential.
Cost-effective maintenance solutions not only prolong the lifespan of used machine tools but also ensure they operate at peak performance. By implementing preventative measures, regular inspections, and timely repairs, manufacturers can avoid costly downtime and unexpected failures. This blog will explore various maintenance strategies tailored for used machine tools, emphasizing the importance of proactive care in maximizing value. Ultimately, investing time and resources into maintaining these tools will result in significant cost savings and improved efficiency in production processes.
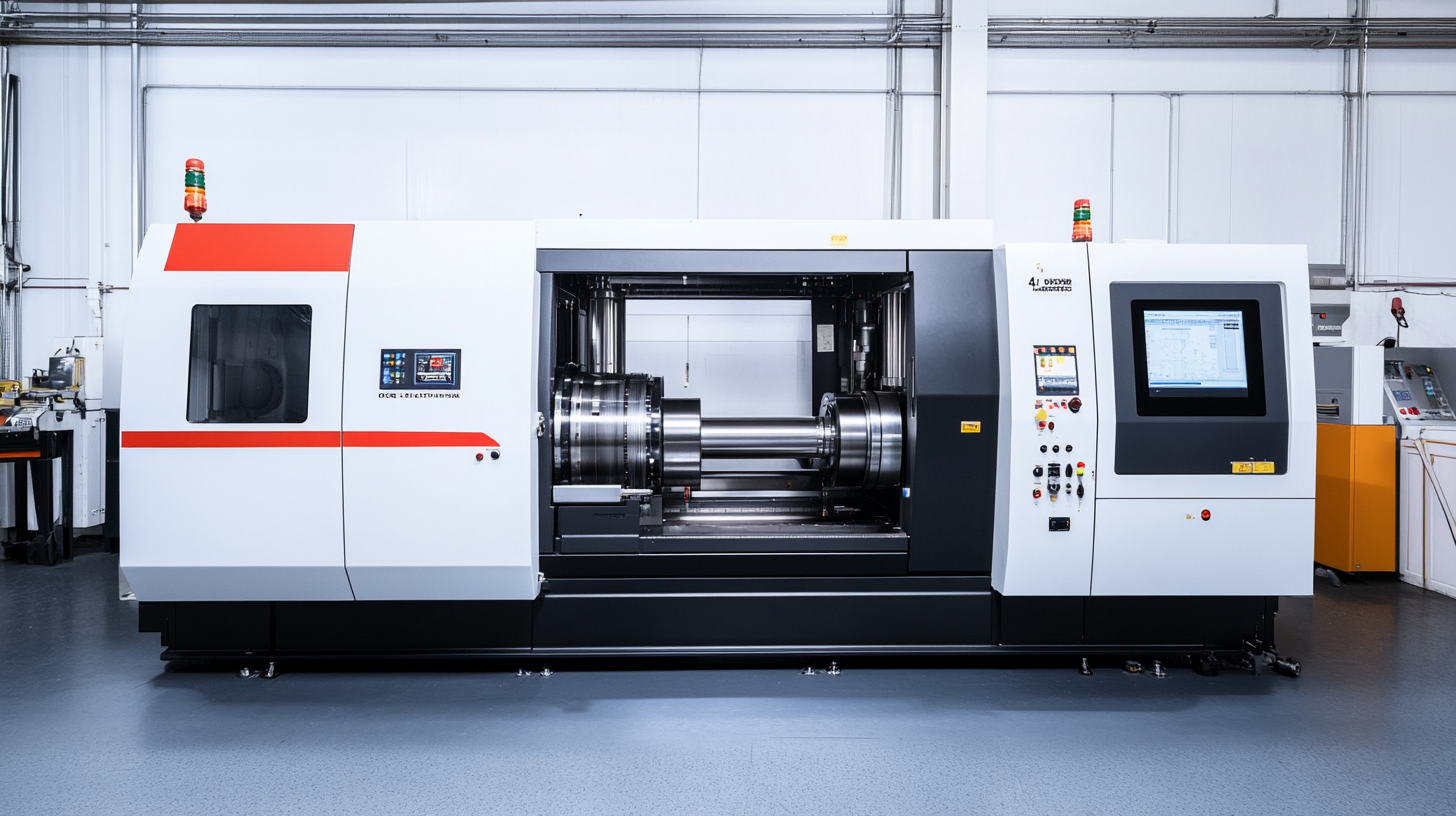
Identifying the Best Quality Used Machine Tools for Your Operations
When it comes to operating a successful manufacturing business, selecting the right quality used machine tools is a critical decision that can significantly impact productivity and profitability. The first step in this process is to understand your specific requirements. This means evaluating the types of materials you'll be working with, the complexity of the parts you need to produce, and your production volume. These considerations will guide you in identifying the right machine tools that fit both your operational needs and budget constraints. Once you've established your requirements, the next step is to source the best quality used machine tools. It's essential to partner with reputable dealers who offer thorough inspections and warranties. Look for machines that have a proven track record in performance and reliability, as this will save you from potential headaches in maintenance and repairs later on. Pay attention to the machine's history, including previous ownership, usage patterns, and any modifications. Machines that have been well-maintained and lightly used are usually better investments. Finally, implementing cost-effective maintenance solutions is crucial to ensure the longevity of your used machine tools. Regular servicing, proper operator training, and timely repairs can prevent costly downtime and extend the life of your equipment. Consider creating a maintenance schedule based on the manufacturer's recommendations and the actual usage of your machines. By prioritizing maintenance and choosing the right tools, you can maximize value and drive your operations toward greater efficiency and success.
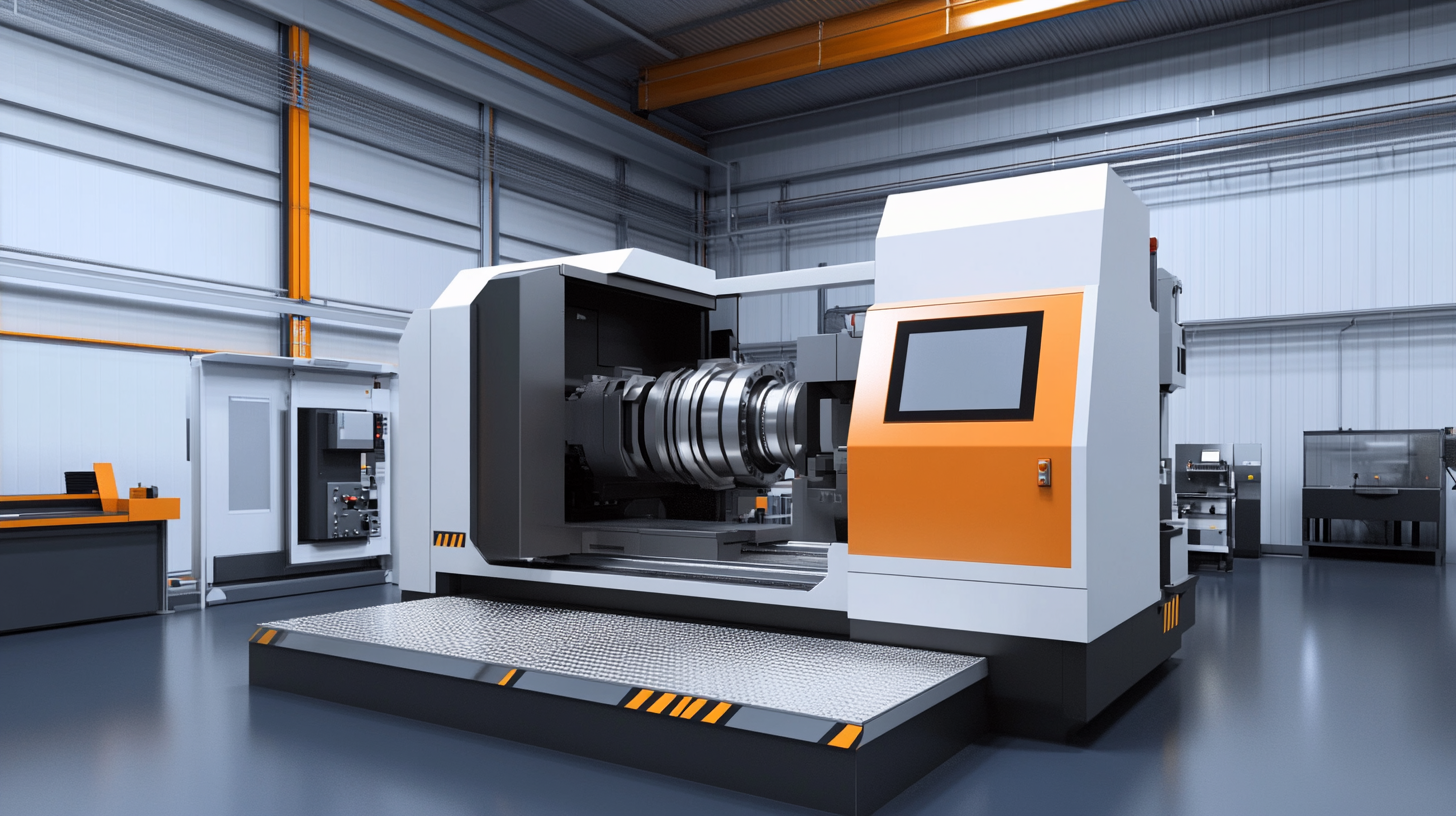
Cost-Effective Maintenance Strategies for Extended Machine Lifespan
Maintaining quality used machine tools is crucial for manufacturers looking to extend their operational lifespan and enhance productivity. Cost-effective maintenance strategies can significantly reduce downtime and repair costs while ensuring that machinery remains in optimal working condition. Implementing a proactive maintenance schedule is one of the cornerstones of a successful strategy. By regularly inspecting and servicing equipment, potential issues can be identified and addressed before they escalate into costly repairs or unplanned stoppages.
In addition to routine inspections, adopting advanced technologies such as condition monitoring can elevate maintenance efforts to a new level. This approach utilizes sensors and data analytics to track machine performance in real time, providing insights that inform maintenance decisions. By understanding the specific needs of each machine, manufacturers can tailor their maintenance strategies, optimizing resource allocation and reducing unnecessary labor costs. This targeted approach not only helps maintain high productivity levels but also extends the machinery's useful life.
Moreover, training operators on best practices for machine care can have a profound impact on longevity. By educating staff about proper usage, cleaning routines, and routine operational checks, businesses can minimize wear and tear caused by user error. When employees are equipped with the knowledge to identify minor issues, they can address them quickly, further safeguarding the integrity of the machinery and ensuring that investments in quality used tools yield maximum returns.
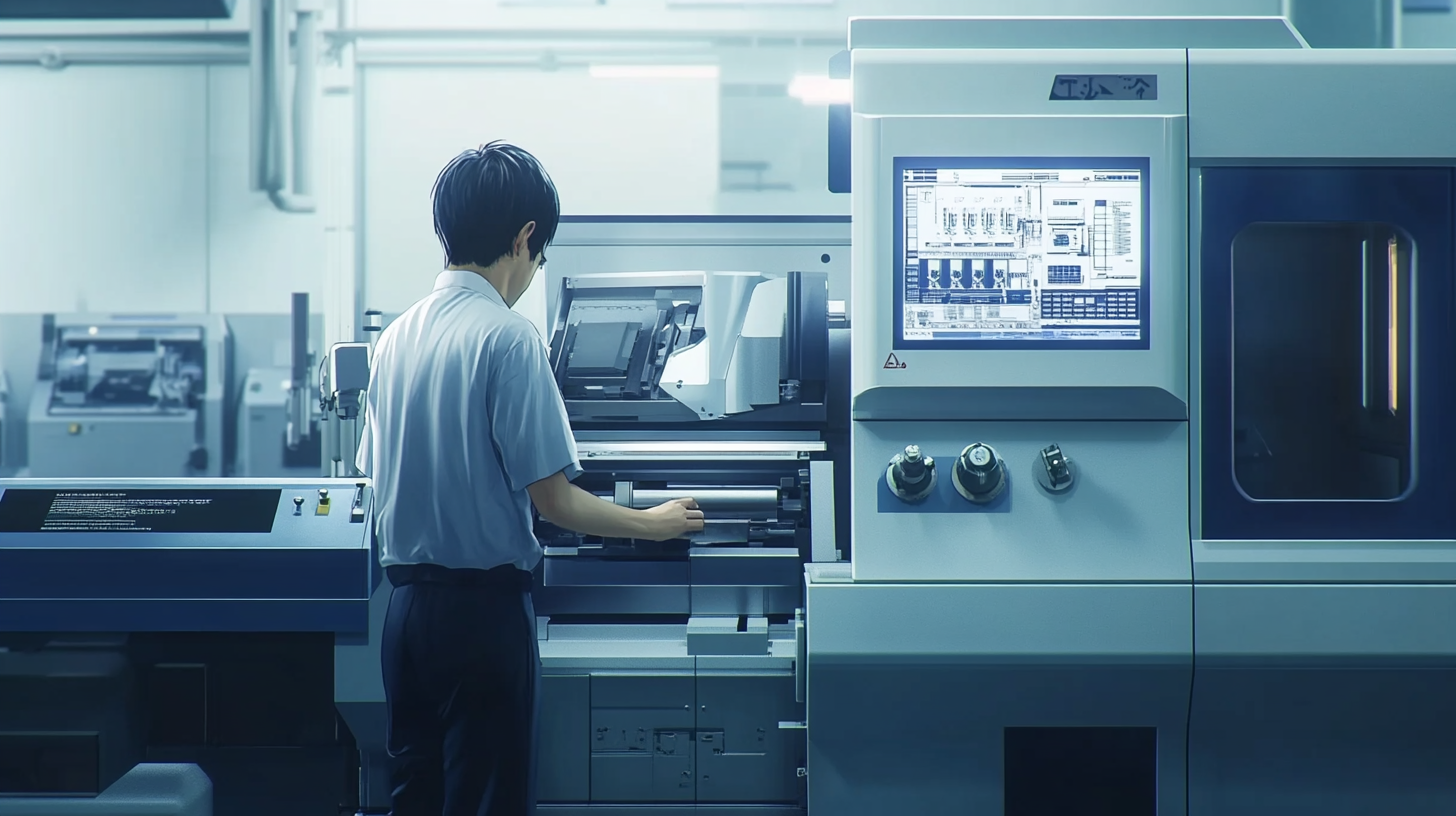
The Role of Regular Maintenance in Maximizing Equipment Performance
Regular maintenance is crucial for maximizing the performance of used machine tools. Without a consistent maintenance program, even the best machines can underperform, leading to increased downtime and reduced productivity. By focusing on routine inspections and timely servicing, operators can identify potential issues before they escalate into significant problems. This proactive approach not only extends the lifespan of the machinery but also ensures optimal operation, allowing for higher quality production and efficiency.
One of the core benefits of regular maintenance is its cost-effectiveness. Instead of facing expensive repairs or replacements due to neglect, investing in a structured maintenance routine can yield significant savings in the long run. For instance, simple tasks such as lubrication, cleaning, and alignment can prevent wear and tear that would otherwise lead to costly failures. Additionally, by keeping machinery in peak condition, manufacturers can avoid production delays that often arise from equipment breakdowns, thereby maintaining their competitive edge in the market.
Furthermore, regular maintenance enhances safety in the workplace. Well-maintained machines are less likely to malfunction, reducing the risk of accidents that can occur due to equipment failure. This focus on safety not only protects the workforce but also fosters a culture of reliability and responsibility within the organization. In summary, committing to a regular maintenance schedule is essential for maximizing the performance and longevity of quality used machine tools.
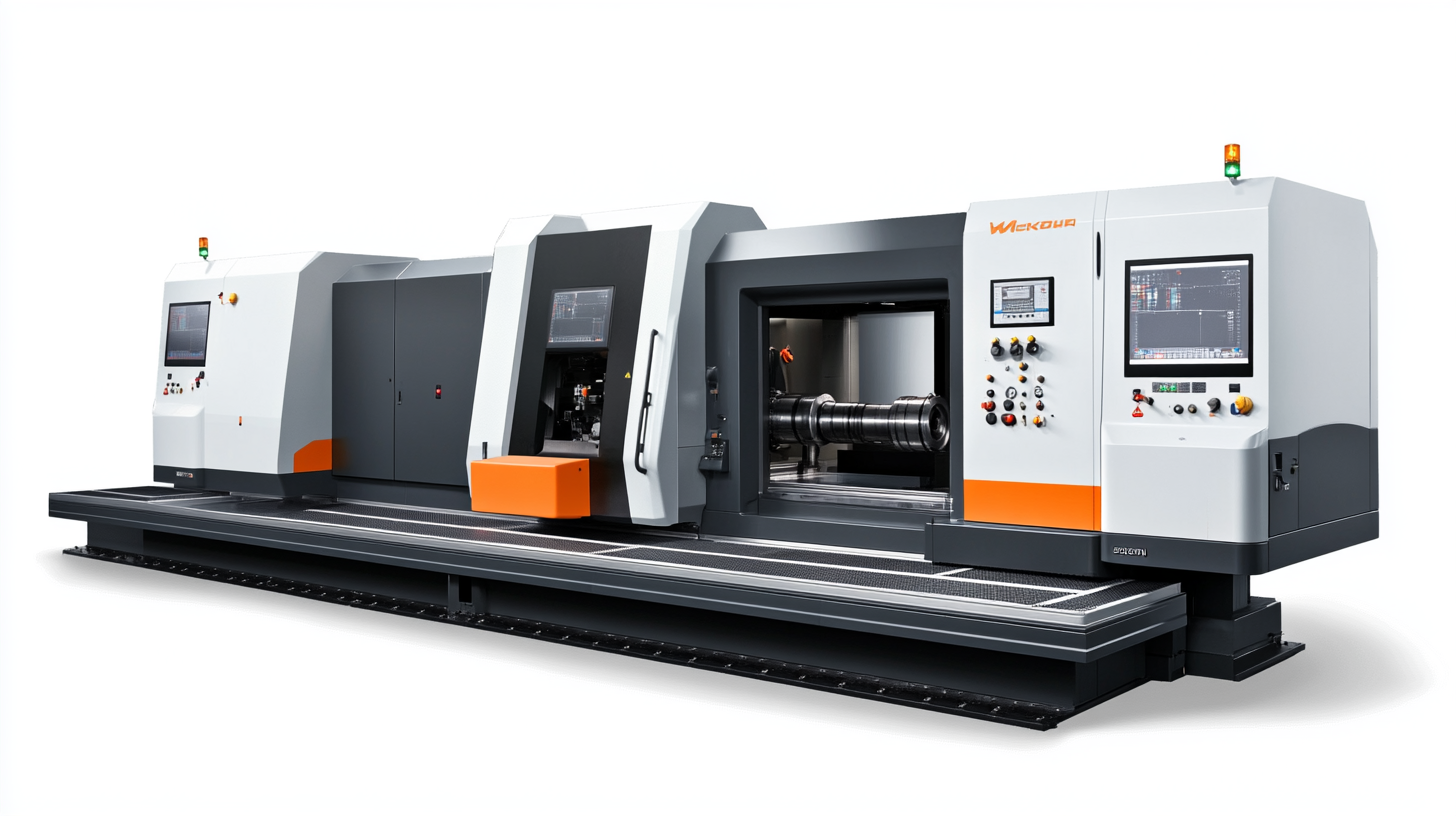
Common Repairs for Used Machine Tools: Preventive vs. Reactive Approaches
In the realm of machine tools, the debate of preventive versus reactive maintenance continues to be a central theme for maximizing the lifespan and efficiency of equipment. Preventive maintenance stands out as a proactive approach, aimed at identifying and addressing potential issues before they escalate into costly repairs. According to industry reports, implementing a robust preventive maintenance strategy can reduce repair costs by as much as 30% while enhancing productivity.
On the other hand, reactive maintenance—often seen as a necessity when unforeseen failures occur—can lead to increased downtime and operational inefficiencies. Research indicates that unplanned downtime can cost manufacturers upwards of $260,000 per hour in lost productivity. Transitioning toward a preventive maintenance model not only mitigates these risks but also embraces advanced technologies, such as AI-driven predictive maintenance. This innovative approach not only forecasts equipment failures with remarkable accuracy but also boosts factory uptime by an impressive 15%, allowing organizations to respond swiftly to maintenance needs.
The integration of AI tools into maintenance strategies is transforming the landscape of equipment management. For instance, in the oil and gas sector, predictive maintenance powered by AI has revolutionized how companies manage their assets, significantly reducing unplanned downtime and optimizing resource allocation. By leveraging data analytics and machine learning, organizations can maintain their used machine tools more effectively, ensuring that they deliver optimal performance while minimizing repair costs.
Building a Maintenance Schedule: Balancing Costs and Operational Efficiency
In today's industrial landscape, balancing costs and operational efficiency is crucial for maintaining the competitiveness of used machine tools. One effective strategy is to develop a comprehensive maintenance schedule that incorporates predictive maintenance techniques. According to the latest research published in the International Journal of Computing and Engineering, machine learning models can significantly improve predictive maintenance in industrial settings, helping organizations to foresee potential equipment failures before they occur. This not only optimizes maintenance operations but also reduces unplanned downtime and repair costs, ultimately enhancing productivity.
To effectively implement a maintenance schedule, companies can leverage advanced tools such as Computerized Maintenance Management Systems (CMMS). These platforms simplify the tracking of maintenance tasks and equipment status, ensuring that organizations can manage their maintenance operations efficiently. By utilizing preventive maintenance software, businesses can plan and schedule regular tasks that keep machinery in optimal condition, thus mitigating the risks associated with equipment breakdowns.
Moreover, the integration of digital twin technology presents a valuable opportunity to enhance operational efficiency and safety. By creating a virtual representation of their machinery, businesses can monitor performance in real-time and make data-driven decisions that prolong equipment lifespan while minimizing overhead costs. As industries continue to evolve, adopting such smart technologies and robust maintenance schedules will be vital for maximizing the value derived from quality used machine tools.