Enhancing Precision and Efficiency in Manufacturing with Tool Room Mills
In the competitive landscape of modern manufacturing, precision and efficiency are paramount for sustained success. According to a report by Grand View Research, the global CNC milling machine market is anticipated to reach USD 100 billion by 2025, growing at a CAGR of 5.6%. This significant growth underscores the increasing reliance on advanced manufacturing technologies, such as Tool Room Mills, which are designed to enhance precision while optimizing operational workflows. Tool Room Mills not only provide the versatility needed for intricate machining tasks but also play an essential role in reducing production time and minimizing waste, ultimately boosting profitability.
The integration of Tool Room Mills into manufacturing operations can lead to substantial improvements in productivity. A study by the Manufacturing Institute revealed that companies adopting advanced tools report up to 20% increased output and a 30% reduction in machining errors. This data highlights the critical role that Tool Room Mills can play in facilitating the high levels of accuracy and speed required in today’s manufacturing processes. As industries continue to evolve, embracing innovative technologies, the strategic deployment of Tool Room Mills will be vital for manufacturers looking to enhance their competitive edge and drive sustainable growth.
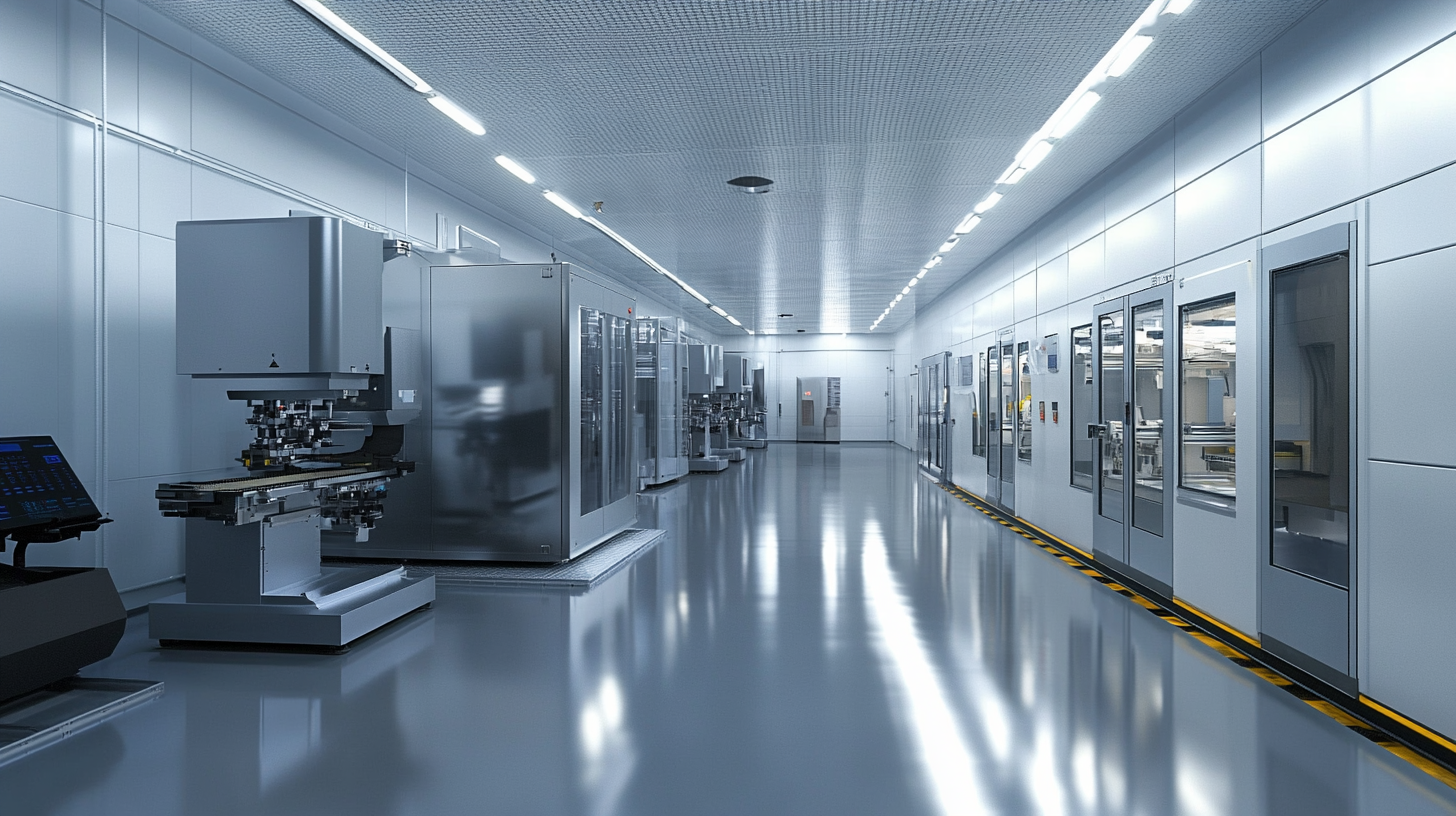
Understanding Tool Room Mills and Their Role in Modern Manufacturing
Tool room mills play a crucial role in modern manufacturing by providing the precision and versatility required for various machining tasks. Unlike standard mills, tool room mills are designed to handle more complex and intricate components, making them indispensable in industries such as aerospace, automotive, and medical equipment manufacturing. These machines typically feature a more robust construction, enabling them to maintain high precision over extended periods, which is vital for producing components with tight tolerances. One of the standout attributes of tool room mills is their ability to perform a range of operations, including milling, drilling, and tapping. This versatility allows manufacturers to streamline their workflows by reducing the need for multiple machines for different tasks. Furthermore, modern tool room mills are often equipped with advanced CNC (Computer Numerical Control) technology, which enhances their capabilities, increases repeatability, and minimizes the risk of human error. As industries continue to seek higher efficiency and accuracy in production, the role of tool room mills becomes increasingly significant in meeting these demands. In addition to high precision and operational versatility, tool room mills contribute to overall cost-effectiveness in manufacturing. By enabling the production of high-quality components in-house, manufacturers can reduce lead times and minimize dependency on external suppliers. This not only enhances flexibility but also supports continuous improvement initiatives, as manufacturers can swiftly adapt to changing designs and market demands. Ultimately, tool room mills are integral to optimizing production processes and driving innovation in today’s competitive manufacturing landscape.
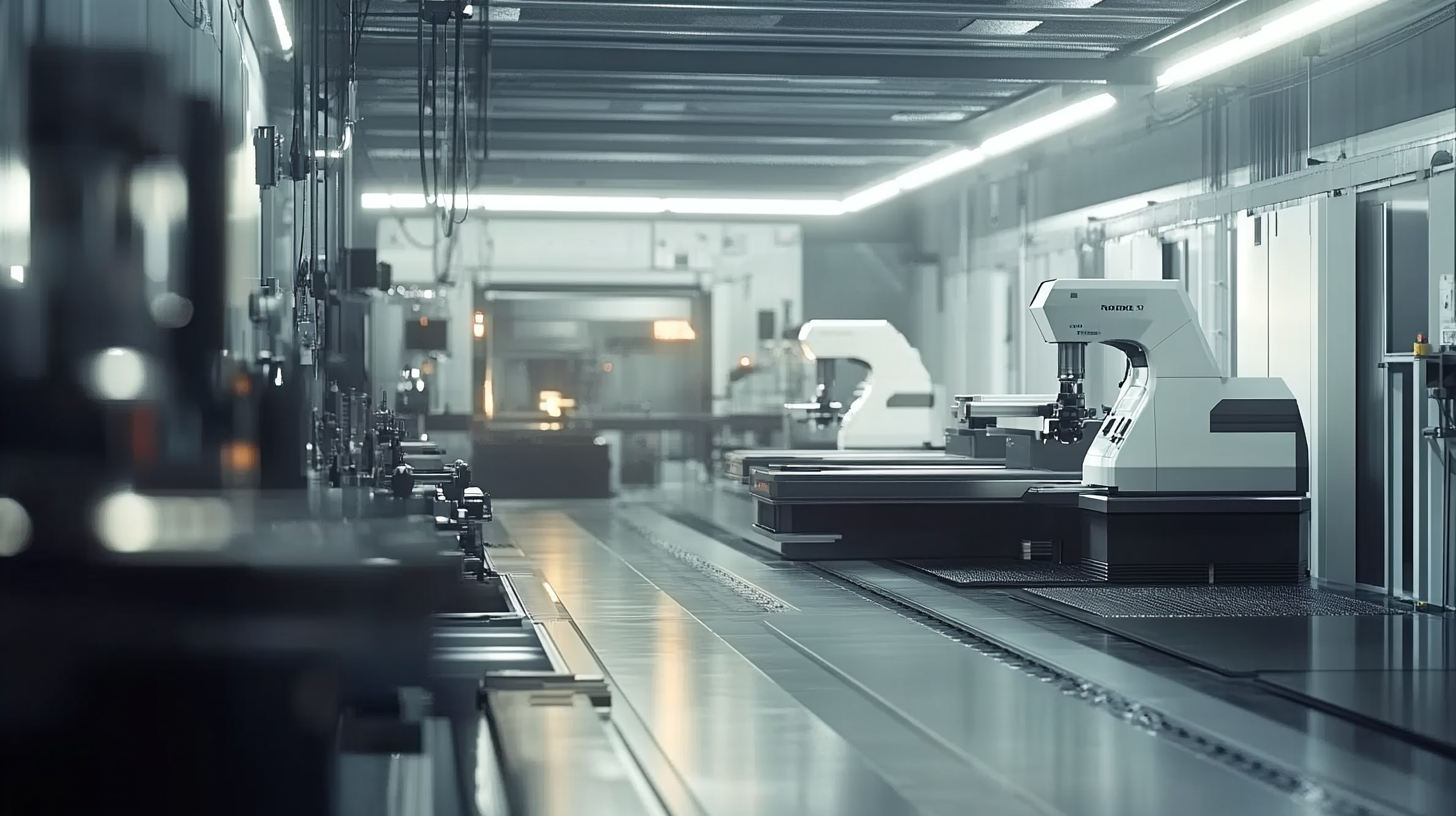
Key Features of Tool Room Mills That Enhance Precision
Tool room mills have become a cornerstone in the manufacturing sector, particularly when it comes to enhancing precision and efficiency. These specialized machines cater to the demanding needs of toolmaking and precision machining, allowing for tight tolerances and high-quality finishes. According to a report by the Manufacturing Institute, the precision machining industry is projected to grow at a rate of 4.5% annually, underscoring the critical role that precision machinery plays in modern manufacturing.
One of the standout features of tool room mills is their advanced CNC (Computer Numerical Control) technology, which facilitates highly accurate machining operations. CNC systems can achieve tolerances as tight as ±0.0001 inches, ensuring that parts meet exact specifications. In an industry where even the slightest deviation can lead to significant costs in rework and scrap, this level of precision is invaluable. Furthermore, many of today's tool room mills come equipped with user-friendly interfaces that simplify the programming process, thereby reducing the time required for setup and increasing overall productivity.
Another crucial characteristic of tool room mills is their versatility. These machines can perform a variety of operations, including milling, drilling, and tapping, all on a single platform. This multi-functionality not only saves space in manufacturing facilities but also minimizes the need for multiple machines, further streamlining production workflows. According to a study by the American Machine Tool Distributors' Association, companies that utilize versatile machine tools report up to a 30% increase in operational efficiency. This capability to switch between tasks without the need for extensive retooling significantly enhances both productivity and precision in manufacturing processes.
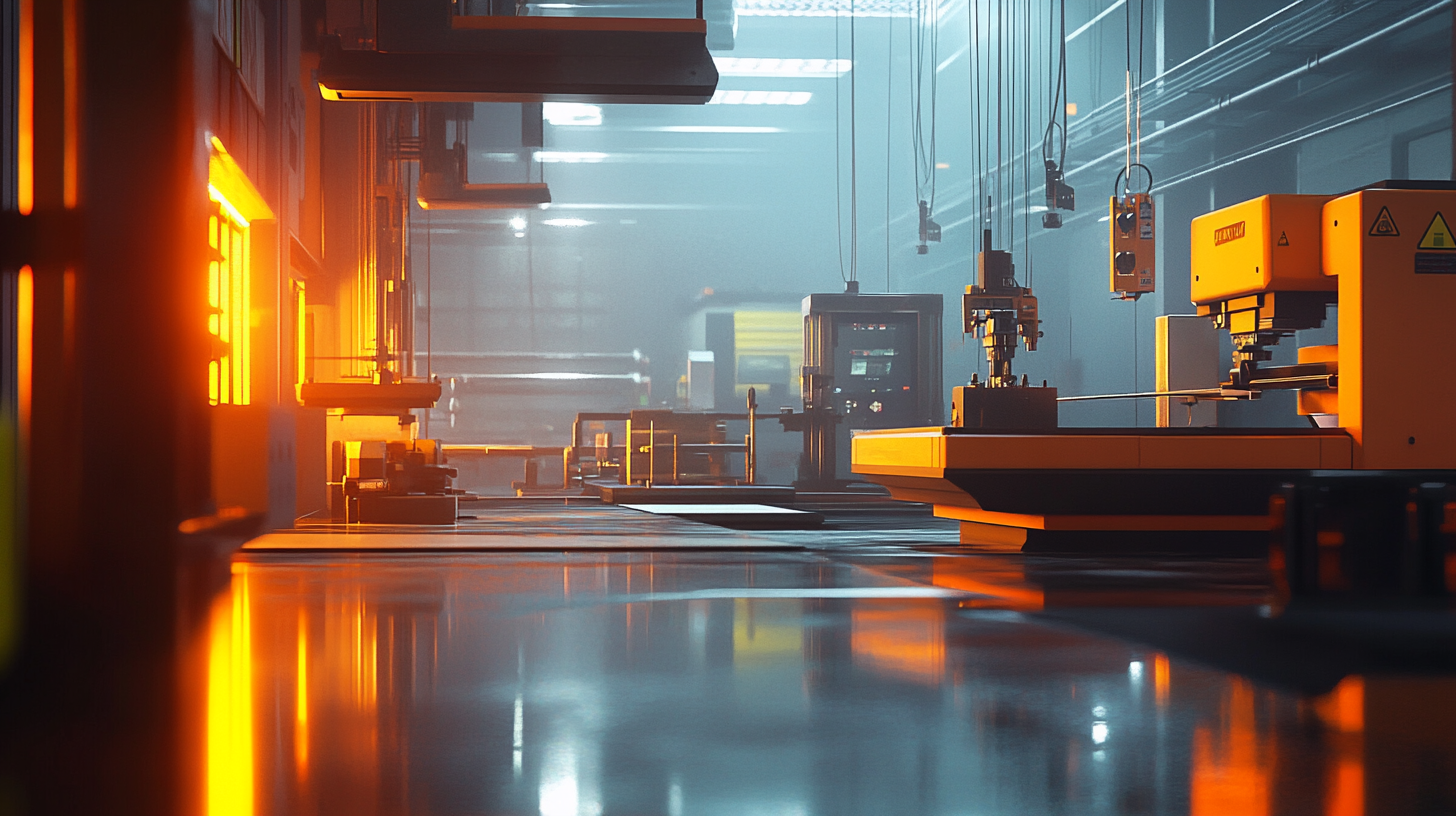
Improving Efficiency through Advanced Tool Room Mill Technologies
The landscape of manufacturing is evolving rapidly, driven by advanced tool room mill technologies that significantly enhance operational efficiency. With the global CNC machine market projected to reach nearly $200 billion by 2032, the emphasis on precision and productivity is more pertinent than ever. Advanced tool room mills are at the forefront, offering manufacturers the capability to streamline their processes. These machines are designed for superior accuracy, enabling intricate designs and reducing waste in production.
Moreover, the integration of cutting-edge technologies such as CAD/CAM has transformed the capabilities of tool room mills. Enhanced algorithms not only optimize tool paths but also extend tool life significantly. This means manufacturers can achieve faster production rates while minimizing downtime and costs associated with tool replacement. As industries face the challenges of supply chain disruptions, the efficiency offered by advanced tool room mills becomes crucial. They empower manufacturers to adapt swiftly to changing demands, ensuring resiliency in production.
In addition, the incorporation of data analytics and digital solutions is paving the way for smarter manufacturing processes. Advanced data analytics provide insights that help identify inefficiencies, leading to better decision-making in production lines. With the rise of technologies like digital twins, manufacturers can simulate operational scenarios and predict outcomes, further enhancing productivity. This technological synergy not only boosts performance but also aligns with sustainability goals, allowing companies to reduce their environmental footprint while maintaining high-quality output.
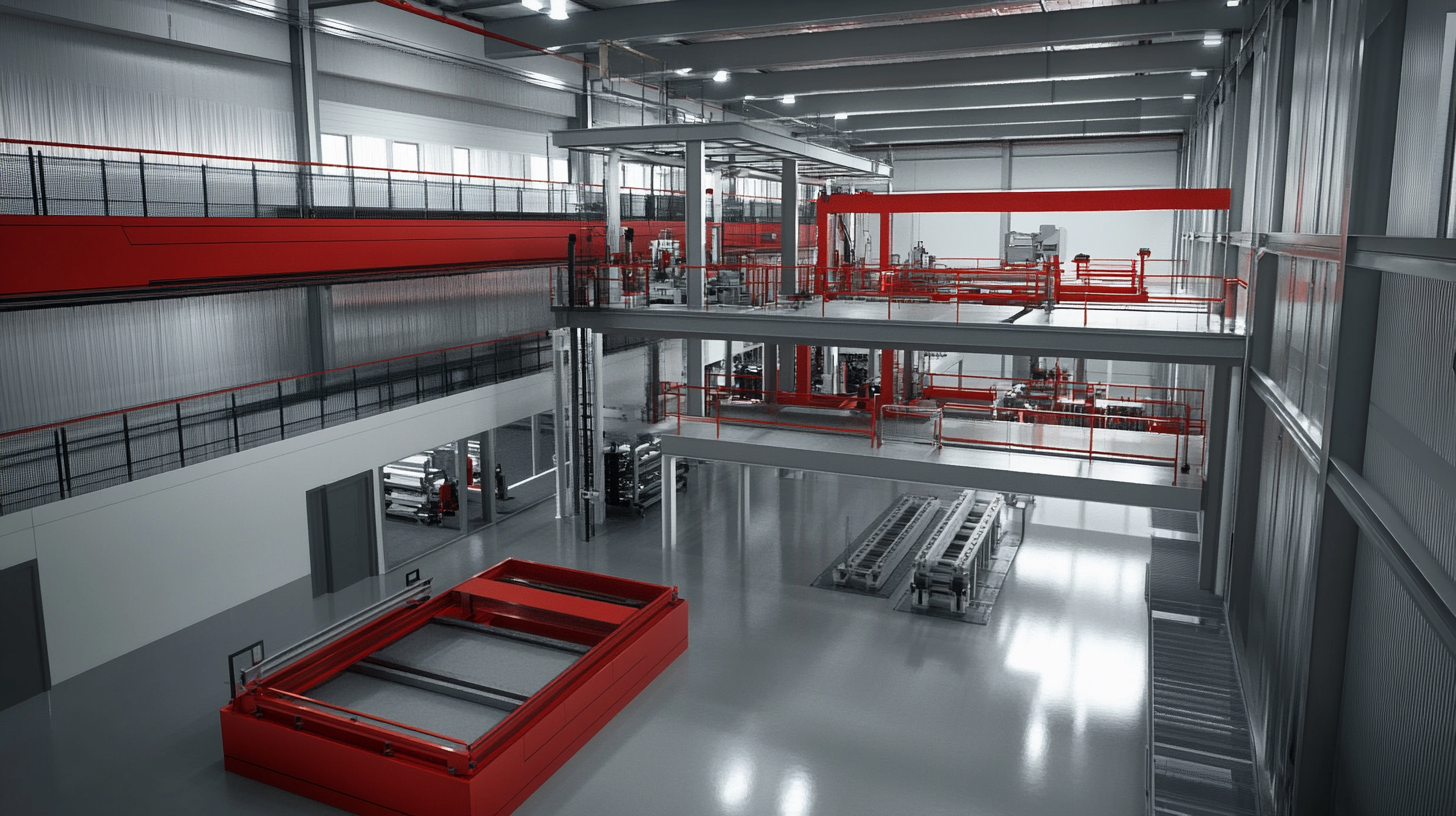
Best Practices for Optimizing Tool Room Mill Operations
In the realm of manufacturing, tool room mills serve as invaluable assets for precision machining. To maximize the efficiency and performance of these machines, implementing best practices is essential. One effective approach is regular maintenance. Establishing a maintenance schedule ensures that machinery components are kept in optimal condition, reducing the likelihood of unexpected breakdowns and costly downtimes. Cleaning and lubricating critical parts can significantly extend the lifespan of tool room mills while maintaining their accuracy.
Another crucial practice is employee training. Skilled operators who understand the capabilities and intricacies of the machinery can make a world of difference in production quality. By investing in comprehensive training programs, manufacturers empower their workforce to utilize the mills effectively, leading to enhanced precision in the outputs. Moreover, encouraging operators to delve into troubleshooting techniques helps mitigate errors during production, further enhancing workflow and efficiency.
Additionally, integrating modern technology such as CNC (Computer Numerical Control) systems can revolutionize tool room mill operations. These systems allow for automated controls that increase precision and reduce human error. By utilizing CAD (Computer-Aided Design) and CAM (Computer-Aided Manufacturing) software, manufacturers can streamline their processes, ensuring that everything from programming to production becomes more efficient. This technological upgrade not only improves the quality of the finished products but also boosts overall operational productivity.
The Future of Tool Room Mills in Smart Manufacturing Environments
The evolution of tool room mills is reshaping the landscape of smart manufacturing, emphasizing precision and efficiency. As industries integrate advanced technologies, the future of these machines lies in their ability to seamlessly operate within a connected environment. The ongoing growth of the CNC machine market signifies a strong investment trend towards automation and digitalization, with projections indicating a remarkable expansion from $101.22 billion in 2025 to $195.59 billion by 2032. This shift highlights the increasing demand for high-quality machining solutions that can enhance production capabilities.
In this context, the introduction of digital-native CNC systems marks a significant advancement for tool room mills. These systems enable job shops to harness data-driven insights, optimizing their machining processes and reducing downtime. The integration of supercomputing and simulation technologies further assists manufacturers in refining their production strategies, ultimately leading to more agile and responsive operations. Noteworthy advancements in tool management also simplify operations, allowing for improved tracking and efficiency, essential for staying competitive in the rapidly changing manufacturing landscape.
As the industry moves toward greater digitization, tool room mills are poised to play a crucial role in realizing the promises of smart manufacturing. With their ability to combine traditional engineering practices with cutting-edge technology, these mills are not only enhancing the precision of manufacturing but also paving the way for future innovations in production techniques. The continuous evolution of these tools will undoubtedly be a key element in the success of modern manufacturing enterprises.