5 Reasons Why Tool Room Mills are Essential for Modern Manufacturing
In the fast-evolving landscape of modern manufacturing, the significance of precision and efficiency cannot be overstated. According to a report by MarketsandMarkets, the global CNC machine market is projected to reach $119.89 billion by 2026, growing at a compound annual growth rate (CAGR) of 6.8%. Central to this technological advancement are Tool Room Mills, which have become indispensable for producing high-quality components with intricate designs. Their ability to perform various machining operations with speed and accuracy makes them a crucial asset in any manufacturing setup.
The versatility of Tool Room Mills allows manufacturers to adapt swiftly to changing demands, thereby enhancing productivity and reducing lead times. In a survey conducted by the National Association of Manufacturers, organizations reported a 30% decrease in production time after incorporating advanced milling equipment into their operations. This ability to integrate cutting-edge technology positions Tool Room Mills not only as tools for efficiency but also as vital instruments in driving innovation within the manufacturing sector. As we delve into the five reasons why Tool Room Mills are essential for modern manufacturing, it becomes clear that these machines play a pivotal role in shaping the future of production.
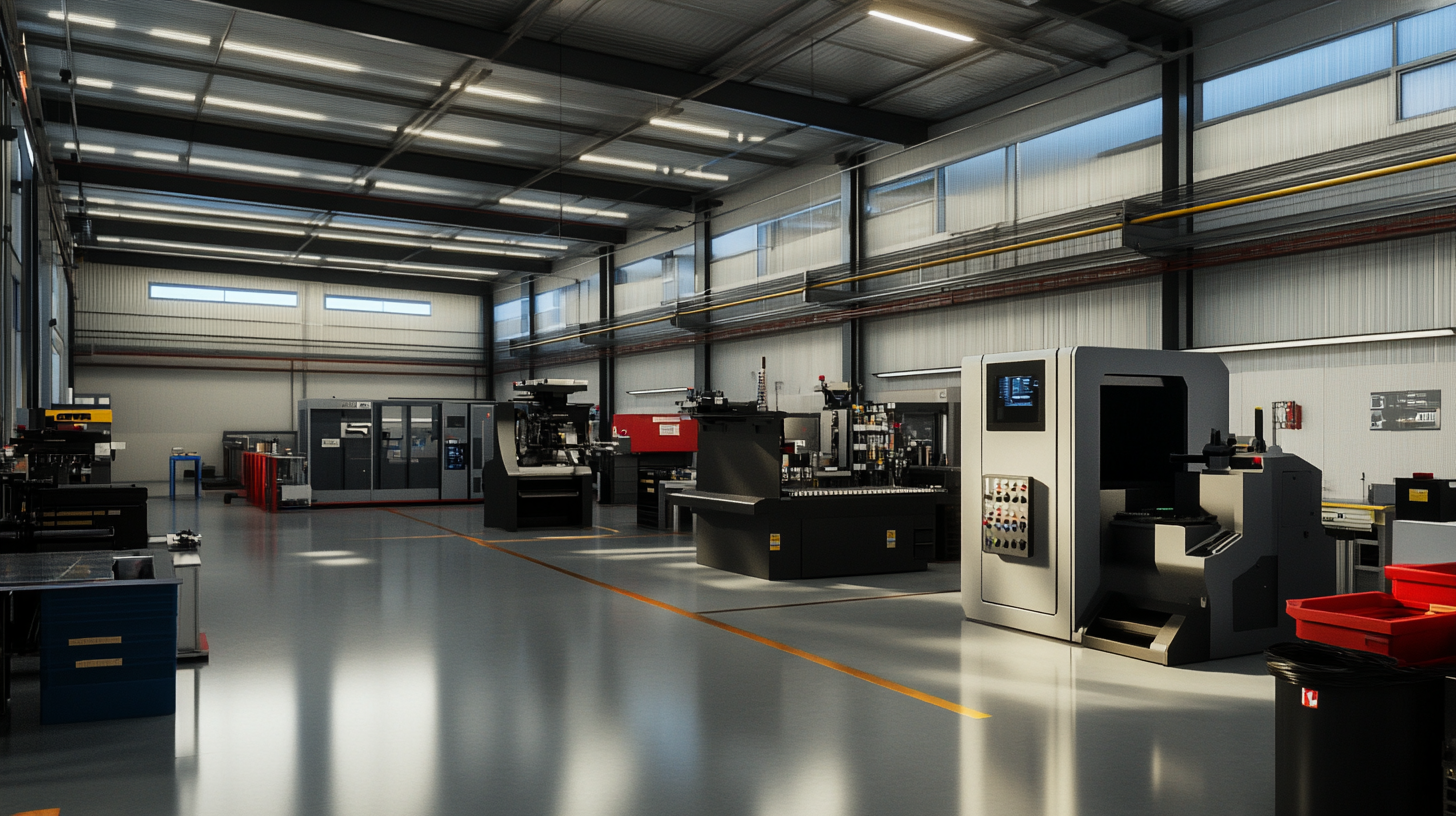
The Versatility of Tool Room Mills in Diverse Manufacturing Sectors
In today's fast-paced manufacturing landscape, the versatility of tool room mills has become a cornerstone for diverse sectors, ranging from automotive to aerospace. Tool room mills facilitate precision machining, allowing manufacturers to produce complex components efficiently. According to a report from the National Association of Manufacturers, precision machining accounts for over 40% of all machining processes, highlighting the critical role that tool room mills play in maintaining high production standards while adapting to the specific needs of various industries. One of the significant advantages of tool room mills is their ability to handle a wide range of materials, from metals like aluminum and steel to advanced composites. A survey conducted by the Association for Manufacturing Technology showed that nearly 75% of manufacturers reported increasing their use of versatile milling machines to enhance productivity and reduce setup times. This adaptability not only streamlines production workflows but also minimizes downtime, enabling manufacturers to keep pace with customer demands for customized and high-quality products. Moreover, the advent of advanced CNC technology has elevated the capabilities of tool room mills, allowing for intricate designs and precision engineering. According to a report by Market Research Future, the global CNC machine market is anticipated to grow to $109 billion by 2026, driven in part by the escalation of precision-driven industries that rely on tool room mills for their manufacturing processes. As manufacturers strive for innovation in product development, the essential role of tool room mills in delivering versatility and adaptability becomes increasingly evident, ensuring that they remain a vital component in the evolution of modern manufacturing.
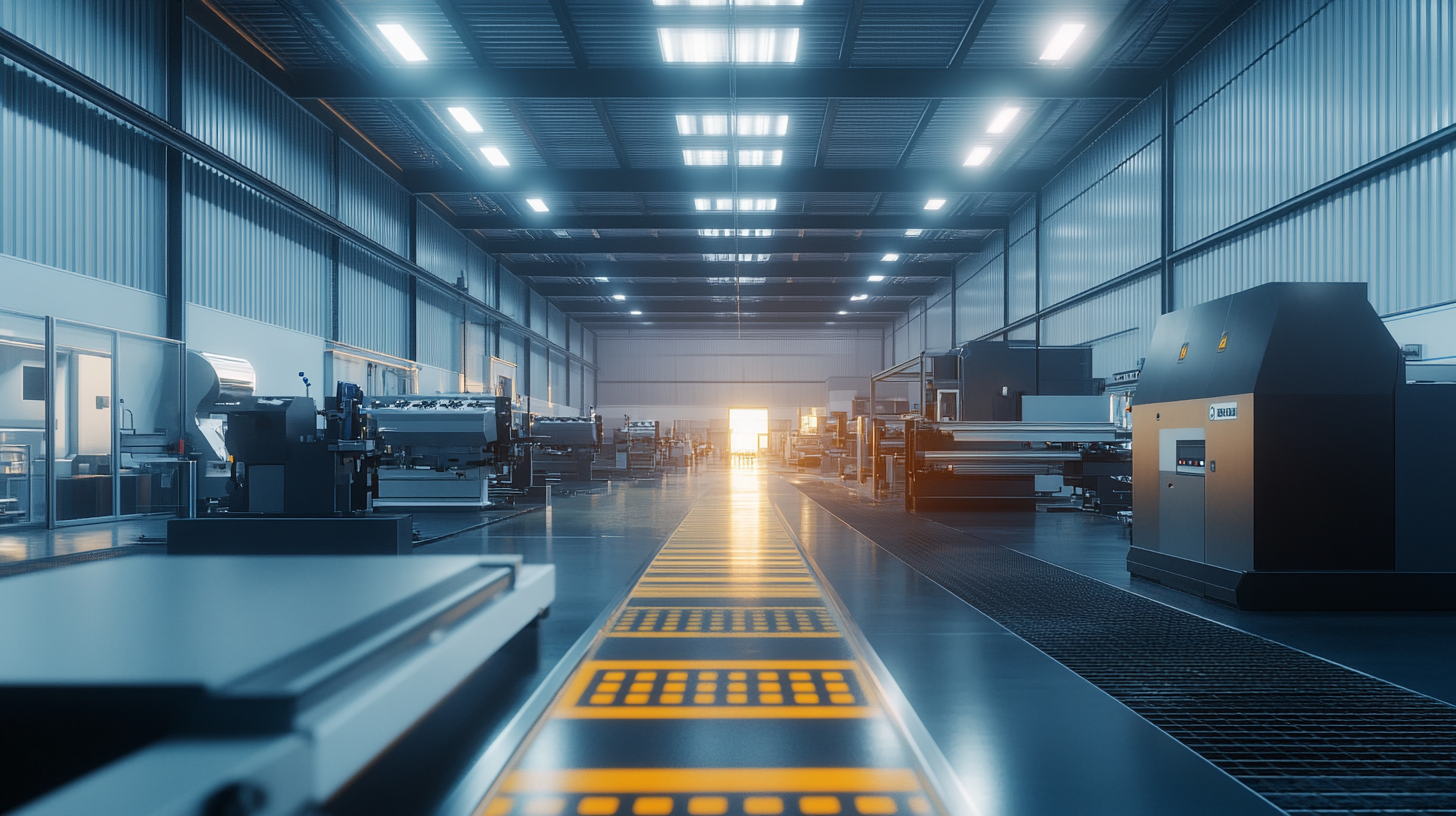
Enhancing Precision: How Tool Room Mills Improve Product Quality
Tool room mills play a vital role in modern manufacturing by enhancing precision and ensuring superior product quality. These machines are designed to operate with a level of accuracy that is crucial for producing intricate components and assemblies. With the ability to manufacture parts to tight tolerances, tool room mills enable manufacturers to meet stringent industry standards, reducing the risk of defects and minimizing waste.
One of the standout features of tool room mills is their versatility. They can handle various materials, from metals to plastics, making them essential in industries ranging from aerospace to automotive. This adaptability allows manufacturers to produce a wide range of high-quality products using the same machinery, increasing efficiency and productivity. Furthermore, the advanced CNC (Computer Numerical Control) technology utilized in tool room mills enhances repeatability, ensuring consistent results across multiple production runs.
Moreover, the precise capabilities of tool room mills facilitate complex machining processes, such as contouring and surface finishing, that elevate the overall quality of the end products. By allowing manufacturers to execute detailed designs with high fidelity, these mills contribute to the creation of components that not only meet but often exceed customer expectations. As manufacturing continues to evolve, tool room mills remain a cornerstone in promoting precision engineering and high-quality production.
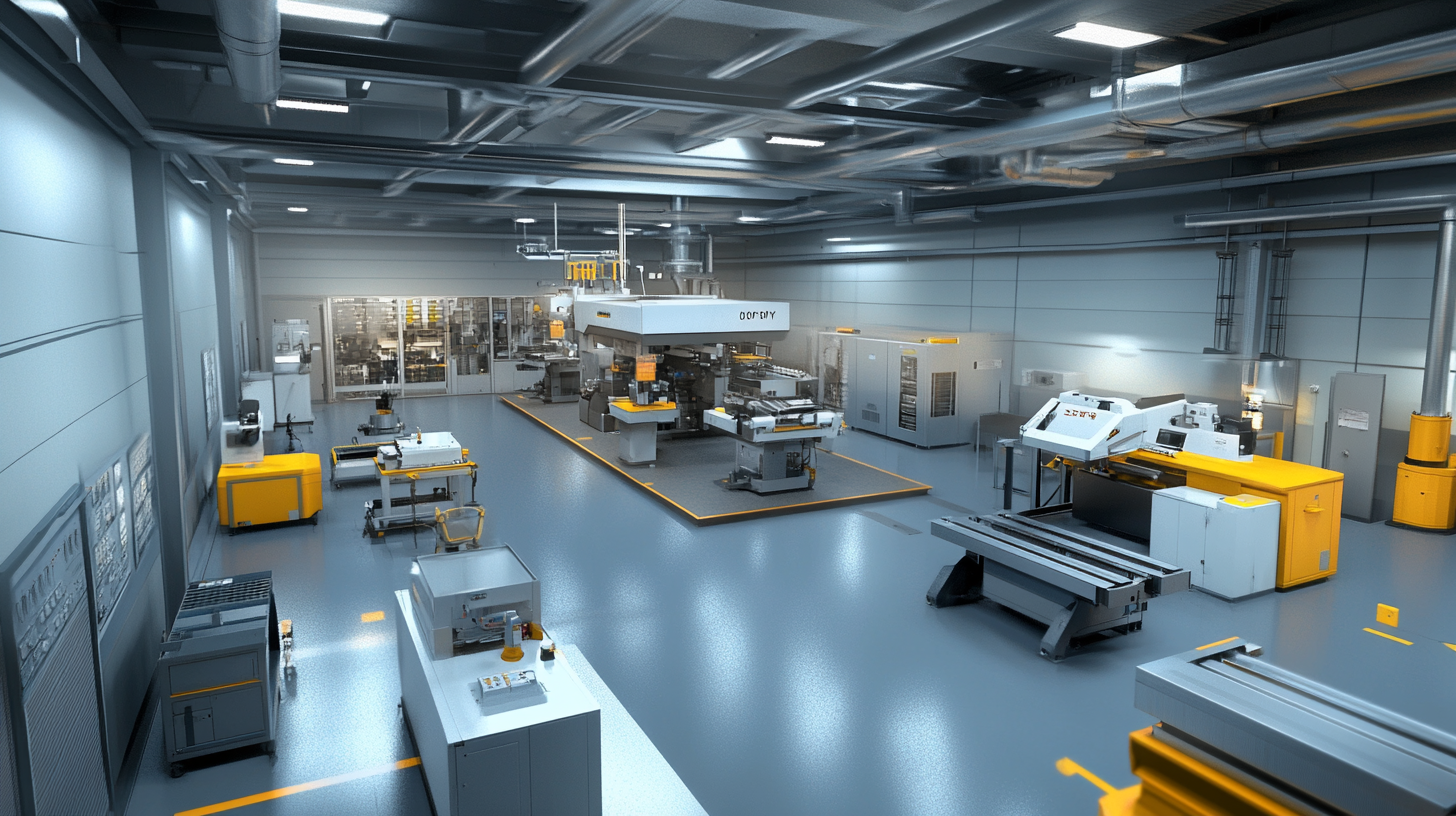
Cost-Efficiency: The Economic Benefits of Using Tool Room Mills
In the current landscape of modern manufacturing, cost-efficiency is increasingly becoming a significant factor that businesses must consider. Tool room mills have emerged as an essential technology that addresses this need. These versatile machines provide the ability to produce high-precision components at relatively low operational costs. According to recent studies, utilizing tool room mills can reduce manufacturing expenditures by up to 30% compared to traditional machining methods, due to their ability to perform multiple processes in a single setup. This not only minimizes labor requirements but also decreases material waste, directly contributing to savings.
Moreover, as industries evolve, the demand for rapid prototyping and custom tools grows. Tool room mills are perfectly suited for this challenge, providing manufacturers the flexibility to create complex parts quickly, thereby minimizing lead times. With advanced CNC technology, these mills can produce intricate designs while maintaining tight tolerances, which is essential in sectors such as aerospace and automotive. A report highlights that companies employing tool room mills have experienced a 20% increase in efficiency in their production lines, showcasing their value in enhancing manufacturing capabilities.
As the manufacturing landscape continues to shift towards automation and sustainability, the adoption of cost-effective tools like tool room mills is pivotal. Not only do they offer a competitive edge in pricing, but their adaptability to high-performance production is unmatched, ensuring that they remain integral to modern manufacturing processes. By integrating these mills into their operations, manufacturers can not only improve their bottom line but also position themselves as leaders in a cost-conscious market.
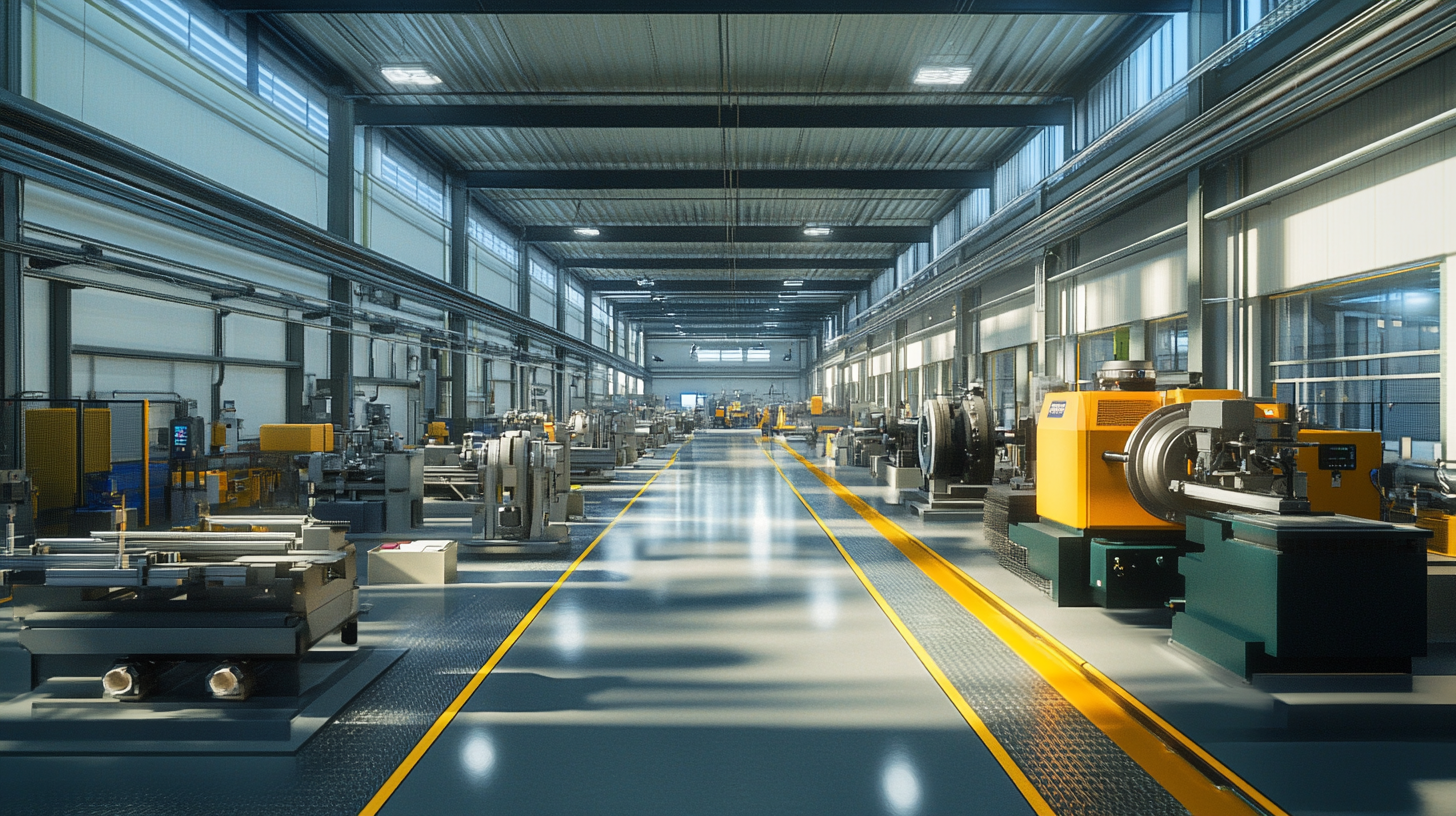
Maximizing Productivity: Tool Room Mills in Streamlined Manufacturing Processes
In the fast-paced world of modern manufacturing, efficiency and productivity are paramount. Tool Room Mills are key players in achieving these goals. They offer unmatched precision and versatility, allowing manufacturers to create complex parts with intricate designs. This capability is crucial for streamlining production processes, reducing waste, and maximizing output. With their programmable features, Tool Room Mills can quickly adapt to different machining tasks, ensuring that production lines remain flexible and responsive to changing demands.
Moreover, the integration of Tool Room Mills into manufacturing workflows enhances operational efficiency. These machines reduce setup time, enabling manufacturers to switch between jobs seamlessly. This capability not only accelerates production cycles but also minimizes downtime, making it easier to meet tight deadlines. By leveraging advanced features like automated tool changers and CNC technology, manufacturers can achieve a higher level of accuracy and consistency, vital for maintaining quality control across different production batches.
Additionally, Tool Room Mills facilitate innovation within manufacturing processes. By enabling rapid prototyping and small-scale production runs, these machines empower designers and engineers to experiment with new ideas without incurring substantial costs. The ability to quickly produce and test components allows companies to stay competitive in a market where innovation is key. As modern manufacturing continues to evolve, the role of Tool Room Mills in optimizing productivity and driving progress will only grow more significant.
Adaptability and Innovation: The Future of Tool Room Mills in Manufacturing
In the ever-evolving landscape of modern manufacturing, tool room mills stand out as a beacon of adaptability and innovation. These machines are not just relics of traditional craftsmanship; they are increasingly being integrated into smart manufacturing systems to meet the demands of today’s fast-paced industry. The versatility of tool room mills allows manufacturers to produce a wide range of components with varying complexities, making them indispensable in multi-functional environments.
The fusion of advanced technology with tool room milling processes is paving the way for a future where customizability is at the forefront. With features such as CNC capabilities, these mills allow for precision machining that can be easily adjusted for different machining operations. This means that manufacturers can swiftly pivot their production lines to respond to changing customer needs and market trends, reducing downtime and maximizing efficiency.
Moreover, the innovation within these machines is not limited to their operations. The integration of software solutions and IoT technology enhances their functionality by providing real-time data analytics and monitoring. This level of feedback empowers manufacturers to make informed decisions, optimize workflows, and minimize waste. As industries lean more towards sustainability, the ability of tool room mills to adapt not only to design specifications but also to environmental considerations showcases their critical role in the future of manufacturing.